In the shipbuilding industry, 3D laser scanning technology can be used for ship manufacturing and assembly scanning, ship deformation analysis, on-board scanning, on-board facility upgrading, maintenance, measurement and design services. In this guide, we cover the importance and applications of 3D scanning technology in the shipbuilding industry.
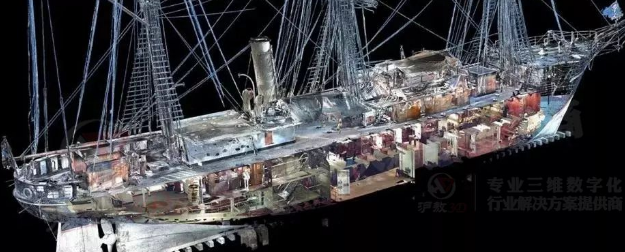
What Is 3D Scanning Technology
Compared with traditional surveying and mapping technology, 3D laser scanning technology can realize the accurate position, shape and size of objects in 3D space, and is superior to traditional surveying and mapping technology inaccuracy, spatial relationship and integrity. 3D laser scanning, also known as real scene replication technology, is a reverse modeling technology. It does not need engineering drawings and has low requirements for the environment, which provides a guarantee for saving the overall operation time.
Why Choose 3D Scanning – Importance Of 3D Scanning For Shipbuilding Industry
The aerospace ship is a high-tech strategic industry and the engine of national cutting-edge technology development. Aviation and navigation technology is related to all aspects of the country and people’s life. Any small accident may cause irreparable huge losses. Therefore, the quality must be strictly controlled. At the same time, with the continuous progress and improvement of industry technology, how to improve innovation ability and means is an urgent problem for Chinese enterprises. Three-dimensional measurement technology has a wide application prospect in the field of aviation and navigation and can provide a variety of solutions for the development and progress of the industry.
Application Of 3D Scanning Technology In Shipbuilding Industry
1. Part accuracy test
Regardless of the size, the hull is assembled and welded by a large number of parts. The quality of parts directly affects the safe driving and service life of the ship. The traditional detection method adopts the contact detection method, such as three-dimensional dot, special fixture and inspection tool. Although this method has high precision, it has low detection efficiency. In the detection process, it is likely to cause unnecessary secondary damage to the parts, and there are many detection dead corners.
Advanced optical measuring equipment such as three-dimensional scanner adopts optical principle for surveying and mapping, and provides reliable and real three-dimensional data on the premise of no wear and damage to the scanned workpiece. The obtained three-dimensional data can be compared with the three-dimensional drawing to quickly and accurately obtain the deviation of each position of the workpiece, and the correction scheme is given based on the comparison results. The data that are difficult to obtain by traditional methods, such as few scanning dead angles, complex curved surfaces and the angle of turbine blades, can also be obtained easily. At the same time, fast scanning can also improve the efficiency of detection and reduce time and labor cost.
3D scanning collects part surface data with up to millions of coordinate points per second, and the best accuracy can be controlled within 0.01 mm. The size of the collected 3D point cloud model is consistent with that of the parts. The professional software can quickly analyze the full size of the parts, or compare the parts drawings to quickly generate the deviation chromatogram, so as to make the machining accuracy of the parts clear at a glance. Therefore, 3D scanning technology has great advantages over traditional detection methods in detecting the machining accuracy of parts.
2. Reverse design
3D scanning technology can also be used in the reverse design of aircraft and ship parts. The key dimensions can be obtained according to the scanned data, which can be used not only for the secondary development of products, but also for the design improvement of products, so as to achieve a big breakthrough in performance at low cost. The three-dimensional scanner can easily obtain the product shape data. The shape data obtained through analysis can be improved on the original basis, or the product drawing can be designed reversely for processing. At the same time, many old classic product designs often have many exquisite designs. These designs are unknown due to the lack of key drawings and other information due to their long history and unsaved data. The reverse modeling after three-dimensional scanning can realize the reproduction of the structure, which is of great significance for data preservation, technical innovation and so on.
3. Deformation analysis/wear analysis
Ships staying on the sea for a long time are vulnerable to the erosion of sea water and sea air. At the same time, they will inevitably be damaged in the process of use. Ships often play a vital role in many important military and civil industries. Once an accident occurs, the loss is huge. Therefore, the maintenance and repair of ship equipment parts is particularly important. The three-dimensional scanner can obtain the three-dimensional data of aircraft and ships before and after use. Through the comparison of the data before and after use, we can find the deformation degree of parts and other information, and provide a clear direction for the design of products and the improvement and strengthening of corresponding parts. At the same time, high-precision scanning can also accurately and timely find the damaged parts, so as to provide data basis for the maintenance of parts.
4. Virtual assembly
Virtual assembly plays a unique role in ship development, maintenance and operation training. The three-dimensional scanning equipment is used to scan the parts to be installed, establish the three-dimensional model and match the coordinates. The engineer assembles the three-dimensional model in the same coordinate system in the software. During the assembly process, the software provides real-time collision detection, assembly constraint processing, assembly path and sequence processing, so that the Engineer can analyze the assembly of parts, After the virtual assembly, the software system can record the relevant information of the assembly process and generate a review report for later analysis. Virtual assembly is completed in computer, which saves a lot of manpower, material resources and time cost.
5. VR browsing
VR, that is, virtual reality. In the shipbuilding industry, we “move” the real scene into the computer through three-dimensional scanning. With the VR system, we can “immerse” in any place and enter every place of the ship.
In the past, when we wanted to understand the interior of the ship, we could only use pictures, videos and other materials, and the emergence of three-dimensional scanning to make the plane data three-dimensional, from three-dimensional scanning and panoramic shooting to model creation, and then to model optimization, add sound, animation and other elements to form a complete VR environment, so that anyone can immerse in it and feel the unique environmental atmosphere of the ship.