Coordinate measuring machine (CMM) is a precision measuring instrument, can be all workpiece sizes and geometric position dimensions, surface measurements, by many scientific research institutes, industrial and mining enterprises to use. Using the coordinate measuring machine for part shape and position tolerance detection, both engaged in numerical control technology and several points of integration research, the measurement results are very accurate. However, in actual measurement work, due to improper measurement steps, relatively large measurement errors may occur.
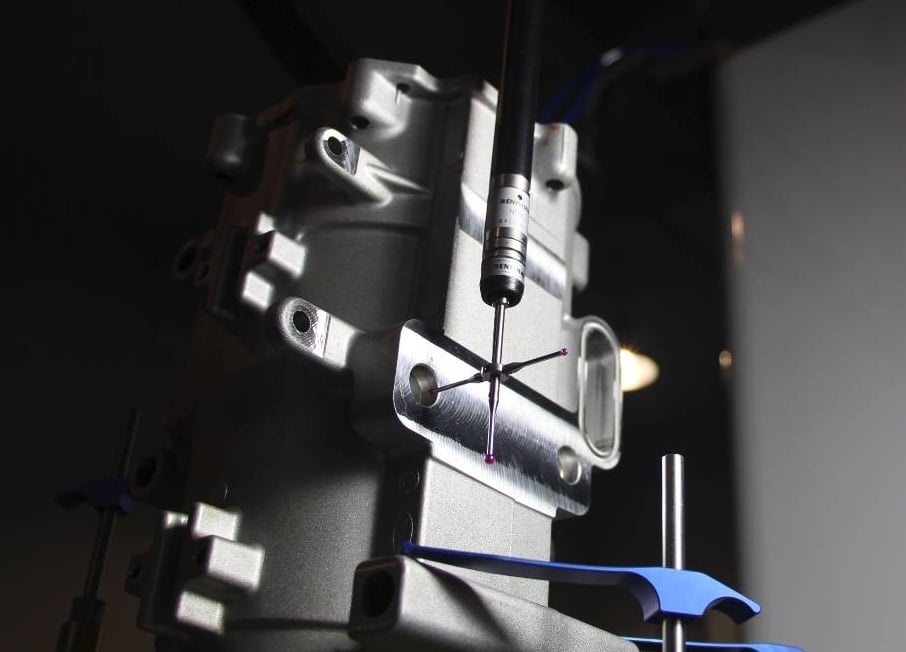
Due to the complexity of the measurement process, how to measure the workpiece with coordinate measuring machine is not easy to master, the following is a simple introduction to how to measure the workpiece with CMM:
1. Analyze measurement requirements
When a new workpiece is sent to coordinate measuring machines for dimensional inspection, we must first understand the measurement requirements of the tester. According to the accuracy of our coordinate measuring machines such as 1.6 + 3.0L/1000 um, the measurement requirements are analyzed to see whether the coordinate accuracy meets the measurement requirements, and which one or more of the geometric tolerances should be measured by the workpiece. Because the measurement requirements determine our measurement methods and measurement processes. At this time, it is also necessary to process the workpiece or the finished product drawing as the basis for measurement. At the same time, it is necessary to understand the machining process of the workpiece and understand the workpiece processing benchmark (this is a must, because some workpieces are not processed according to the design benchmark or process benchmark on the drawing when processing, and the specific situation is analyzed in the next step).
2. Determine the measurement scheme
The process is to determine the measurement scheme, measurement method and measurement benchmark according to the measurement requirements. The establishment of the measurement scheme and measurement method is determined by the analysis of the measurement requirements of the previous step and is determined empirically. The choice of measurement benchmark has a great influence on the accuracy of the measurement results. The processing benchmark of processing is inconsistent with the process design benchmark, and is divided into two types according to the actual situation, one is the inspection of processing capacity or processing process. The second is the inspection of finished products. In the first case, the workpiece is generally measured by the processing reference as the measuring reference; In the second case, the workpiece is generally measured using a process design benchmark. Of course, the choice of measurement schemes, measurement methods and measurement benchmarks involves many empirical aspects.
1) Read the drawings and be familiar with the co-construction
2) Clear measurement size
3) Confirm the measurement sequence
3. Reasonable choice of probe configuration
According to the elements to be measured in the workpiece, the probe file of different configurations, the angle of the probe, the length of the probe rod, etc. are selected.
