In the realm of precision engineering, where accuracy reigns supreme, the role of CNC measuring systems is indispensable. These marvels of technology have revolutionized the way we assess and validate the dimensions, tolerances, and quality of intricate components with astonishing precision. From manufacturing industries to research laboratories, CNC measuring systems have become the gold standard for ensuring excellence and consistency in the modern era of advanced engineering. In this article, we will embark on an illuminating journey into the realm of CNC measuring systems, delving into their fascinating capabilities, applications, and the unrivaled potential they hold in shaping the future of precision engineering. Prepare to be captivated as we unlock the hidden secrets of this extraordinary technology, revealing a world where accuracy knows no bounds.
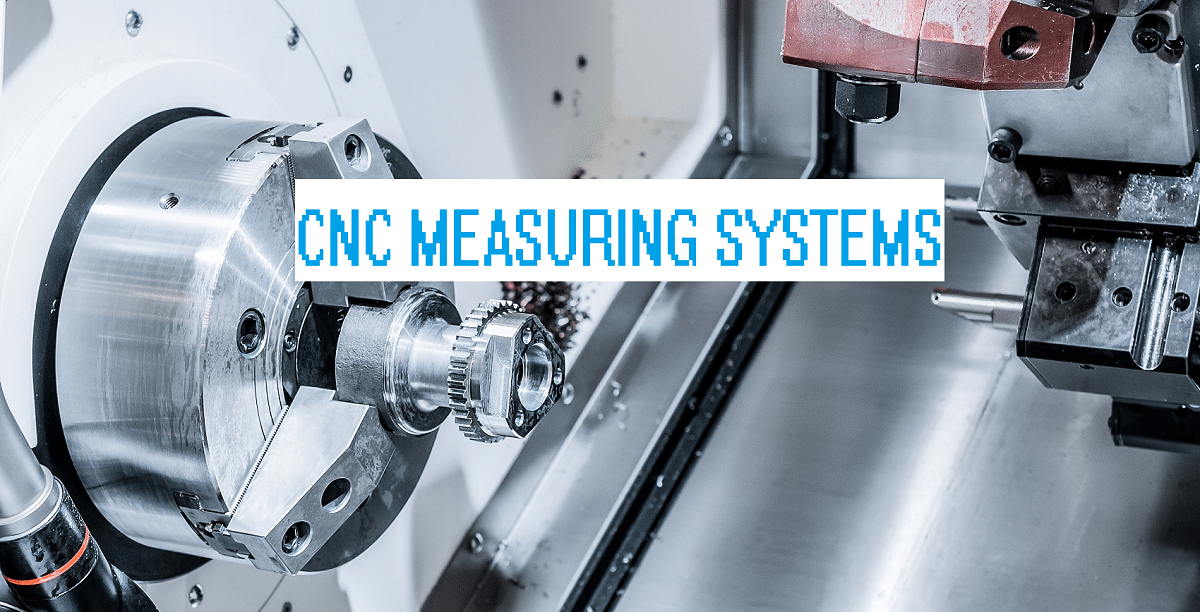
CNC Measuring Systems
CNC (Computer Numerical Control) measuring systems refer to the use of computer-controlled devices to measure and inspect machined parts in a manufacturing environment. These systems provide accurate and precise measurements of various dimensions, ensuring that the manufactured parts meet the required specifications.
Here are a few common types of CNC measuring systems:
- 1. Coordinate Measuring Machines (CMMs): CMMs are widely used in industries for dimensional inspection of complex parts. They use a probe to measure the coordinates of points on the surface of the part. The collected data is then used to create a digital representation of the part, which can be compared against the original design to check for any deviations.
- 2. Vision Systems: Vision systems utilize cameras and image processing techniques to inspect parts visually. They capture images of the part and analyze them to detect defects, measure dimensions, and perform various quality checks. Vision systems are often used for surface inspection and to verify the presence or absence of specific features.
- 3. Laser Scanners: Laser scanners use laser beams to capture the shape and geometry of a part. The laser beam is directed onto the part’s surface, and the reflected beam is analyzed to generate a three-dimensional representation of the part. Laser scanners are commonly used for reverse engineering, quality control, and dimensional inspection of freeform or complex surfaces.
