In order to promote the understanding and application of the TS16949 standard, the International Automotive Task Force (IATF) has published an application guide for the five core tools to promote their use and dissemination. This article will provide a brief introduction to the five tools for colleagues.
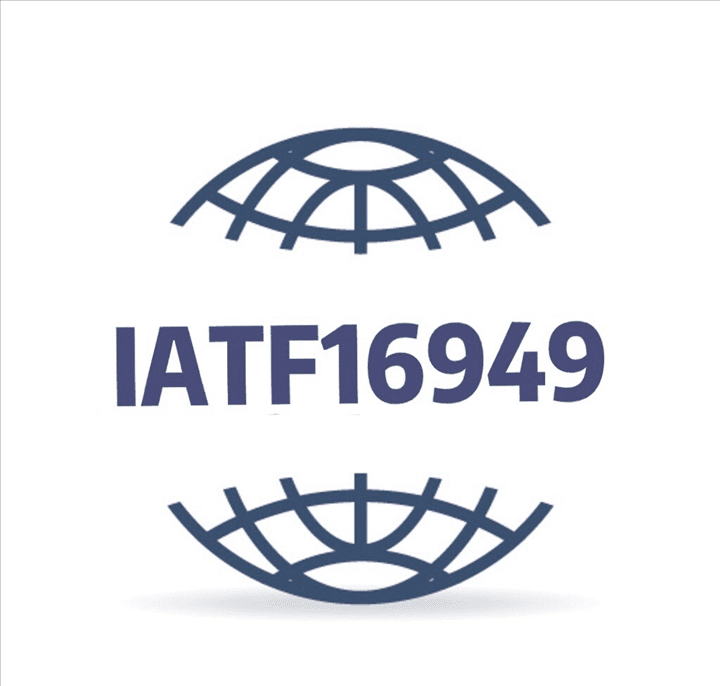
IATF16949 QSM Tools: APQP, PPAP, FMEA, MSA, SPC
The five core tools in IATF16949 refer to APQP (Advanced Product Quality Planning), FMEA (Failure Mode and Effects Analysis), MSA (Measurement System Analysis), SPC (Statistical Process Control), and PPAP (Production Part Approval Process).
They were developed by the three major American automotive companies (General Motors, Ford, and Chrysler) as a reference manual for quality assurance for the QS-9000 standard. Practice has proven that these tools have certain effectiveness in quality management and control, so they are recommended for use in the IATF16949:2016 technical specification.
The “Five Core Tools” refer to the five tools that must be applied in the automotive industry to implement the IATF 16949 standard. Effective application of these tools can help organizations better prevent defects, promote continuous improvement, reduce production costs, and improve product quality.
APQP (Advanced Product Quality Planning)
APQP (Advanced Product Quality Planning) is a structured approach to product quality planning that is used for new or modified product design and new or modified process design. It aims to manage product design and manufacturing process design, determine the steps necessary to achieve customer satisfaction with the product, and provide high-quality products at the lowest possible cost. The goal of quality planning is to ensure product quality and improve product reliability.
The purpose of implementing APQP is to:
- Reduce the risk of quality issues and product recalls
- Improve customer satisfaction by ensuring that products meet their needs
- Improve product and process design by involving cross-functional teams and considering multiple perspectives
- Identify and mitigate risks early in the product development process
- Increase efficiency and reduce waste by designing and developing products and processes with quality in mind
PPAP (Production Part Approval Process)
The Production Part Approval Process (PPAP) is a practical technique that aims to verify, through approved procedures for product validation, that the first batch of products manufactured using production tools and processes meet the technical requirements prior to shipping.
The purpose of implementing PPAP is to:
- Ensure that the supplier has understood all the requirements of the customer’s engineering design records and specifications, and that the potential exists to continuously meet these requirements during the actual production process under the required production cycle conditions.
- The Five Core Quality Tools are at the heart of TS16949 and have been proven to be effective quality tools for the automotive industry. They will play an important role in improving the quality management level and competitiveness of the automotive industry.
SPC (Statistical Process Control)
SPC stands for Statistical Process Control, which is a manufacturing control method that collects data on control items in the manufacturing process based on their characteristics, and uses process capability analysis and process standardization to identify abnormalities in the process and immediately take improvement measures to restore the process to normal.
The purpose of implementing SPC is to:
- Make reliable evaluations of the process;
- Determine the statistical control limits of the process, judge whether the process is out of control and whether the process has the capability;
- Provide an early warning system for the process, monitor the process in a timely manner to prevent the occurrence of waste;
- Reduce reliance on routine inspections, and replace a large amount of testing and validation work with timed observations and systematic measurement methods.
MAS (Measurement Systems Analysis)
MSA is the use of statistical methods to analyze the bias and variance of a measurement system, to determine whether the measurement system is in a statistically controlled state, and to evaluate the capability and performance of the measurement system. The application of MSA is to all measurement systems involved in the control plan.
The purpose of implementing MSA is to:
- Identify and quantify sources of variation in the measurement system
- Evaluate the measurement system’s accuracy, precision, and stability
- Identify opportunities for improvement
- Establish a baseline for measurement performance
- Monitor the system over time and detect changes or improvements.
FEMA (Failure Mode and Effect Analysis)
FMEA, as a planning tool for preventive measures, aims to identify and evaluate potential failures and their consequences in products/processes; and to find measures to avoid or reduce potential failures and continuously improve them.
The purpose of implementing FMEA is to:
- Easily and low-costly modify products or processes to reduce the risk of post-modification crisis;
- Find measures to avoid or reduce potential failures.
IATF16949 Five Core Tools Relationship
This topic can be difficult to understand for someone without practical experience, and even for those with practical experience, it may be hard to understand, because they are interrelated. The classic APQP network diagram, which took Ford a hundred years to draw, shows the most meticulous approach. Here, I will give a brief description of the five core tools in the hope of providing a basic understanding.
APQP is a complex process that must be done by a component company when providing new products to the OEM. Its purpose is to solve all problems before production of the product begins. Therefore, it is a process that requires several back-and-forth iterations to achieve the final planning results.
FMEA is a failure mode analysis performed in the second and third stages of APQP, including products and processes. The most important point here is that the product has not yet been produced, and it is a potential possibility analysis. Many companies are not used to this point and often analyze it as a product already in production.
SPS and MSA are things that are formed during process planning. In other words, what kind of process needs to be controlled using SPC. Generally speaking, processes with special characteristics should use SPC, but this is not absolute. It is necessary to mention that the control plan is the result of APQP planning, and the measurement tools involved in the control plan should all be subjected to MSA. During the initial control plan, that is, the trial production control plan, the planned measurement tools or selected SPC may not have good results, so adjustments and improvements may be made, and the final production control plan is formed. The SPC and MSA in the final production control plan should be able to meet the needs of mass production.