On the purchasing side, it is important to clarify what you want suppliers to implement as a minimum. The auditee side also has a great opportunity to learn the level of requirements on the supplier’s side.
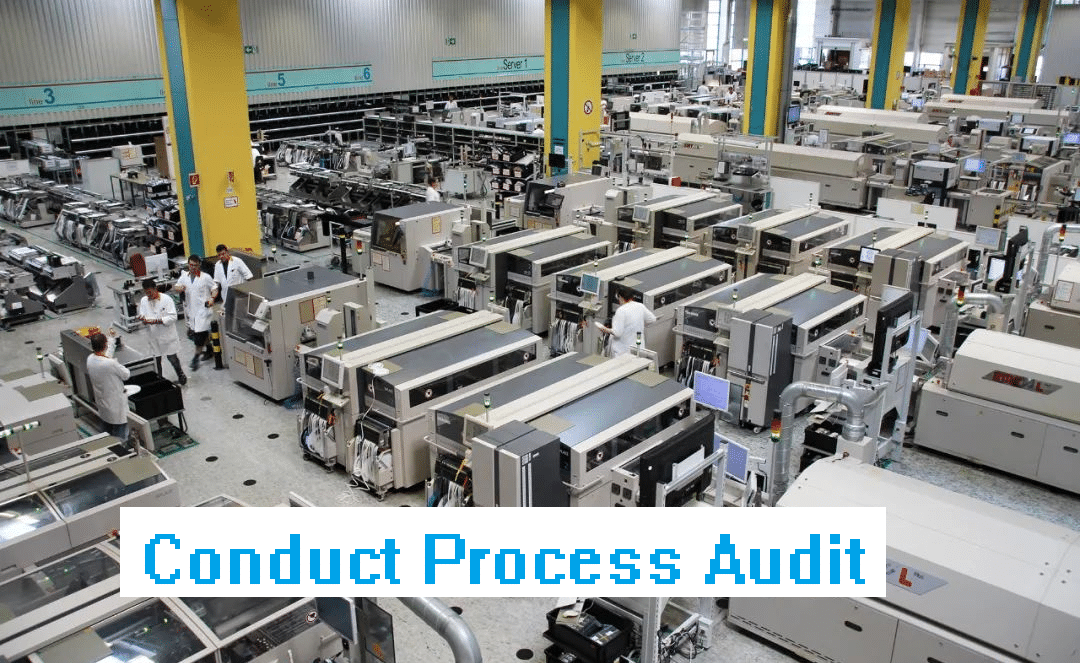
Process quality audit is the focus of the internal quality audit, the purpose of which is to verify whether the factors affecting the production process and its control methods meet the requirements of process control and process capability, to identify existing problems in a timely manner, and to take effective corrective or preventive measures to improve and enhance to ensure that the process quality is in a stable and controlled state. Here we break down the purpose and key points of process audits, as well as how to conduct an effective manufacturing process audit and what to watch out for.
Why Do We Need Process Audits?
Why Is A Process Audit Necessary?
- For purchased products that are directly related to the quality of the company’s products, the purchaser needs to guarantee the quality of the product to the customer.
- In the case of hiring a new supplier, to understand the supplier’s competence, which cannot be determined only by evaluating samples.
If a quality problem occurs with a purchased product that is directly related to the quality of the company’s own products, the quality problem of the purchased product is directly related to the quality problem of the company’s own products.
It will be just as necessary to improve the quality level of suppliers of purchased goods as it is to improve the quality level of your own manufacturing process.
Also, if you are hiring a new manufacturer, it is very likely that the sample will be a champion product. It is important to visit the factory once and confirm whether the supplier is capable of mass production.
How to Conduct an Effective Process Audit
The process audit most enterprises are promoting:
- Checklist
It is important for the purchaser to clarify the items and levels required and share them with the parties concerned. The level of importance is also discussed, and a checklist is compiled.
There are three levels of importance: essential, critical, and better to have. The scoring criteria are: 3 points for acceptable, 3 points for no problem, 0 points for no system, 2 points for improvement, and 1 point for inadequate. It is difficult to put together, but once created, it is convenient to use the same one over and over again.
- Check Items
- Management of drawings/instructions/standard documents
Confidentiality management, latest version management, change management, instructions, etc. The purpose is to make sure that our requests are reflected in our products.
- Information management
We do not want product information to be leaked outside the company, so we check information management within the company and to outside parties.
- QC Process Chart
Is the necessary information included in the QC process? Are the results of risk assessment included? We check if the information required for the QC process is included in the QC process chart.
- Manufacturing process
We check for worker training, necessary equipment and jigs, and work methods.
- Inspection process
Are inspection methods appropriate? Are inspection records kept properly? etc.
