Automation is defined as “the deployment of automated processes through technology that monitors and manages production and product shipments,” and is now an irresistible trend for manufacturers. Automation has come so much in the last decade that there’s no industry that hasn’t embraced it. Companies operating in the aerospace, defense, and industrial gas turbine industries are increasingly focusing on viable solutions for fast and accurate inspection of complex parts such as castings in the manufacturing process.
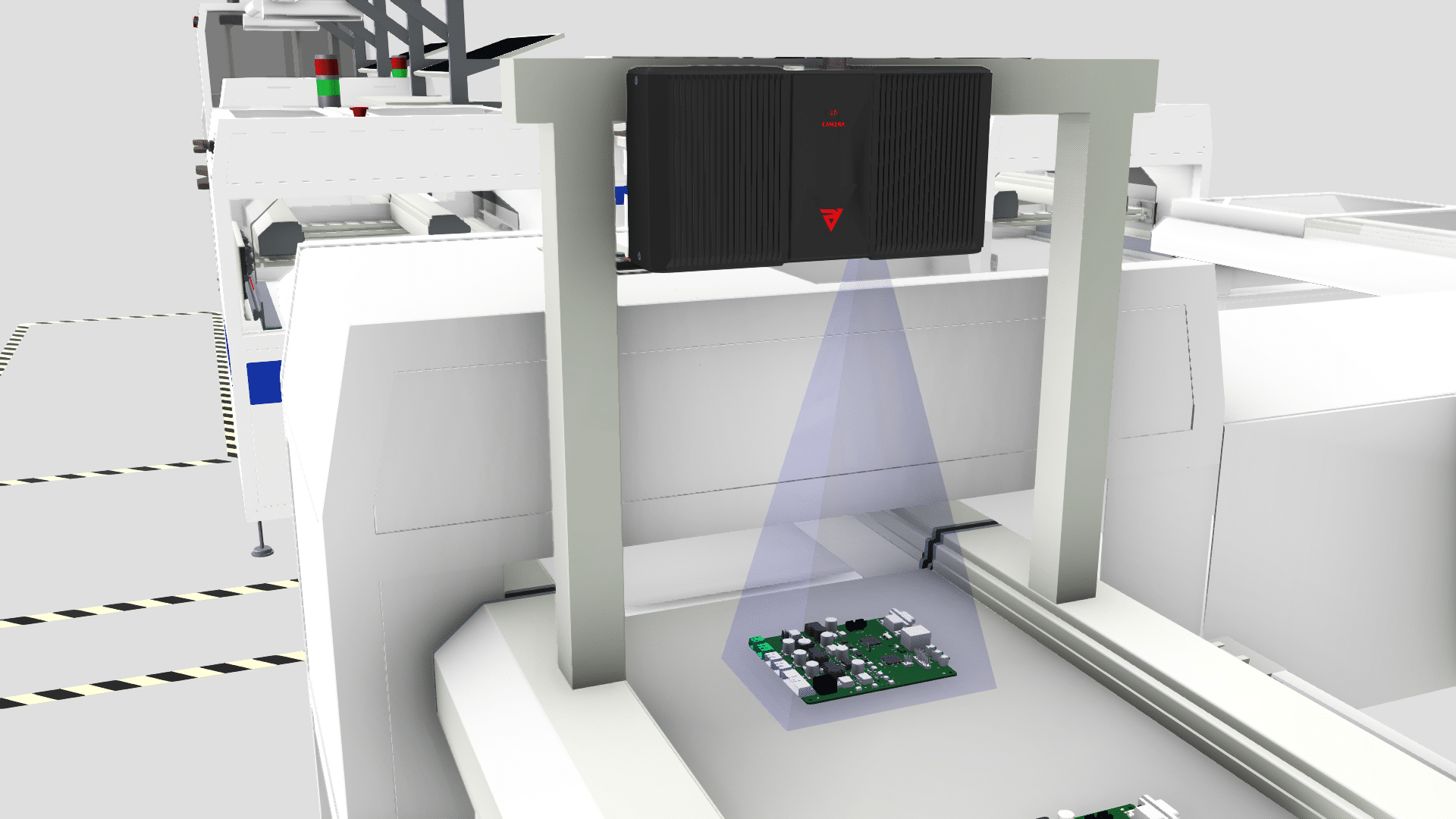
How can manufacturers identify casting incompatibilities so that they can avoid a separate process for correction while at the same time reducing customer frustration?
