Quality management should be changed from post quality inspection control to preventive pre and in-process control, what’s why we have the initial production check and during production inspection. Full quality management can reduce nonconforming products and ensure good quality. So what is the nonconforming product and how to control it?
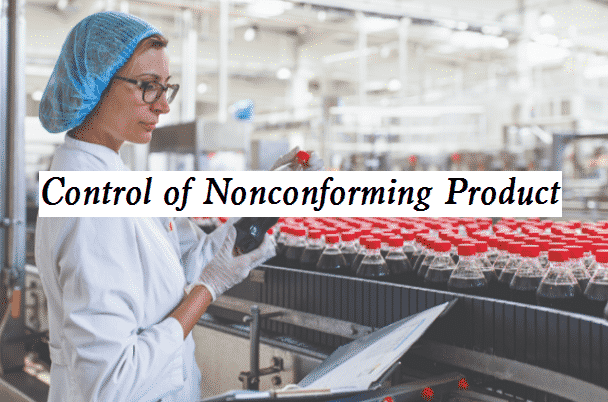
What are Nonconforming Products?
Nonconforming products refer to products that exceed the accepted standard and do not meet the requirements. Nonconforming products need to be identified, separated, assessed, and reprocessed to prevent unexpected use or flow into the hands of customers. In order to respond, handle, prevent and eliminate the causes of quality abnormalities in time, so as to maintain the normal operation of the quality system.
How Do You Control Nonconforming Products – Control of Nonconforming Product Procedure
1. Control of material quality
The quality department is responsible for designing the sampling inspection scheme and implementing the inspection according to the standards. If the incoming quality is found to be unqualified, the unqualified label shall be posted, the batch return shall be carried out according to the process, and the abnormality should be fed back to the purchasing department for communication and handling.
- Reject: in case of a return, the procurement department shall contact the supplier and return the nonconforming products to the supplier; in case of urgent material demand, the production planning or procurement leader shall invite relevant departments to convene the raw material review committee to discuss the emergency handling methods.
- Supplier selection: the procurement department shall contact the supplier to conduct a full inspection on the nonconforming products, and select the qualified products for us; Nonconforming products shall be returned and replaced.
- Select on behalf of suppliers: if suppliers cannot come to select, the factory will arrange to select on behalf of them. However, the selected man-hour cost will be transferred to the supplier for payment.
- Rework: unqualified products that can be repaired after selection shall be reprocessed by the supplier for unqualified items to make the products meet the required specifications and quality.
- Special procurement: due to the urgent production demand, the unqualified items will not affect the product function and appearance after being put into operation, or the impact degree is within the acceptable range after review, and other conditions that can be used under concession, which can be adopted after being reviewed and countersigned by the raw material review committee, and signed by the chairman of the raw material review committee; Specially purchased products shall be marked according to the company’s regulations, and all records shall be filed according to the record management requirements. Note: if the quality is abnormal and belongs to customer-supplied materials, the quality shall be reported to the sales department to inform the customer of the abnormal situation, and the sales department shall communicate with the customer and give handling opinions; Handle according to customer feedback.
2. Product control during production
If any quality abnormality is found during the quality inspection and patrol inspection or the production operator finds any quality abnormality through independent inspection, he must immediately inform the shift leader of the production section for emergency treatment. Identify, distinguish and isolate non-conforming products and products that may be affected, and mark them clearly.
Set the inspection and detection methods for quality or process, conduct full inspection or test for abnormal isolation products, and flow into the next process after confirmation.
Timing of shutdown for emergency treatment of abnormal quality: technical documents when the production parameters are set improperly, resulting in a large number of products with poor consistency; the production defect rate is high, the emergency treatment countermeasures are invalid, and the product defect rate continues to rise; when the product does not meet the requirements due to the misuse of unexpected materials and data. The line shutdown must be decided by the manager of the process, quality, production, and relevant departments, and the abnormalities shall be eliminated after the line shutdown is confirmed In addition, the production can be resumed only after the trial is confirmed to be free of problems.
The nonconforming products in the production process shall be operated according to the established control plan and treatment process, or the rework, repair, selection, scrap, special purchase, degradation, and other operations shall be carried out after being evaluated by the process, quality, production, and other relevant departments.
3. Quality control for finished products and shipment
OQC shall carry out delivery sampling inspection for finished products. In case of abnormal quality exceeding the control requirements, the products shall not be delivered. The nonconforming products shall be handled according to the methods specified in the operating instructions for delivery inspection of each department.
In case of nonconforming quality feedback from customers, it shall be handled according to the customer complaint management process and return and exchange process of each department.
When the nonconforming level of a customer complaint, change, and reliability quality develops, the quality department shall check the quality of the inventory. If the quality of the inventory is found to be unqualified, the quality department shall notify the warehouse for marking and isolation, and the warehouse shall not ship. The quality department shall inform the production planning, and the production planning shall give the handling opinions of the outbound stock, and other units shall cooperate with the handling opinions of the production planning to handle the nonconforming products.
When nonconforming product quality is found in the factory, if the products involved in the abnormality have been shipped to the client or are on the way to the client, the quality or sales department must contact the client to return the products for re-inspection, or negotiate the handling method to ensure the quality of the products shipped to the client.
4. Nonconforming product handling procedure
The above nonconforming products defined according to the control requirements of nonconforming products shall be treated according to the operation procedure requirements or control plan of each process after being identified, distinguished, isolated and marked, or reworked, repaired, selected, scrapped, especially adopted, degraded and other operations shall be evaluated by the process, quality, production, and other relevant departments.