- Identification and traceability
It is important to be able to check the process and know what the condition of the actual product is. Also, how much time will it take to actually trace the lot back to the purchased parts and how much time will it take to investigate? We will ask them to confirm how much time it will take to investigate and how much the impact will be spread.
- On The Day Of The Audit
Audit
After receiving an explanation of the process using the QC process chart based on the checklist, we will actually go out to the site to check the necessary items and, in some cases, verify documents.
Closing
Closing is conducted after the checklist has been completed with the details of the day’s checks on the checklist. This is effective because you can immediately see items such as large deviations from your own scoring. Items that we consider important are also scored so they are easy to communicate. Since I usually spent two days auditing, We would work hard on the results of the first day after returning to the lodge, even if it was late, to create the sheet, and on the second day I was given time to complete the sheet before closing. Various areas for improvement would come up and we would decide when they would submit their improvement plans, and then the audit would be over.
Follow-Up After The Audit
We will ask them to report the results according to the improvement plan, and we will confirm the results with a site visit when the time is right.
- Other process audit procedures
Preliminary Preparation
I don’t remember that a check sheet was ever sent to the client, but the sales representative would discuss with the client what the flow of the audit would be, what the agenda would be, what issues would be discussed, and what materials should be prepared on the day of the audit. The sales representative discusses with the client how the meeting will go, what the agenda will be, what issues will be discussed, and what materials should be prepared.
The content of the meeting is communicated to the quality assurance department of the factory, which prepares and confirms the content in advance.
On The Day Of The Audit
Every manufacturer uses a QC process chart to explain the situation and check the manufacturing process and inspection process. This process is generally the same everywhere.
In that sense, identification, traceability, and drawings/instructions/standards are optional, but conversely, we have added these items because many small and medium-sized companies lack awareness of them. Some customers audit according to ISO9001 or, in the case of automotive, ISO/TS16949.
It is generally the case everywhere that action items are summarized at the closing and an improvement plan is submitted by the auditee.
What To Watch Out For In A Process Audit
Things to keep in mind when conducting an audit:
Do not visit in large numbers
- However, the more people who visit the factory, the more difficult it will be for the factory to guide them around the site. If the number of visitors increases, it will be more difficult for the factory to guide them around the site. If they think, “What is this person doing here?
- If it is a factory tour, it is better to go separately for that purpose.
It is not to extract more know-how or technical information about the manufacturing or inspection process than necessary
- Naturally. Even if you have a nondisclosure agreement, the auditor does not have to if they do not want to openly disclose all information. It is a breach of etiquette to ask for more than you need.
Don’t ask for more than the level we require. We tend to point out more details than necessary when we are concerned
- That point may be a big deal.
Suppliers have the right to decide what improvements to make
It is better not to decide on specific measures at the audit, but to have them answered after a separate internal discussion. If we could not say no to the supplier on the spot because of our intention, we would end up talking about it later. The other party may have internal circumstances that they do not want to tell us. It is important to convey your wishes clearly, but it is also important to ask the other party to consider them.
Possibly serviced by customer service. (Not showing their true colors?)
- It is natural to prepare for the customer, but some suppliers mend so much that their true appearance is not visible. Even if it takes some time, it is still necessary to check the documents on the spot, on the case we have appropriately specified.
If delivery is to be prohibited, clearly indicate and promise what will happen when delivery is resumed
- The purpose is communication between the buyer and seller. However, if, in fact, it is necessary to make a decision to suspend deliveries, it is important to explain to that effect, and explain and promise what will happen if the suspension is lifted. In my case, if a critical item was not addressed, I would suspend delivery.
When the process audit reaches a certain level, it should be moved to a quality meeting and followed up in that meeting
There is no need to force process audits to continue. To avoid pointing out more than necessary, let’s encompass it somewhere in the quality meeting.
What Should The Auditee Or The Audited Party Be Aware Of?
- Understand the level of detail required by the auditor.
- Do not give ad hoc answers.
- Be well prepared.
While it is important to understand the level of detail required by the auditor, some clients may point out things that are more detailed than necessary. If you feel that a point is more than necessary, listen carefully to the reason and background.
If you have an idea, they may withdraw it, and if you know the background and reason, you may be able to make other suggestions. It is also important, of course, not to give ad hoc answers. However, we cannot have an internal discussion in front of the client. If the audit is going to last two days, it is a good idea to have an internal discussion after the client has left and start the second day with a review of the previous day’s work.
The client is conducting the audit on the assumption that the process audit will be attractive to them and they will buy the product. You can be confident about that. The person conducting the audit also has a lot of work to do to prepare for the audit.
Process audit not only assured quality but also simplified the line and improved the plant’s ability to perform well. Let’s do our best to build a relationship of mutual trust and growth through audits and suggestions.