In today’s highly competitive business landscape, maintaining product quality is paramount. Quality control processes play a crucial role in ensuring that products meet the required standards and customer expectations. Among the various quality control techniques, sampling plans provide an efficient way to assess product quality by examining a subset of items from a larger batch or population.
When it comes to sampling plans, two commonly used methods are single sampling and double sampling. Both approaches offer distinct advantages and considerations that can significantly impact quality control outcomes. Therefore, it becomes crucial for organizations to understand the nuances of each method and select the most appropriate one for their specific requirements.
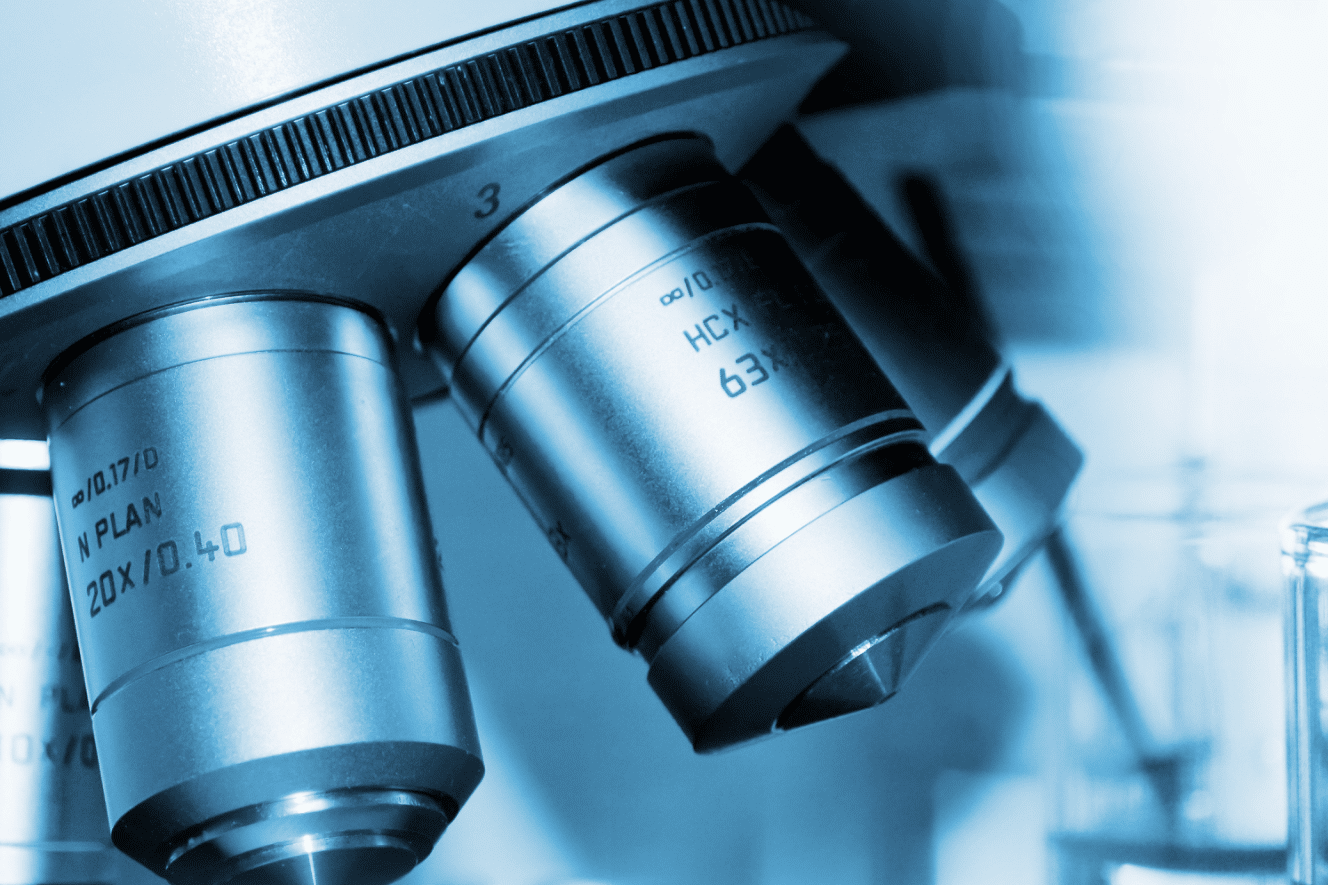
In this article, we will delve into the world of quality control and explore the factors to consider when choosing between single and double sampling plans. We will provide a comprehensive overview of these methodologies, highlighting their strengths, limitations, and applicability in different scenarios. By the end, you will have gained valuable insights into making informed decisions that optimize quality control processes and enhance customer satisfaction.
Now, let’s explore the intricacies of single and double sampling plans and discover how they can impact your organization’s quality control strategies. Feel free to modify and expand upon this introduction to suit your needs. Let me know if there’s anything else I can assist you with!
How To Choose Between Single And Double Sampling Plans
Choosing between single and double sampling plans depends on the specific requirements of your quality control process and the resources available. Here are some considerations to help you make an informed decision:
- 1. Acceptance Criteria: Determine your acceptance criteria for the product or process being inspected. This includes specifications for defects, non-conformities, or other quality characteristics. Consider the level of risk and the criticality of the product or process. Double sampling plans typically offer higher protection against accepting a lot with unacceptable quality.
- 2. Inspection Costs: Evaluate the costs associated with conducting inspections. Double sampling plans involve two stages of sampling, which may require additional resources and time. Assess the availability of personnel, equipment, and budget for inspection activities.
- 3. Lot Size: Consider the size of the lot or batch being inspected. Double sampling plans are often more suitable for larger lot sizes, where the initial sample is used to make a decision to continue or terminate the inspection. For smaller lots, single sampling plans may be sufficient.
- 4. Prior Knowledge: Assess your prior knowledge about the quality level of the lot. If you have some information or historical data about the quality performance of the supplier or process, it can help in determining whether a single or double sampling plan is appropriate.
- 5. Statistical Considerations: Understand the statistical properties of single and double sampling plans. Double sampling plans provide greater precision in estimating the quality level of a lot due to the two-stage nature of the plan. Single sampling plans may be simpler to implement but offer less precision.
- 6. Applicable Standards: Refer to applicable industry standards or guidelines that may recommend or prescribe specific sampling plans based on the nature of the product or process. For example, standards like ISO 2859-1 (for attribute sampling) provide detailed information on various sampling plans and their applications.
The decision between single and double sampling plans should be based on a thorough understanding of your specific quality control requirements. Consider the factors mentioned above and consult with experts or quality professionals to make an appropriate choice.