Compared to metal and ceramics, resin molding makes it possible to produce a large number of high-precision products at low cost. In addition, since it is cheaper and superior in mass production than processing methods such as cutting and pressing, there are many cases where parts that used aluminum etc. at the prototype stage are changed to resin at the mass production stage.
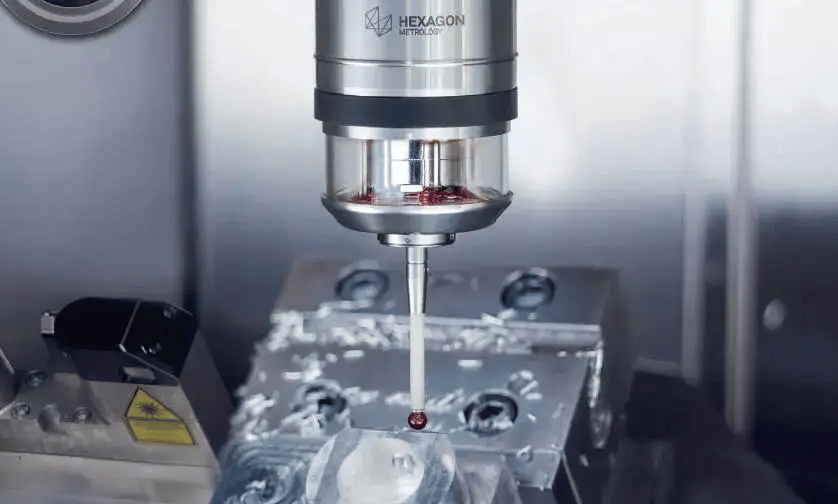
However, it also has characteristics such as injection and blow failures due to abnormalities such as viscosity, temperature, and pressure during molding, and shape defects due to mold wear. Furthermore, due to the characteristics of the resin, deformation may occur due to residual stress or thermal stress even after molding. These defects are particularly fatal for assembled and mating parts that require high accuracy, and are major problems that directly lead to product malfunctions and assembly and mating defects.
This section introduces the main resin molding methods and types of trouble, prototype measurements in development and design, and measurement methods to prevent defective outflow in mass production. In addition, we will introduce the challenges of traditional measurement methods and solutions to solve them.
What Is Resin Molding?
Resin molding is a processing method in which the resin that has been heated and melted is injected into a mold, made into a predetermined shape, cooled, solidified, and taken out. Taking advantage of the characteristics of various resin molding materials, we mold in a method suitable for the application and shape.
As molding materials, pellets in which the resin is made into rice granules are used for thermoplastic resin, which produces plasticity by heating, and powdered resin is used for thermosetting resin, which solidifies by heating. We may also use pellets or powders that mix function-enhancing additives or colorings into the resin.
In order to perform resin molding stably, it is important to manage molding conditions such as mold temperature, amount of resin material, and injection rate. In addition, in each process, attention should be paid to contamination of dirt and dust, and adhesion of foreign matter due to static electricity.
Types Of Resin Molding
Resin molding methods can be mainly classified into injection molding, blow molding, extrusion molding, and calender molding, and among them, injection molding and blow molding are widely used as representative molding methods. Here, we will explain these two molding methods.
Injection Molding
In injection molding, the heat-melted resin is injected into a mold and filled to form it. Since resin is injected and filled at high pressure, products with thin wall thicknesses and complex shapes can be formed at high speed and are suitable for mass production. It is mainly used for the molding of thermoplastics, but in rare cases, it is also used for the molding of thermosets.
The basic principles of injection molding are:
- (1) Material resin is input from the hopper, heat-melted, and plasticized.
- (2) Molded into a certain shape using a mold or the like.
- (3) Cool and harden into the shape of a mold.
After that, the molded product is removed from the equipment and becomes a resin product through various processes and quality inspections. The main products made by injection molding are:
- Smartphone cover
- Electrical product casings and plastic models
- Bath chairs and toilet seats
- Automotive bumpers and interior panels
In this way, it is used for molding and mass production of a wide variety of resin products from small and medium-sized products to large parts, so it can be said that it is a typical resin molding method. Injection molding is further classified into the following methods, depending on the product to be manufactured:
Insert Molding:
It is a molding method in which metal screws and terminals (insert products) are inserted into a mold in advance, resin is injected around it, and molded into an integrated form (composite molding).
Multi-Color Molding And Cross-Material Molding:
It is a molding method that combines resins of different colors and materials and molds them into one piece.
Film Insert Molding And Film-In-Mold Molding:
Film insert molding and film-in-mold molding are used to decorate the surface of logos of resin products, characters, membrane switches of electrical products, and automobile interiors (resin parts such as shift panels), and are called “decorative molding”.
Film insert molding is a molding method in which a film (decorative film) printed on the pattern, gloss, matte, etc. is set in the mold in advance, and the film and resin in the mold are bonded together by heat and pressure during injection molding to make it one. Film-in-mold molding is a molding method in which a decorative film is set in a mold and the decoration of the film is transferred to the resin during injection molding.
