In recent years, the need for precision machining has increased. With the increasing demand for EV components and the advancement of semiconductor processes due to the spread of AI and 5G, cutting sites are facing issues not only with how to “grind” accurately, but also how to “measure” accurately and efficiently.
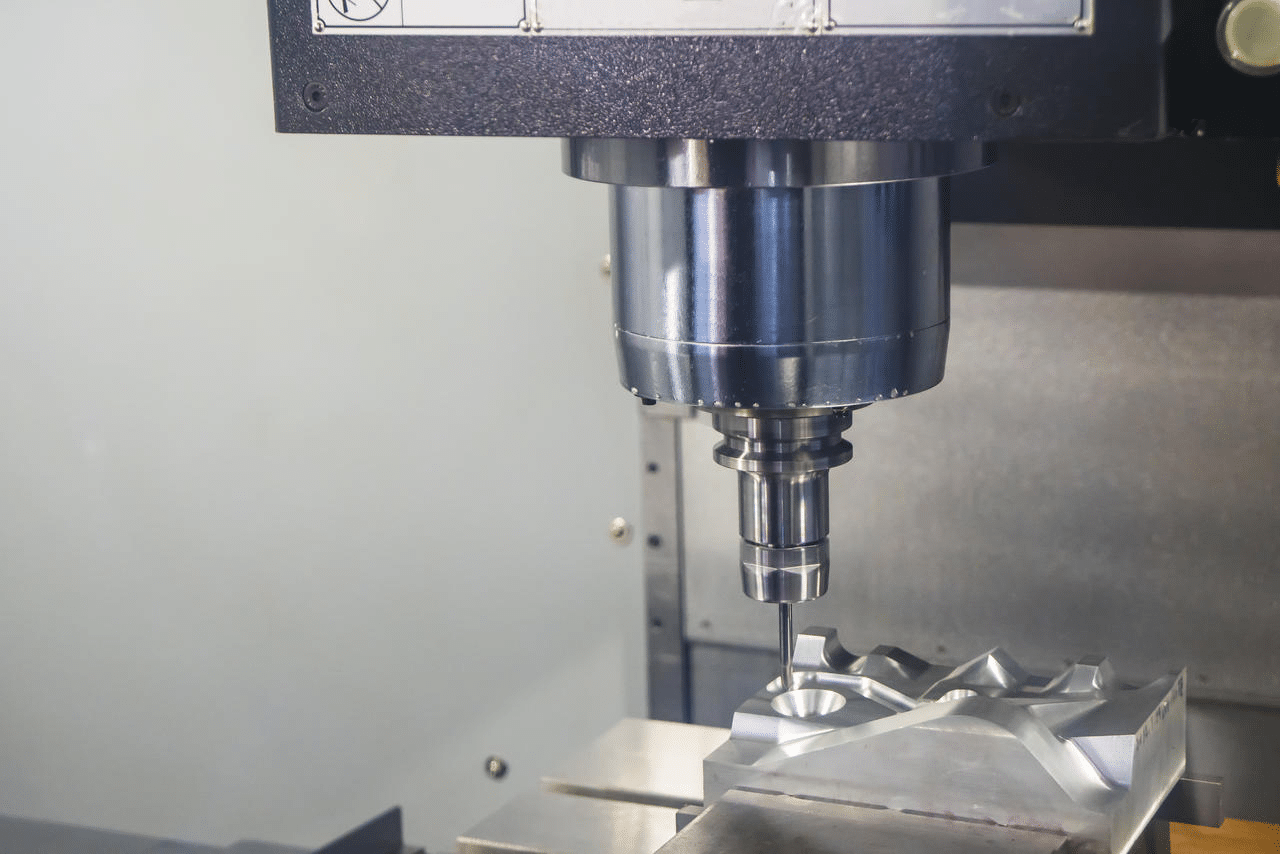
In this article, we talk about the dimensional measurement issues in CNC cutting and the handy probe 3D measuring machine that can perform 3D Dimensional Inspection for anyone, anywhere.
