Consumers’ demand for quality and fashion has led to a series of changes in the manufacturing field. The most obvious is that the quality control standard of products is becoming more and more strict. These changes put forward higher requirements for the detection industry. The traditional measurement or detection equipment (such as three coordinates, laser tracking, etc.) is not only expensive, but also the measurement and detection process is very cumbersome and time-consuming. In this guide, we discuss about the application of 3D scanning in quality control.
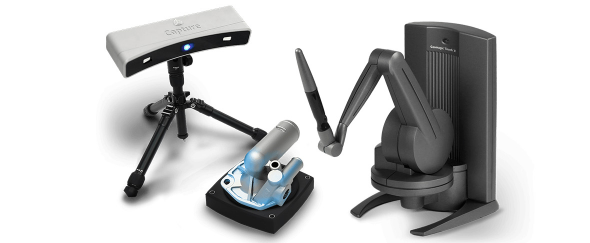
Application Of 3D Scanning In Quality Control Direction
Using the 3D scanner or photogrammetry system to obtain the 3D point cloud data of the product and cooperate with the special 3D detection software to quickly detect the shape of the product can achieve the purpose of quality detection and improve the product quality. The point cloud data obtained by the three-dimensional scanner can also be seamlessly connected with the dot data of the traditional articulated arm measuring machine and the three coordinate measuring machine. The cooperative application of a variety of measuring equipment can solve the measurement and detection problems of various complex workpieces, and the detection time is greatly shortened.
The technical process only completes the three-dimensional inspection of the workpiece in 4 steps, with a high degree of automation in the whole process:
- 3D scanning, or use 3D scanner to obtain 3D scanning data;
- Import 3D scanning data into the detection software and the original CAD design model to align automatically in multiple ways;
- The detection software creates the deviation color map and measures the dimension and tolerance (GD & T);
- Automatically complete the test report and then display the test results.
In terms of technology, it also has outstanding advantages, such as automatic detection, high-precision processing and fast. Regardless of the size and complexity of the workpiece, the average detection is within 15 minutes. It has strong compatibility, supports data from 3D scanners, measuring arms, tracking equipment and CMM, and can easily align coordinate systems from multiple measuring instruments.
In the production process, only by strictly controlling the quality in all links can we finally achieve zero defects.
The advantage of three-dimensional scanning is:
- The detection efficiency is greatly improved, and the detection of multiple parts in the same batch can realize batch detection.
- It reduces the situation of missing inspection and wrong inspection in the detection process, and can be corrected in time.
- The special skill requirements for testers are relatively low, the operation is simple and easy to start.
- Pdf report can be output to intuitively express the measurement data and measurement position.
Here are three examples to give you an intuitive impression.
Case 1: Application of three-dimensional scanning in the inspection of large pressure vessels
Now many companies have high requirements for product accuracy. Due to the large size of pressure vessel products, it is difficult to control the detail size of head parts in the production process, and there are a series of quality problems such as appearance deformation caused by metal rebound and mismatched installation hole position. Because the manual detection process is cumbersome, the speed is slow, the workpiece is difficult to move, and there are some problems such as missed detection, a high-precision handheld laser scanner can be selected for the detection of pressure vessels.
The detection process is roughly as follows: first, conduct on-site scanning, which can be completed in about ten minutes without labeling points. Then, after scanning, the data map is produced for detection and analysis. The detection results show that the product is distorted and deformed, and the local area error exceeds 2.5mm. It is determined that the processing error is too large and needs to be returned to the factory for repair.
Case 2: Application of 3D scanning technology in geometric tolerance analysis
This case is mainly aimed at electric switch manufacturing enterprises. The switch products are plastic parts with upper and lower covers. Due to uncertain interference factors such as thermoplastic deformation during plastic manufacturing and molding, the final assembly effect will be affected. In order to ensure the accuracy of the final product, it is necessary to evaluate the geometric tolerance of a series of key assembly positions and the coincidence of relative mating dimensions. In the past, the conventional detection method of the industry was to manually measure the spatial dimension, which needed to be equipped with many shape and position tolerance detection instruments, square box, deflection instrument, feeler gauge and roundness instrument. The processes were numerous and complex, the professional requirements for users were relatively high, and the detection efficiency was too low.
Case 3: Detection of automobile tire vulcanization capsule by three-dimensional scanning
In the process of tire manufacturing, in addition to the important significance of forming process to tire balance, vulcanization process is also very important.
Tire vulcanization capsule is a tool for tire vulcanization. The capsule is expanded by filling compressed air, nitrogen or superheated water inside to support the tire rubber embryo to form an internal pressure vulcanized tire. If the wall thickness of the capsule is unstable and uniform, it will lead to uneven stress, directly affect the final shape of the finished tire and affect the balanced passing rate of the tire.
The inner and outer wall data of tire vulcanization capsule can be directly collected by hand-held three-dimensional scanner, and the measurement is fast and accurate.