How do you know if a plastic product is a low quality or high quality? Some surface defects can be identified by eyes and hands, but accurate measurement needs professional quality inspection service and precision instruments. Here let’s take a look at some common problems in plastic parts, and how to optimize the injection mold for plastic fabrication.
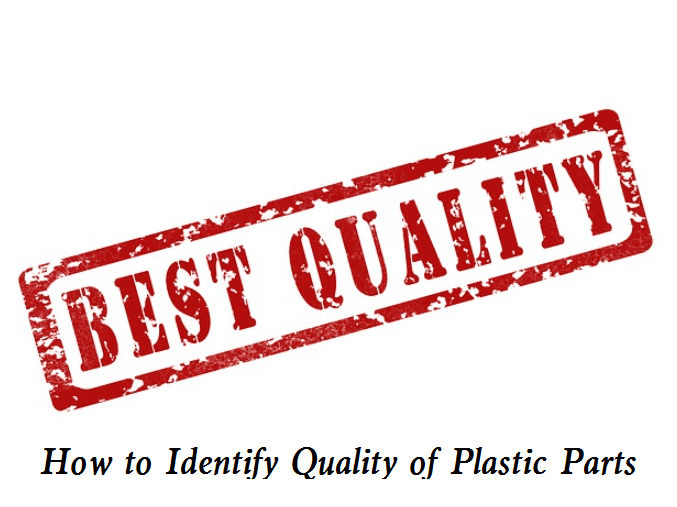
How to Identify Quality of Plastic Parts – Plastic Quality Defects
The common quality problem of plastic parts is first the color difference, which means that the color of the plastic parts is different from the standard color sample under the standard light source by visual observation. Secondly, the injection molding is not satisfactory. This means that the plastic parts are not orderly and the mold cavity is not filled up. Specifically, there are also bubbles, gaps, or shrinkage holes on the surface of the plastic parts.
The warping deformation of plastic parts is also a common problem. The shape of plastic parts will rotate or twist after demoulding or after a period of time, such as straight edges facing inward, or parts facing outward with ups and downs. Generally, there are overall and local deformations. There are also weld lines or ripples during welding. The weld lines generally refer to the linear traces on the surface of plastic parts, which are formed by the convergence of plastics in the mold, while the melts are not completely fused at the intersection. The ripples of plastic parts are generally shown on the surface of plastic parts, showing a spiral or fog-shaped waveform, resulting in an uneven surface.
During the molding process of plastic parts, if the original predetermined size accuracy cannot be maintained, it means that its size is incorrect. If there are pores or bubbles in the plastic parts, it is also unqualified. In addition to these, the surface of plastic parts may also have problems such as mixing corrosion, depression, cold material, white spots, or insufficient strength.
When a thin rubber material appears around the plastic part along the parting line or on the sealing surface of the mold, it indicates that it has an edge overflow problem; The uneven color and poor luster are very obvious on the surface of plastic parts; Because of demoulding, plastic parts will also have similar defects such as deformation, top white, crack, strain, etc.
The defects of plastic parts will not only affect the assembly efficiency or the performance of the whole machine, but also result in a certain difference between the molded products of plastic parts and the quality standards we originally set. The important thing is that they cannot meet the customer’s requirements. These defects of plastic parts may be caused by various factors such as molds, raw materials, process parameters, equipment, environment, personnel operation, etc, Therefore, we should strictly manage all aspects of plastic parts molding. To ensure the quality of our plastic products.
How to Optimize Quality of Injection Molds
Precision injection molding parts are produced by processing injection molds. The quality of injection molds will directly affect the time cost of injection molding and the quality of injection molding parts. So how to improve the quality of injection mold?
- Design of injection mold
In the case of the injection mold design scheme, all aspects should be considered in order to design a good scheme. Including the choice of injection mold raw materials, mold application and safety factors, as well as mold convenience. In terms of raw materials, first, consider that the performance of raw materials specified by customers is an important factor affecting mold quality. Therefore, the required performance of raw materials should be determined according to the specific main purpose, method and other elements of the injection mold. - Manufacturing of injection mold
This is also a key step. The way of production and processing also has a great impact on the quality of injection mold. In the process of processing, in addition to the effective selection of high-precision production and processing requirements, there are many aspects that need to attach great importance to the project acceptance work and select high-precision detection instruments to ensure the accuracy of accurate measurement data information. In order to reduce the possibility of damage during the application of injection molding die, in the case of production and manufacturing, the surface of its parts needs to be strengthened to improve its wear resistance.
- Application of injection mold
In the application process, it is necessary to improve the quality of the injection mold, and reasonably apply and maintain it so that every point can be carried out according to strict requirements, including the installation method, basic parameters, and timely maintenance of the injection mold.