CNC Machining Trends and Measurement Needs
CNC machine tools that realize micron orders. At the cutting site, there are still many uncertain factors such as increasing complexity of workpieces, diversification of materials, and tool wear, and highly accurate measurement technology is indispensable for improving quality.
In cutting, measurements are performed at each process before machining (setup), during machining (process), and after machining (Dimensional Inspection), but the needs required for measurement are also changing due to changes in machining trends.
Machining Accuracy: Measure Complex Workpieces With High Accuracy
In the processing of parts for automobiles and semiconductor manufacturing equipment, the number of complex shapes and unprecedented high-performance materials is increasing, and the precision required for cutting is also increasing. As machine tools become more complex, it is no longer possible to accurately measure workpieces with complex shapes using the same “measurement method” as before. In addition, multi-edged composite tools are sometimes used to improve machining efficiency, and the measurement method has become more sophisticated.
High-Mix Low-Volume Production: Efficient Measurement Of High-Mix Low-Volume Parts
As product lifecycles in markets such as automobiles and smartphones become shorter, there is an urgent need to shift from “mass production” to “high-mix low-volume production.”
In cutting, not only the construction of flexible lines that combine robots, but also a flexible measurement system that can measure anywhere in the factory is required.
Labor Shortage: Measure Without Relying On Skilled Workers
Due to a serious labor shortage due to the declining birthrate, labor saving in factories is progressing rapidly. In cutting, the consolidation of processes using multi-tasking machines and automatic conveying by robots are increasing, but the “measurement process” is a bottleneck.
Measurements and inspections in the process are performed using micrometers and coordinate measuring machines, but standardization is still difficult and the process often relies on skilled workers. In the field, there is a need for tools that anyone can easily measure.
Challenges Of Measuring CNC Cutting Parts
As “processing accuracy,” “high-mix low volume,” and “labor shortage” become trends, it is important to understand the issues in the field in order to meet diversifying measurement needs. We will introduce the increasing issues of workpiece measurement in recent years, along with processing examples by industry.
Processing trends and measurement needs
- Motor Case (Automotive Industry)
- Cylinder block (Automotive industry)
- Artificial joints (Medical industry)
- Jet Engine Parts (Aircraft Industry)
- Large vacuum chamber (Semiconductor industry)
- Processing of motor cases(Automotive industry)
CNC Cutting of motor cases (automotive industry)
Automobiles are rapidly shifting to EVs in order to achieve carbon neutrality. The motor case that houses the EV motor is made of light aluminum alloy to reduce the weight of the car body. must be measured. Because of the high-mix low-volume production, we do not build a dedicated line like the one seen in conventional automotive parts processing.
What are the problems in motor case measurement?
Coordinate measuring machines are mainly used for precision measurement of motor cases. After processing in the machining center, we move to the measurement room and measure the dimensions, but if it is NG, we will have to go back and forth for additional work. Since the setup is redone every time the machine is moved, the machining accuracy will decrease due to positional deviation.
CNC Cutting of cylinder blocks (automotive industry)
While production for EVs is increasing, production of engines for transportation and construction machinery is still continuing. For cylinder blocks that require particularly high accuracy, “comparative measurement” is carried out with a special gauge. Since there are many measurement points, careful measurement is required so that reading errors do not occur due to unreasonable posture or parallax.
What are the problems of measuring cylinder blocks?
Comparison measurement is based on the dimensions of the master work that has been temperature-adjusted, and the difference is precisely measured.Another issue is that measurement results vary when inexperienced workers perform measurements.
CNC Cutting of artificial joints (medical industry)
Artificial joints used in artificial joint replacement surgery and artificial bones used in implants often use titanium, which is highly biocompatible. Lightweight, high-strength titanium is known as a “difficult-to-cut material” and has low thermal conductivity and severe tool wear, so measurement after machining is essential. In order to improve adhesion to the bone, it is necessary to precisely measure the hole position and geometric tolerances.