Optimizing manufacturing processes and producing higher quality parts requires the ability to quickly spot quality issues and take corrective action based on advanced statistical analysis. By knowing trends, companies can identify opportunities to improve upstream and downstream processes. In this way, only compatible casting parts are shipped to the customer.
As part geometries and surface treatments become increasingly complex, how can you quickly and accurately measure parts such as castings with large and complex details?
For companies looking to transition to more advanced manufacturing methods, minimizing preconditioning, measurement cycle time, and programming time is essential. Measuring instruments need to be replaced with new, state-of-the-art technologies, and to meet complex measurement standards, measurement solutions that combine accuracy and speed, versatility and simplicity are required.
As the market becomes increasingly competitive, how can manufacturers maintain a competitive advantage and exceed customer expectations?
Improving both productivity and product quality is the surest way to increase new contracts and maintain lasting customer relationships. Quality and productivity issues can be solved with automated quality control solutions designed for at-line inspection. Companies building productive industrial measuring cells designed for the production floor have built scalable and repeatable production workflows that make them the most competitive in the market.
Solution: A complete turnkey solution for automated quality control
Speed, precision, versatility, and simplicity combine automated quality management solutions to solve productivity and quality problems faced in the manufacturing process.
The speed is made possible by automated 3D scanners that leverage the capabilities of robot-mounted, metrology-grade optical 3D scanners developed for at-line inspection. In addition to faster measurement speeds, there is no need to adjust surfaces when measuring welded structural parts and castings, saving valuable measurement time.
Metrology-grade accuracy, repeatability, and resolution are due to dynamic referencing capabilities that are independent of environmental instability and provide high-quality measurement results, no matter how complex, regardless of surface treatment, trim or geometric features. This also means more reliable measurements, which in turn allows suppliers and customers to build stronger relationships.
Versatility is achieved by a complete turnkey solution designed for the production floor, where settings can be changed according to the customer’s specific needs. Highly efficient 3D scanning of objects with variable reflections can be performed and measurements of any size or surface geometry can be performed.
Simplicity is achieved by a digital twin environment that is available to users of all levels, regardless of proficiency, and enables easy and fast programming of robot paths and optimization of the line of sight of the robot system. In addition to an easy-to-use user interface, an integrated solution is useful for most operators who have no knowledge of dimensioning or robotics.
Features: Speed, accuracy, versatility and simplicity of 3D scanning enable you to build industry-leading sand casting production processes.
Automated 3D scanning solutions integrated into the production process enable engineers to quickly and accurately measure castings (regardless of geometric complexity), as well as monitor for deviations from metrics and explain trends to customers.
- At-line inspection of mass production
Highly productive industrial measuring cells pave the way for automated total inspections. Today, casting scanning is integrated into the manufacturing process. In fact, castings can be inspected in between several steps and operations during the production phase before being sent to the loading dock.
- Preventive Examinations
By measuring castings with an automated 3D scanning system, companies can obtain a lot of dimensional data. This allows engineers to monitor deviations and keep a close eye on trends. If a part has a high number of out-of-tolerance events, the engineer reviews the data to report on deviation trends and indicate corrective action.
- Quality inspection at production sites
Acquiring all surface data for parts with complex geometries or castings of different sizes is no longer a hassle. Robot-mounted scanners with optical trackers with dynamic referencing are ideal for measuring parts on the production floor because they are independent of environmental instability such as vibration and temperature fluctuations, and can consistently maintain part alignment and measurement accuracy throughout the inspection process.