Metal castings are a type of molded articles, how to conduct effective quality inspection on castings? Here are some testing methods to ensure high quality castings.
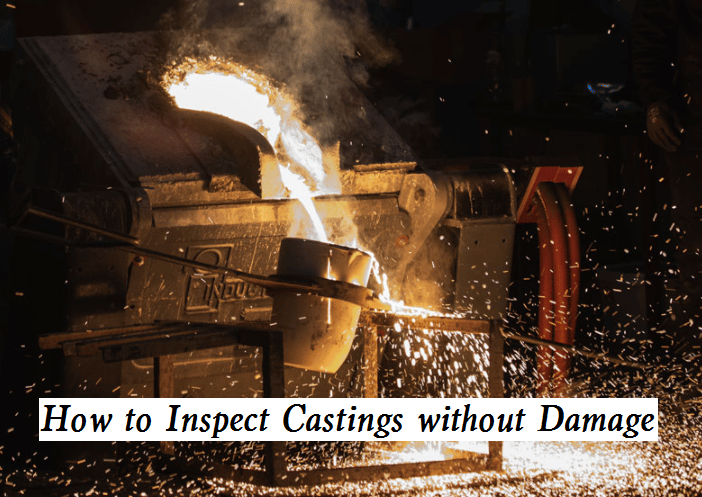
How to Inspect Castings without Damage or Destruction
1) Liquid penetrant test
Liquid penetrant testing is used to check various opening defects on the surface of castings, such as surface cracks, surface pinholes, and other defects that are difficult to find with the naked eye. The commonly used penetrant inspection is color inspection. This method is to correct or spray-colored (usually red) liquid (penetrant) with high permeability on the casting surface. The penetrant penetrates into the opening defect and quickly wipes off the surface penetrant. Then spray a dry display agent (also called developer) on the surface of the casting. After the penetrant of the residue in the opening defect is sucked out, the display agent is dyed to reflect the shape of the defect. Size and distribution. It should be pointed out that the accurate surface of the tested material for penetrant testing decreases with the increase of the surface, that is, the lighter the surface, the better the detection effect. The surface detection accuracy of the polished grinder can even detect intergranular cracks.. In addition to color detection, fluorescent penetrant detection is also a common liquid penetrant detection method.
2) Eddy Current Testing
Eddy current testing is applicable to the inspection of defects with a depth generally not exceeding 6 to 7 mm below the surface. There are two types of eddy current testing: coil placement method and straight through coil method When it is placed near the coil with AC current, the AC magnetic field entering a part will sense eddy current (eddy current) in the direction perpendicular to the exciting magnetic field in the accessory. A magnetic field opposite to the direction of the exciting magnetic field will be generated, which will cause the original magnetic field in some coils, thus causing the change of coil bias. If there are defects on the casting surface, the electrical characteristics of eddy current will be distorted, so as to detect the existence of defects. The main disadvantage of eddy current testing is that the size and shape of the detected defects cannot be displayed. Generally, only the surface location and depth of the defect can be determined.
3) Radiography
Radiographic examination, usually using X-ray or γ Ray is used as radiation source. Therefore, equipment and other auxiliary facilities are required to generate radiation. When the target is exposed to the radiation field, the radiation intensity of the radiation will impact the influence of the internal defects of the casting. The radiation intensity emitted by the casting will change locally with the size and nature of the defect, thus forming the radiographic image of the defect. The image is developed or recorded by the radiographic film, or real-time detection and observation are conducted through the fluorescent screen, or detection is conducted through the radiation counter. The method of developing and recording is the most commonly used method, which is usually called radiographic inspection.
4) Ultrasonic testing
Ultrasonic testing can also be used for internal defects. It uses the sound beam of high-frequency sound energy to spread inside the casting. When they meet the internal surface or defect, they will reflect and find the defect. Therefore, acoustic ultrasonic testing of various defects or internal surface reflection is widely used. Its main advantages are high detection sensitivity, small cracks can be detected; It has strong penetrability, and can detect thick wall castings. Its main limitation is that it is difficult to explain the reflection waveform of discontinuous defects with poor size and directivity, used for poor internal structures, such as dimensions and organization.