Many people may know that APQP is one of the five tools of quality management. So what are the stages of APQP? Advanced Product Quality Planning includes five phases: planning and defining the project, product design and development, process design and development, product and process confirmation, and feedback evaluation and corrective measures.
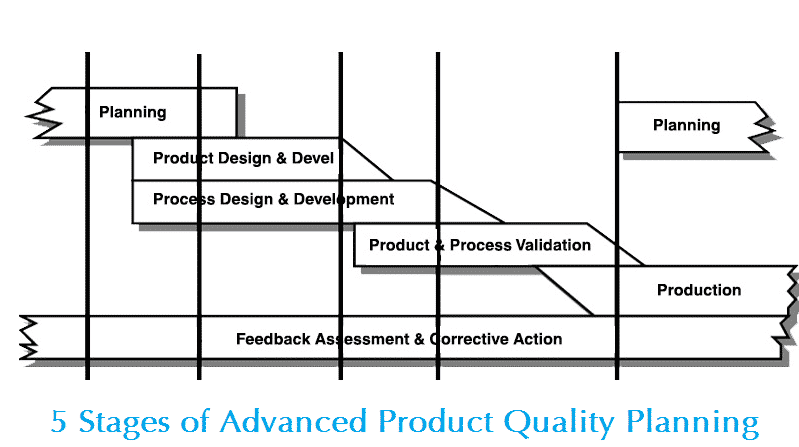
5 Stages of Advanced Product Quality Planning (APQP)
APQP adopts a structured description method to manage the project through the definition of two dimensions: time and task. In practical application, the company can define the number of nodes of product development and the form of deliverables according to the characteristics of its own products. Quality control involves a wide variety of quality inspection services and management methods.
Phase I: product planning and definition
This stage is mainly to determine the scope and feasibility review stage, mainly including:
(1) Provide customers with necessary documents and requirements related to products;
(2) Understand customer needs and expectations;
(3) Identify potential constraints and risks to meet customer requirements;
(4) Identify sub-suppliers and processes to meet requirements;
(5) Determine the feasibility of product manufacturing scheme;
(6) Collect historical data and quality information;
(7) Establish design objectives;
(8) Establish an APQP cross-departmental team to determine the submission level of PPAP.
Phase II: product design and development
This stage is a further in-depth review of engineering and technical requirements to ensure that the products meet the needs and expectations of customers, mainly including:
(1) Ensure the feasibility of product manufacturing through the review of design objectives, drawings, technical agreements, calculation and simulation data;
(2) Use DFMEA tools to identify potential problems and risks of products and get opportunities for improvement;
(3) Identify special characteristics and form a list of special characteristics;
(4) Prepare test verification plan to verify product design elements;
(5) Prepare initial process flow chart and sample control plan;
(6) Prepare error-proofing measures to reduce product risks;
(7) Determine the product quality assurance plan;
(8) Design change management.
Phase III: process design and development
This stage is to meet customer expectations and product requirements, develop the manufacturing process, and use DFMEA tools to identify potential problems and risks in the manufacturing process, so as to improve the process design, mainly including:
(1) Considering the layout of the production line, form process flow chart, and workshop plan;
(2) Plan product handling route;
(3) Use DFMEA tool to identify potential problems and risks in the manufacturing process and improve process design;
(4) Prepare operation instructions, such as SOP and SIP;
(5) Form a list of equipment and measuring tools;
(6) Prepare trial production control plan;
(7) Form CPK research plan, MSA and CMK plan;
(8) Implement product packaging and transportation specifications.
Phase IV: product and process validation
This stage is to verify the product characteristics and process characteristics through the evaluation of the production trial run, and form the production part approval document (PPAP), mainly including:
(1) Determine the trial production plan;
(2) Prepare production control plan;
(3) Measurement system analysis and form GRR analysis report;
(4) Analyze the capability of key equipment and form CMK report;
(5) Analyze the initial process capability and form CPK report;
(6) Confirm the process and form trial production records and trial production inspection records;
(7) Research on working hours and form a standard working hour Research Report;
(8) Approval of production parts, formation of Appearance Approval report, full-scale inspection report, material inspection report and performance test report, and submission of parts warranty (PSW);
(9) Packaging evaluation and form packaging evaluation report;
(10) Prepare preventive maintenance plan for key equipment;
(11) Prepare mass production handover list.
Phase V: product and process approval
This stage is the customer’s verification and approval of product quality. PPAP documents are the most direct evidence to meet the customer’s quality requirements. Therefore, this stage is mainly the customer’s verification and approval of PPAP documents, mainly including:
(1) PPAP documents;
(2) Main prototype;
(3) PSW.
Benefits of Implementing Advanced Product Quality Planning (APQP)
(1) Manage the product development process with a structured and systematic method, and support the standardization and simplification of the process, so as to reduce the time to market and improve efficiency;
(2) Emphasizing the role of cross-sectoral groups;
(3) Improve the overall quality of products and customer satisfaction;
(4) From conceptual design, design development, process development, trial production to production, as well as information feedback, corrective measures, and continuous improvement activities in the whole process;
(5) Continuously take error-proofing measures to reduce product risks;
(6) Promote the early identification of quality problems, from quality control to quality assurance.
Tips for Implementing APQP (Advanced Product Quality Planning)
- Play the role of the cross-departmental team. APQP documents are the result of the cross-departmental team discussion and are not prepared by a person or a department;
- Use FMEA tools to emphasize the identification of potential risks and find improvement opportunities;
- Fully identify the special characteristics of products and processes, which need to be reflected in the flow chart, FMEA, control plan (CP), operation instruction (SIP SOP), design and engineering drawings;
- Focus on the design method of error proofing;
- Use MSA and CPK analysis tools to ensure the stability of the measurement system and production process, reduce variation and ensure product quality consistency.