Blow Molding
Blow molding is formed by extruding heat-melted resin in a pipe shape, sandwiching it in a mold, blowing air in from the inside to inflate it. It is suitable for the production of hollow resin molded products, and is also called “blow molding” or “hollow molding” from the production method. The main products made by blow molding are:
- PET bottle
- Containers for liquid cosmetics and detergents
- plumbing
- Piping fittings
When filling a liquid, resin may be used differently depending on the characteristics of the liquid. For example, if it is necessary to prevent oxidation due to the permeation of oxygen, a resin with gas barrier properties is used. When chemical resistance is required, multiple molding materials containing resins that are not altered by chemicals are molded in layers.
There are different ways to blow mold depending on the product you are making. Here, we will describe a typical blow molding method.
Extrusion Blow Molding:
The basic structure and principle of the extrusion blow molding machine are as follows:
- (1) Extrude the melt resin.
- (2) Molding a cylindrical parison (hot parison) with a die.
- (3) Do not cool or solidify, put it in a mold.
- (4) Blow air into the mold.
Injection Blow Molding (Injection Drawing/2-Axis Stretch Blow Molding):
The basic structure and principle of injection blow molding machine are as follows: A typical product is PET bottles made of polyethylene terephthalate (PET).
- (1) The thermoplastic resin is injection molded as a test tube preform (cold parison) in advance.
- (2) Heat the preform and stretch it into the mold with a stretching rod.
- (3) Molding by blowing high-pressure air.
Multi-Layer Blow Molding:
For parison, we use materials such as ethylene-vinyl alcohol copolymer (EVOH), which has a high gas barrier, to prevent oxidation and alteration of the contents, and to improve the strength. Therefore, this molding method is suitable for molding resin containers such as cooking oil, seasonings and gasoline tanks.
The basic principles of multilayer blow molding are:
- (1) Two or more kinds of material resins are co-extruded to form a multilayer preform (cold parison).
- (2) Heat the preform (cold parison).
- (3) Blow mold by blowing air.
Three-Dimensional Blow Molding:
Unlike extrusion (direct) blow molding, in which a parison is placed in the longitudinal direction, it is possible to mold three-dimensional shapes that avoid material drawdown and burrs from occurring. This molding method can produce high-quality products with complex shapes with curved parts and bellows, such as hoses and piping for air conditioners.
- (1) The accumulator is filled with resin with an extruder and the parison is molded.
- (2) Air suction is performed from the opposite exit. The parison follows the shape in the mold to the lower part of the mold.
- (3) Blow mold by blowing air.
Poor Assembly And Mating Of Resin Molded Products
Resin molding is easier to process than metal, and by using various materials, the hardness and weight can be changed, and the color and shape can be expressed freely. On the other hand, slight differences in the temperature and filling volume of the material, slight distortion of the mold, etc. cause warpage, swelling, strain, short shot, etc., which cause assembly failure and mating failure.
Poor mating is a defect when bonding or combining resin products that do not fit in size and cannot be bonded or gaps are created. In addition, if a part that has a mating defect occurs is forcibly assembled, there is a risk that the part may be damaged, and it will cause leakage of the contents for parts that require airtightness.
Warping (Sledding) and Undulation
Warping and undulation of resin molded products are a state in which the workpiece is curved like a bow, and are sometimes called bends and twists. In addition, there are forward warping and reverse warping depending on the direction.
On the other hand, a swell is an unevenness on a surface formed by a combination of warps in various directions. Warpage and undulation of resin molded products mainly occur due to the following causes.
- Difference in resin shrinkage
- Uneven mold temperature
- Difference in shrinkage rate of melt resin by flow direction
The difference in resin shrinkage:
Warpage occurs when there is a shrinkage difference in the resin due to variations in temperature and pressure in the cavity. The magnitude of the shrinkage of the resin in the cavity is proportional to temperature and inversely proportional to pressure. For this reason, for example, if there is a thin part and a thick part in one workpiece, the thin part shrinks small because the temperature is low, and the thick part shrinks greatly because heat is stored. This difference in temperature causes a difference in shrinkage in the cavity, resulting in a deformation called warpage.
Uneven mold temperature:
When the temperature of the mold is uneven, the resin in the cavity causes a shrinkage difference and warpage. For example, if the cooling time of the mold varies from part to part, there will be a difference in the amount of shrinkage of the resin, which will cause warpage.
Differences in the shrinkage rate of the melt by flow direction:
The shrinkage rate varies depending on the flow direction of the resin, which causes warpage and swelling. When glass fiber or the like is blended in the resin, the fiber is oriented in the direction in which the resin flows a lot. For this reason, the shrinkage in the direction in which the resin flows is small, and the contraction in the vertical direction with respect to the flow of the resin is large. This is called “anisotropy of shrinkage due to fiber orientation”, and warpage occurs due to this.
