We often use many quality indicators. Many people have encountered this problem about how to calculate these indicators. Today, we have prepared some commonly used formulas for quality management, which you must use.
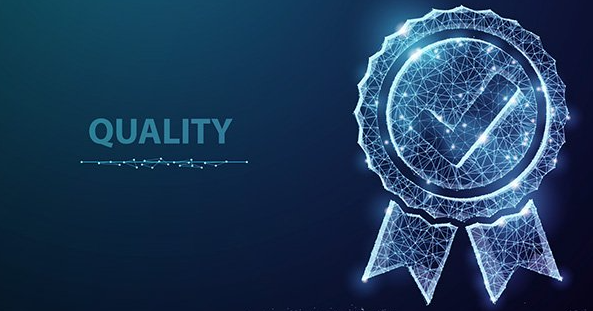
Common Formulas For Quality Management
1. Scrap rate
– Definition: This percentage is obtained by dividing the cost of waste materials by the total production cost or by dividing the total quantity of waste products by the total production quantity of products.
– Purpose: Used as a result measure to determine whether the process is in accordance with the standardized production and assembly of parts.
– Formula: Scrap rate% = (material amount of scrap / total production cost) × 100% or (total scrap quantity / total production quantity of products) × 100%。
– Terminology: Scrap material amount: the value of the material used for scrap.
– Total production cost: he sum of labor, materials and factory burden (water, electricity, etc.).
– Application/information: Scrap calculation is to get its value directly from the financial system of the company. If the company’s financial system cannot separate the value of waste materials from labor and expenses, it shall coordinate with relevant departments as soon as possible.
1. Rework rate
– Definition: The proportion of time spent in rework activities is obtained by dividing rework man hours by production man hours or the total quantity of reworked (repaired) products by the total production quantity.
– Purpose: Used as a result measure to emphasize those operation stations that need to be improved in the first quality.
– Formula: Rework rate% = (rework man hours / total production man hours) × 100% or (total quantity of reworked (repaired) products / total production quantity) × 100%.
Terminology:
- Rework hours: It refers to the time spent on reprocessing, sorting and repairing the workpieces that will become waste. These time can be spent on work in progress, finished products and purchased parts or materials. Rework time includes repair, repackaging, re sorting, additional inspection activities and containment. Rework time includes internal or external activities. It shall include direct time plus the direct time part of overtime.
- Production labor hours: Total working hours of direct / production workers (including direct time plus direct time part of overtime).
- Application information: Occasional inspections by direct labor workers shall not be considered rework. Any product that re enters the production process shall be considered as rework. Part of the total labor content of the production line shall be considered as rework. This part will be determined according to the reworked products. For example, in the final inspection, 10% of the products of the painting production line are unqualified, and there are 20 operators in the painting production line. The reworked products (10%) need to be painted again, and 10% of the total working time of the painting production line is considered to be used for rework. 10% × 20 people × 8 hours = 16 rework hours.
3. Qualified rate of product warehousing inspection
– Definition: Obtained by dividing the qualified quantity of product receipt inspection by the total quantity of receipt inspection.
– Purpose: used as process measurement to measure the quality level of the whole production process.
– Formula: Qualified rate of product warehousing inspection% = (qualified quantity of product warehousing inspection / total quantity of warehousing inspection) × 100%.
4. Parts per million of nonconforming products (customer return rate or product defect rate)
– Definition: The ratio of the quantity returned / rejected by customers or the quantity of unqualified products to the total shipped quantity or the total production quantity per million products.
– Purpose: It is used as a result measure to comprehensively show the impact caused by product dissatisfaction, so as to concentrate on solving the problem.
– Formula: Customer return rate = returned pieces / delivered pieces, total product quantity * 1000000 or product defect rate = total unqualified pieces / total product quantity * 1000000.
5. Quality accident
– Definition: The number of production pauses caused by unqualified products every year. Cause the company to stop delivery, stop production or require the manufactured products to be corrected.
– Purpose: It is used as an overall outcome measure to reflect the dissatisfaction of products caused by the number of quality accidents of the company, so as to concentrate on solving problems.
– Formula: Quality accident = the number of factory production pauses caused by quality accidents defined by the company every year.
6. Processing defect rate of parts (inspection qualification rate or process qualification rate)
– Definition: Patrol inspection qualification rate or process qualification rate, that is, the one-time qualified quantity in the production process of parts divided by the total production quantity of parts or the weighted average. The processing defect rate of parts is the total number of unqualified parts divided by the production input quantity of parts.
– Purpose: Used as process measurement to determine the quality level of production process.
– Formula: (Inspection qualification rate or process qualification rate)% = (one-time qualified quantity of process / total production quantity of parts) × 100% part processing defect rate = (unqualified quantity of parts / production input quantity of parts) × 1,000,000.
7. One time pass rate of customer inspection
– Definition: Refers to the delivered products. The quantity received after passing the customer’s inspection at one time is divided by the total quantity of delivered products.
– Objective: To measure the quality level of finished products delivered from the warehouse as a result measure.
– Formula: One-time pass rate of customer inspection% = (quantity received after passing customer inspection at one time / total quantity of delivered products) × 100%.
8. Incoming inspection qualification rate
– Definition: Within a certain period of time, the qualified quantity of incoming inspection is divided by the quantity of incoming inspection.
– Purpose: Used as a result measure to monitor the supplier’s supply quality level.
– Formula: Qualified rate of incoming inspection% = (qualified quantity of incoming inspection / total quantity of incoming inspection) × 100%。
9. Quality cost
– Definition: It is simply defined as the failure (loss) cost within a certain period of time.
– Purpose: It is used as a result measure to reflect the comprehensive achievement of the operation effectiveness of the company’s quality management system.
– Formula: Quality cost = internal failure (loss) cost + external failure (loss) cost. Internal failure (loss) cost = scrap loss cost + rework or repair loss cost. External failure (loss) cost = customer return loss fee + product liability fee + complaint fee. Ratio of quality cost to sales = (quality cost ÷ sales) × 100%.
Terminology:
- Internal failure (loss) cost: The loss caused by the failure of the product to meet the quality requirements before delivery.
- External failure (loss) cost: Losses caused by the product’s failure to meet the quality requirements after delivery.
- Scrap loss fee: The cost of scrapping caused by the failure of finished products, semi-finished products and products in process to meet the quality requirements and can not be repaired or economically unworthy of repair.
- Rework or repair loss cost: Expenses paid for repairing nonconforming products to meet the quality requirements or expected use requirements.
- Customer return loss fee: Loss of customer return expenses.
- Product liability fee: Relevant compensation costs caused by product quality failure.
- Complaint fee: Expenses incurred for repairing or replacing products with quality problems complained by customers.
10. Batch failure rate
– Definition: Refers to the proportion of the number of batches that need to be reworked (repaired or scrapped) in the total number of inspection batches in a certain period of time if the inspection batch is judged to be unqualified.
– Purpose: Used as a result measure to monitor the overall quality level of the process.
– Formula: Batch failure rate = number of unqualified batches / total number of inspection batches * 100%.
– Inspection lot: A batch of products submitted for inspection, and also a batch of products collected as inspection objects.
Generally, the inspection lot shall be composed of unit products with the same model, grade and type (size, characteristics, composition, etc.) and basically the same production conditions and production time. Production batch: refers to a certain number of products put into production determined by the production plan.