- 4. Optical Comparators: Optical comparators use optical magnification to measure dimensions and compare them to a reference. The part is placed on a stage, and an optical system magnifies the image of the part onto a screen. A reticle or overlay with known dimensions is superimposed on the image to make measurements. Optical comparators are useful for quick and non-contact measurements of simple geometries.
- 5. Form Measurement Systems: Form measurement systems are specifically designed to measure the form, profile, and surface characteristics of a part. These systems use various probes, sensors, or scanning methods to measure parameters such as roundness, flatness, cylindricity, and roughness. They are commonly used in industries where the surface finish and shape of a part are critical, such as automotive and aerospace.
CNC Measuring Tools
CNC measuring tools form the backbone of accurate measurement in the CNC machining process. These tools are specifically designed to measure various aspects of the manufactured components, ensuring conformity to precise specifications. Here are some essential CNC measuring tools:
- Calipers: Digital or Vernier calipers provide precise measurements of length, width, and thickness. They are ideal for measuring external dimensions of machined parts.
- Micrometers: Micrometers are precision tools used for measuring dimensions with high accuracy, typically in the range of micrometers or millimeters. They are ideal for measuring smaller features like diameters, depths, and clearances.
- Height Gauges: Height gauges allow for the measurement of heights, steps, and depths accurately. They are commonly used in the inspection of machined components.
- Thread Gauges: Thread gauges, such as plug gauges and ring gauges, are utilized for measuring the pitch and diameter of threaded components. These tools ensure proper thread engagement and quality control.
CNC Measuring Equipment and Devices
CNC measuring equipment and devices encompass a broader range of tools and systems that enable comprehensive dimensional analysis and quality control during the manufacturing process. These devices go beyond individual measurements and offer advanced features for enhanced accuracy and efficiency. Here are a few notable examples:
- Coordinate Measuring Machines (CMM): CMMs are versatile devices that measure the coordinates of points on a workpiece’s surface, allowing for precise three-dimensional measurements. They utilize a probe attached to a moving arm or bridge, capturing data points and generating detailed measurement reports.
- Optical Measuring Systems: Optical measuring systems use light-based technology to capture dimensional data. These systems can employ various techniques such as structured light, laser scanning, or vision-based measurements. They offer fast and non-contact measurement capabilities for complex geometries.
- 3D Scanners: 3D scanners capture the complete shape and geometry of an object by creating a digital representation known as a point cloud. These scanners are particularly useful for reverse engineering, quality control, and creating digital models for further analysis.
- Vision Systems: Vision systems integrate cameras, image processing algorithms, and software to measure dimensions and inspect parts. They can detect defects, measure dimensions, and perform complex inspections based on predefined criteria.
CNC Dimensional Measurement Tools
In addition to individual measuring tools and advanced measuring equipment, CNC dimensional measurement tools enhance the precision and efficiency of CNC machining operations. These tools work in tandem with CNC machines, enabling real-time feedback and adjustments. Some examples include:
- Tool Presetters: Tool presetters measure the dimensions of cutting tools, such as drills and end mills, before they are loaded into CNC machines. This process ensures precise tool positioning and reduces setup time.
- In-Process Measurement Probes: In-process measurement probes are mounted on CNC machines and provide real-time feedback during the machining process. These probes can measure dimensions, check for tool wear, and perform automatic compensation to maintain accuracy.
- Laser Interferometers: Laser interferometers are used to measure and calibrate the positioning accuracy of CNC machine axes. These tools help maintain machine precision by detecting any deviations or errors.
These CNC measuring systems are integrated with computer software that allows for data analysis, statistical process control, and automatic feedback to the machining process. The combination of CNC machines and measuring systems enables efficient and accurate quality control, reducing errors and ensuring that manufactured parts meet the required specifications.
CNC measuring systems are indispensable in the modern manufacturing landscape, ensuring precision, quality control, and efficiency throughout the CNC machining process. CNC measuring tools, measuring equipment and devices, and dimensional measurement tools all contribute to the success of CNC manufacturing operations. As technology continues to evolve, the integration of advanced measuring systems with CNC machinery will further enhance productivity and quality in the manufacturing industry, leading to the production of more accurate and reliable components.