The probe is validated after definition. Principles for selecting probes:
In order to ensure a certain measurement accuracy, in the use of probes, it is necessary to:
(1) Reasonable selection of probe measuring ball diameter
Some “blank parts” and parts processed by ordinary machine tools have not been processed by grinding machines or have not processed burrs, and due to their large shape errors and burrs, they can also cause the measurement results to be repetitive. In this case, it is recommended to use a large diameter stylus and collect more sample points on the features to obtain a more average effect and obtain good repeatability.
(2) Reasonable choice of probe length
The length and weight of the stylus or extension rod have a great impact on the accuracy and repeatability of the measurement. The load capacity of the probe and the sensitivity of the probe (that is, the accuracy of the probe) are often a pair of contradictions, and their ability and price are generally proportional to each other. The extension bar and stylus that exceed the load of the probe will cause disturbance errors in the measurement results and shorten the service life of the probe. Therefore, when using a measuring needle with an extended length, it is necessary to select a suction cup or probe with a correspondingly larger force measurement.
(3) Probe calibration
The correctness of the probe correction is the guarantee of the measurement accuracy, especially the correction of the multi-probe position and the star probe, which must be checked to ensure the accuracy of the measurement.
When using a standard ball calibration probe, for the case of relatively high measurement accuracy, it is necessary to appropriately increase the number of check points in each layer; For the case of measuring complex surface curve features, the number of layers for calibration needs to be appropriately increased.
4. Part Clamping
Clamping principles for parts The clamping of parts needs to consider:
- Stability
- Repeatability
- Convenience, need to consider the probe factor, the distribution of measurement characteristics, etc
- Consider the deformation effect of the part (mainly for thin-walled parts)
For clips there are the following requirements:
- First, the fixture should have sufficient precision and stiffness;
- Second, the fixture should have a reliable positioning reference;
- The third is to have a clamping device.
The main considerations for the clamping of box parts are:
- The convenience of measurement, mainly considering the angle of the stylus;
- The repeatability of the measurement, easy to repeat the measurement of the program;
- The stability of the parts The above is the clamping principle of the parts, on the basis of this principle, according to the actual situation of the workpiece clamping.
Larger workpieces According to the principle of convenient measurement, we can use a higher precision horn with a jack to clamp. Smaller workpieces or irregular workpieces can not be satisfied with only horns and jacks in the clamping process, which requires universal fixtures or special fixtures to ensure. It should be noted here that the measurement platform using air flotation support should pay special attention to the stability of the parts when clamping, so as to avoid the displacement of the workpiece due to the shaking of the platform, which in turn leads to inaccurate measurement results.
5. Preparation of measurement procedures
The process for preparing the procedure is as follows:
- In order to facilitate management, a new measurement program file name with the name of the workpiece or the name of the process is newly established.
- Manually establish a rough coordinate system (3-2-1 method), first collect at least 3 points on the datum plane, and find the plane as the first axis of the coordinate system in the coordinate system; 1 more line (or 2 circles); Finally measure a point (or a circle). Use these manually collected elements to create a rough coordinate system. The shortcut key to establish a coordinate system is CtrltAlt+A.
- Lift the probe from the last manual element, click the DCC mode button in PCDMIS, and enter the program automatic mode. And add a moving point (or set the safety plane to move the probe to the safety plane).
- On the datum surface of the established coordinate system, as many mining points as possible (or according to the process requirements, only the corresponding position of the positioning block of the part is collected as the datum surface), click the Done key on the operation handle after the mining point. Select the execution block in the PC-DMIS software to re-automate the manually acquired datum by the measuring machine.
- Find the plane that has been automatically run by the machine as the first axis of the refined coordinate system.
- Automatically measure other reference elements that constitute the refined coordinate system, and establish the refined coordinate system after completion.
- Measure the various elements required for analysis. In this process, automatic measurement is used as much as possible to reduce the error caused by manual measurement. During this process, be sure to add moving points or move to the safety plane to ensure that there is no collision of the probe.
- Construct elements that cannot be measured directly.
- Evaluate the measured elements according to the measurement requirements of the workpiece drawings.
- In the process of compiling the measurement program, attention should be paid to saving the program to avoid the loss of the unsaved part caused by the accidental shutdown of the measurement software.
6. Run the program
Execute the completed program from beginning to end to determine whether the program can be fully executed.
And improve the needle running path and moving points and other deficiencies.
7. Output report
The first output report is first submitted to the tester for viewing, and the program is saved for next operation after the modification is confirmed. When reporting output, we generally report the file name the same as the workpiece name or process name, and send all the measurement results to the same folder for easy management.