The pursuit of zero defect is one of the objectives of lean quality management. Different people have different views on zero defect of lean management. There are five misunderstandings about zero defect of lean management.
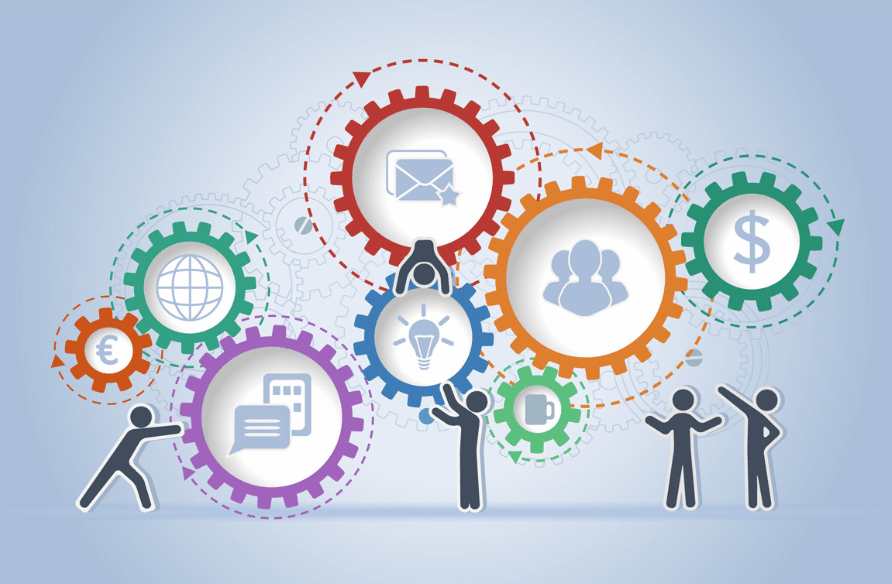
5 Misunderstandings for Lean Quality Management Zero Defects
Misunderstanding 1: Zero defect is only a quality management method
There are many, many methods of quality management, which is dazzling, but zero defect is just one of them. So is it necessary to do it? Zero defect symbolizes a new quality revolution and a new symbol of quality culture; If we only regard it as a method in the quality jungle, we will lose many development opportunities, because zero defect is the practical guide to guide the development of enterprises. If we insist that it is a method, then it is a method to change the outdated quality culture and the way of enterprise operation.
Misunderstanding 2: Zero defect is the goal or the result?
It is one of the most misunderstood problems. Because of the misunderstanding of zero defect, many people often regard zero defect as the goal rather than the result; The bad thing is that as a goal, there is always a voiceover: it is just a goal that is pursued continuously, and it is impossible to achieve. It is just something that inspires many people. Therefore, zero defect also clearly reflects the integrity of an organization or individual. It is not a total problem of a little more, but a product quality problem of conformity or non conformity; One is probability theory connected by relative words such as “possible” and “maybe”, and the other is philosophy of making choices by absolute actions of “Yes/No”.
Misunderstanding 3: Zero defect is only applicable to manufacturing industry
People with this perception are usually engaged in quality control or service industry. They often assume that “defects” are related to manufacturing or blue collar workers. The danger of this misunderstanding is that zero defect is regarded as a screwdriver on the production line, not as a scalpel for tissue and body. Although the concept of zero defect originated from the manufacturing industry, Crosby has developed it into a quality philosophy that can be applied to all businesses since 1965. At the same time, many practitioners have appeared in the financial, insurance, medical, hotel, and even rental companies of ITT. Whether it is the service industry or the manufacturing industry, to change these current situations, we must use the zero defect work standard as the practice guide, and treat the daily business and relationship with the principle of doing right the first time. After all, the division of blue collar and white-collar workers was just a game before the 1980s, which did not help enterprises’ external “integrity and satisfaction”.
Misunderstanding 4: The management thinks that the quality department should be responsible for zero defect
If the senior management of a company holds this attitude, the reason must be either incomprehension or misunderstanding. It is wrong not to know, but misunderstanding and stubbornness are the most terrible. Obviously, they regard zero defect as a quality management method, and the quality management is in the charge of the quality department. Therefore, zero defect should be in the charge of and promoted by the quality department. This is a typical traditional quality logic. This will inevitably lead to confusion in the quality department. Once managers understand that zero defect is the performance of excellent culture and the cost and competitiveness of enterprises, they will naturally be brave to take corresponding responsibilities.
Misunderstanding 5: Our quality level is very high, so there is no need to do zero defect
On the surface, this seems to be the opposite of the previous question, but it is actually the front and back of the same coin. There is a saying that when the moon is full, the water is full, and the greatest sorrow for management is complacency. When we understand that zero defect is a double-edged tool for enterprise market competition – customer satisfaction, employee/shareholder satisfaction and supplier satisfaction on the one hand, and cost reduction and profit increase on the other. Then we must readjust our mentality, hand over the standards for evaluating the quality level to the market and customers, and regard quality management as a complete, dynamic and endless process.
To achieve the goal of zero defect in lean production management, the management and even the whole staff need to change the traditional ideas and take zero defect not only as a goal, but also as a matter of the quality management department. At the same time, lean zero defect is also a dynamic and continuous process. The above five mistakes of zero defects in lean management are common in many of our enterprises. Only by changing the concept in terms of cognition can we further implement the goal.