What are the problems in measuring artificial joints?
Joint prostheses are custom made for each patient. Measurements are performed with a 3D measuring machine, but since it is made-to-order, the problem is that setup and calibration take time.
CNC Cutting of jet engine parts (aircraft industry)
Jet engine parts used in aircraft use heat-resistant alloys such as nickel alloys and titanium. In order to machine the material with high precision, it is processed by one-chucking using a 5-axis machining center, but in recent years, thinner walls have been progressing to reduce weight, and further precision is required.
What are the problems for measuring jet engine parts?
Aircraft parts, which require high precision, are generally inspected for quality using a three-dimensional measuring machine. Measuring workpieces cut by 5-axis machining requires skilled skills, and because the number of operators who can operate it is limited, waiting time for measurement occurs.
CNC Cutting of Vacuum chamber (semiconductor industry)
The growing global need for semiconductors is driving the demand for semiconductor manufacturing equipment. Large vacuum chambers are equipment used in front-end processes such as sputtering and vapor deposition, but high machining accuracy is required to prevent leakage (vacuum leakage).
What are the problems of measuring vacuum chambers?
Some vacuum chambers are large, exceeding one meter. Large micrometers are used for measurements during processing, but since hole positions and geometric tolerances cannot be measured, large three-dimensional measuring machines are used for post-processing inspections. A crane was used to move the equipment to the measurement room, which required a large amount of work and reduced productivity.
The Key To Solving Measurement Challenges Is To Improve Accuracy And Efficiency
For calipers, micrometers, and coordinate measuring machines used in cutting, “improving accuracy” and “efficiency” are the keys to solving problems.
Calipers, micrometers, various gauges
It is the simplest measuring instrument most used in the field. Although it is a hand tool that can be easily measured, the measurement results may vary depending on the skill of the operator, and it is not possible to measure complex shapes, hole positions, and geometric tolerances. In the measurement of aluminum alloys, which has been increasing in recent years, there were times when the workpiece was damaged in an unreasonable posture.
The problem is to improve accuracy
- × Measurement varies depending on the operator
- × Inability to measure complex shapes and geometric tolerances
- × Measurement takes a long time
3D measuring machine
The coordinate measuring machine is a precision measuring machine used for quality inspection of workpieces. In a contact coordinate measuring machine, the stylus is brought into contact with the workpiece and the workpiece is measured based on three-dimensional (X, Y, Z) coordinates. Hole position and geometric tolerances that cannot be measured with hand tools and complex measurements can be made, but measurement in a measurement room controlled at 20°C is essential so that it is not affected by temperature.
The problem is efficiency
- × It takes a long time to move to the measurement room
- × Waiting in line for measurement
- The number of workers who can operate × is limited
Handy Probe CMMs Combining The Convenience Of Vernier Calipers With The Versatility Of A CMM
As improving measurement accuracy and efficiency become an issue, the handheld probe CMM, which combines the ease of hand tools and the versatility of 3D measuring machines, is being introduced one after another at cutting sites. The Handy Probe CMMs enable 3D measurement simply by placing your own probe against the workpiece. It is a new concept 3D measuring machine that does not require skill, and anyone can perform precise measurement anywhere.
Since it can be taken out and used immediately like a caliper, there is no need to “move to the measurement room” or “wait in line for measurement” that were required for a coordinate measuring machine, greatly expanding the range of measurements.
In addition, the Handy Probe CMMs do not have the same measurement orientation restrictions as conventional coordinate measuring machines and touch probes used for on-board measurement. It is a free-angle probe that can be handled freely, and can be measured with a caliper feeling.
Comparison with calipers, micrometers, and various gauges
- There is no variation in measurement by operator
- Complex shapes and geometric tolerances can be measured
- Measurement time can be shortened
Comparison with coordinate measuring machines
- No need to travel to the measurement room
- No waiting for measurement
- Anyone can operate