What are the commonly used tools of quality management systems? Each tool and method has a lot of content and covers a wide range. In this article, we’ll cover 5 quality management tools including APQP, SPC, FMEA, MSA, and PPAP., as well as what benefits they can provide.
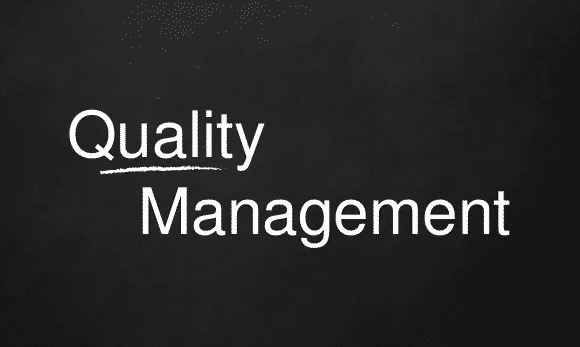
5 Tools of Quality Management System
1. APQP
APQP (Advanced Product Quality Planning), is a structured method used to determine and formulate the steps required to ensure that a product satisfies customers. The goal of product quality planning is to promote contact with everyone involved to ensure that the required steps are completed on time. Effective product quality planning depends on the commitment of the company’s senior managers to strive to achieve the purpose of customer satisfaction.
Benefits of Advanced Product Quality Planning:
- Guide resources to satisfy customers
- Facilitate early identification of required changes
- Avoid late changes
- Provide high-quality products in time at the lowest cost
2. SPC
SPC (Statistical Process Control), mainly refers to the application of statistical analysis techniques to timely monitor the production process, scientifically distinguish the random fluctuation and abnormal fluctuation of product quality in the production process, so as to give early warning to the abnormal trend of the production process, so that the production management personnel can take measures in time to eliminate the abnormalities, Restore the stability of the process, so as to improve and control the quality. SPC is very suitable for repetitive production processes. It can help organizations make a reliable evaluation of the process, determine the statistical control limit of the process, and judge whether the process is out of control and whether the process is capable; Provide an early warning system for the process, timely monitor, the process to prevent the generation of waste products, reduce the dependence on a routine inspection, and replace a large number of detection and verification work with regular observation and systematic measurement methods. The implementation of SPC has been divided into two stages: the analysis stage: using control chart, histogram, and process capability analysis to make the process in statistical steady-state and make the process capability sufficient. Monitoring stage: use a control chart to monitor the process
Benefits of Statistical Process Control:
- Reduce costs
- Reduce defect rate, rework and waste
- Improve labor productivity
- Provide core competitiveness
- Win a wide range of customers
3. FMEA
FMEA (Failure Mode and Effects Analysis) refers to the analysis of potential failure modes and consequences. In the planning and design stage of products/processes/services, FMEA is to analyze the subsystems and parts constituting products and the procedures constituting processes and services one by one, find out potential failure modes, analyze their possible consequences and evaluate their risks, so as to take measures in advance, It is a systematic activity to reduce the serious procedure of failure mode and reduce its possible probability, so as to effectively improve quality and reliability and ensure customer satisfaction. FMEA types include: according to their application fields, common FMEA include Design FMEA (DFMEA) and Process FMEA (PFMEA), system FMEA, application FMEA, procurement FMEA, and service FMEA.
Benefits of Failure Mode and Effects Analysis:
- Reduce development time and cost
- Improve quality, reliability, and safety
- Early identification of single failure points and system interface problems
- Reveal areas needing improvement
4. MSA
MSA (Measurement System Analysis), MSA measurement system analysis uses mathematical statistics and chart methods to analyze the error of the measurement system, so as to evaluate whether the measurement system is suitable for the measured parameters and determine the main components of the measurement system error.
Benefits of Measurement System Analysis:
- Statistical and scientific
- Suitable for continuous and discrete data
- Achieve a low percentage of error
- Assess the correctness of the measurement system
5. PPAP
PPAP (Production Part Approval Process) is a control procedure for production parts and a management method for quality. PPAP production part submission guarantee: mainly including production part dimension inspection report, appearance inspection report, function inspection report and material inspection report; Add some parts control methods and supplier control methods; Mainly manufacturing enterprises require suppliers to make PPAP documents and first article when submitting products. They can only submit PPAP documents after all PPAP documents are qualified; the report also should be submitted after engineering change.
Benefits of Production Part Approval Process:
- Reduce the cost of poor quality
- Ensure parts conform to customer requirements
- Maintain part design integrity
- Identify issues beforehand