Strain
Strain of resin molded products is a phenomenon in which the entire workpiece twists or warps, and is mainly caused by residual stress. Residual stress in resin molding refers to the internal strain remaining in the resin molded product, and there are two types of stress: tensile residual stress, in which a force toward the outside remains, and compressive residual stress, which is directed inward.
Residual stress resin products not only impair dimensional accuracy due to shrinkage and stretching, but also deformation and cracking may occur due to residual stress of resin products during machining such as cutting and grinding, heating such as welding, and processing and processing with coating or solvents. In addition, not only during manufacturing and processing, but also during aging, there is a possibility that distortion may occur due to aging and the shape may change, so special attention is required.
For this reason, treatment to remove residual stress, which is called “annealing (annealing)”, may be performed.
Short Shots
A short shot is a phenomenon in which the resin does not reach every corner of the mold cavity, resulting in an incomplete shape of a part of the mold. The main causes are “fluid tip solidification” in which the resin cools and solidifies before reaching the end and a part of the molded product becomes incomplete, and “air trap” that prevents the resin from flowing smoothly into the mold.
As a countermeasure, in the case of fluid tip solidification:
- Increase the temperature of the polymer to be injected.
- Make the runner thicker.
- Increase the packing pressure or increase the packing time.
- Change the injection rate.
- Increase the surface temperature of the cavity.
- Change the flow pattern.
Resin-Molded Mating Parts Measuring Methods
It is very important to confirm that the resin molded product has the dimensions (within tolerances) and shape as intended. In particular, the mating part of the complex shape part affects the combination work and the degree of sealing, so high accuracy and quantitative measurement of 3D shape is required.
In the past, measurements were made using coordinate measuring machines and calipers, but it was difficult to accurately measure with a coordinate measuring machine, and calipers had various problems such as variations depending on the operator.
Measuring Plastic Molding Parts With Coordinate Measuring Machines
In general, to measure warpage and undulation with a coordinate measuring machine, it is necessary to apply the contact of the probe tip to at least four corners of the surface you want to measure of the object.
For example, in the case of plate members, it is common to measure 6 ~ 8 points. If the measurement range is wide, by increasing the measurement points, it is possible to obtain more measurement values and improve the measurement accuracy. However, in the measurement of warpage and undulation, there were the following issues.
- Since measurements must be made in contact with each other, it is difficult to grasp the shape of the entire object.
- Multi-point measurements to obtain more measurements take a lot of time and do not provide a detailed picture of the overall shape.
Measuring Plastic Molding Parts With Calipers
Hand tools such as calipers can be measured very easily. However, there are multiple factors that cause measurement errors and measurement values to vary.
For example, calipers have different spoonfuls when measuring by different people, such as the force pressed against the measurement point by hand (measuring force) and the variation in the measurement point. As a result, the measured values vary and quantitative measurement becomes difficult. In addition, warping and swelling of a large area required measuring many points, which took time.
Measuring Plastic Molding Parts With 3D Scanning
If you review the challenges of measuring machines that have been used for a long time, you will see something in common. That is, it is measuring while making contact with a three-dimensional object / measurement point with a point or line.
In order to solve these measurement problems, 3D scanner-type coordinate measuring machines. The 3D shape of the object can be accurately captured non-contact and on the surface. You can 3D scan objects on the stage in as little as 1 second to measure 3D shapes with high accuracy. Therefore, it is possible to perform quantitative measurement instantly without variation in the measurement results. Specific benefits include:
Advantage 1 – Scan 3D shapes on the surface. Warping and swelling are clear at a glance
Measuring a resin product with a complex shape with a coordinate measuring machine or caliper required a long time because many points had to be measured. Also, because it is measured at points, it was difficult to measure 3D shapes.
In the case of the 3D Scanner, just place the object on the stage and scan it. Non-contact and positioning-free, it captures the 3D shape of the entire object on the surface. Since it is also possible to display the entire object and measure the profile of any part, it is possible to visualize and grasp the part where the shape defect and its detailed numerical value are displayed.
As a result, it is possible to smoothly confirm molds and molding conditions for trial products, and to identify and take measures against the causes of assembly defects in mass-produced products. Of course, since quantitatively measured shape data can be obtained, it is also possible to manage warpage and swell with numerical values of tolerance values (tolerances) and to use it for trend analysis.
Advantage 2 – Visualization of differences from 3D-CAD data in color
The designed 3D-CAD data and the acquired data can be collated, and the actual finish to the design of the workpiece can be visualized. Even for workpieces that were difficult to measure in the past, by comparing 3D-CAD data with acquired data, defects that were not known until now become clear, so it is effective for investigating mating defects and investigating the cause.
In addition, it can correspond to various dimensional measurements, and by precisely measuring the dimensions of the part you are interested in, you can analyze the problem in detail.
Advantage 3 – It is possible to analyze the cross section without cutting the sample
Even cross-sections, which were previously difficult to measure, can be measured and analyzed in detail by creating cross-sections non-destructively. The reference surface can be freely set from the 3D shape data, and cross-sectional measurement from any direction can be performed.