IATF 16949 is a global standard for quality management in the automotive industry, and an IATF 16949 audit is conducted to assess whether an organization’s quality management system (QMS) is in compliance with this standard.
The purpose of the IATF 16949 audit is to determine whether the organization has implemented an effective QMS that meets the requirements of the automotive industry. This includes ensuring that the organization is consistently providing products and services that meet customer requirements, while also focusing on continuous improvement of their processes and systems.
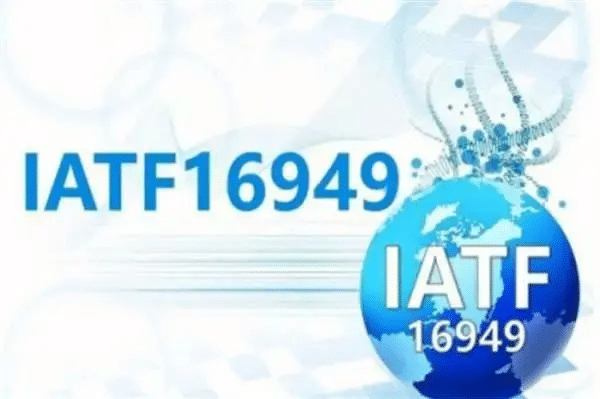
The IATF 16949 audit helps to identify areas where the organization can improve their quality management system, and also ensures that the organization is meeting the expectations of its customers and the automotive industry as a whole. Additionally, being certified to the IATF 16949 standard is often a requirement for doing business in the automotive industry.
How To Perform IATF16949 Audit?
Performing an IATF 16949 audit requires a systematic approach and an understanding of the standard’s requirements. Here are the general steps involved in performing an IATF 16949 audit:
- Planning: The first step is to plan the audit, which involves defining the scope, identifying the audit team, and determining the audit schedule.
- Conducting the audit: During the audit, the audit team should verify whether the organization’s QMS is compliant with the IATF 16949 standard requirements. This is done by reviewing documentation, observing processes, and interviewing personnel.
- Reporting: After completing the audit, the audit team should prepare a report that includes findings, non-conformances, and opportunities for improvement.
- Follow-up: The audit team should follow up with the organization to ensure that any non-conformances have been addressed and corrective actions have been taken.
When performing an IATF 16949 audit, it’s important to keep in mind the key principles of the standard, which include customer focus, leadership, engagement of people, process approach, improvement, evidence-based decision making, and relationship management. The audit should focus on verifying that these principles are being effectively implemented within the organization’s QMS.
Basic Steps for IATF16949 Audit
Here we outlines the basic steps for conducting an audit according to the IATF 16949 standard, including audit planning, audit preparation, on-site audit, and audit reporting.
STEP 1 – Audit Planning
1.1 – Planning for the Audit: Audit Plan; Annual Audit Plan
- Definition of Audit Plan: A set of (one or more) audit arrangements planned for a specific time period and with a specific purpose.
- Definition of Audit Schedule: Description of the activity and arrangement for an audit.
1.2 – Audit Preparation: Audit Implementation Plan; Checklists
Determine the audit team, prepare the audit implementation plan, prepare checklists, and communicate before the audit.
1.2.1 – Determining the Audit Team
- Selection of Audit Team Leader: A) Qualifications B) Business Scope C) Work Experience D) Organizational Capability
- Selection of Auditors: A) Qualifications B) Business Scope C) Professional Knowledge D) Coordination in Work E) Accepted by the Audited Department
1.2.2 – Audit Implementation Plan
Key points for developing the audit implementation plan:
- Cover all requirements and certification scope (locations and activities);
- Consider the status and importance of audit activities and regions;
- Assign personnel with professional backgrounds and abilities to important product realization processes;
- Pay attention to the independence of auditors.
After the audit implementation plan is approved, it should be distributed to each department being audited one week in advance. The audit implementation plan should include: audit objectives, audit scope, audit basis, audit team members, audit dates, audit schedule, audit report release date and scope.
1.2.3 – Preparation of Checklists
Functions of Checklists:
- Provide a roadmap to guide the entire audit process
- Clarify the audit points and methods
- Ensure audit coverage
Key points for developing checklists:
- Understand the division of labor in the department’s quality functions
- Rely primarily on the quality management system documents
- Highlight the main functions of the audited area
- Be detailed and appropriate
- Checklists should be operable
- When auditing by department, the relevant requirements should be included
- When auditing by requirements, the relevant departments should be included
1.2.4 – Pre-Audit Communication
- Notify the department being audited in advance
- Internal meeting of the audit team (if necessary)
STEP 2 – Audit Implementation
2.1 – Opening Meeting
- Audit sign-in
- Introduction of audit team members
- Introduction of audit objectives and scope
- Confirmation of the audit plan arrangement
- Introduction of audit methods and procedures
- Confirmation that the necessary resources and facilities are available for the audit team
- Clarification of questions
- Confirmation of the timing for the mid-term and closing meetings
2.2 – On-Site Audit
- Collect objective evidence through questioning, interviews, examination of documents, observation of relevant work and conditions, and other means in accordance with the audit checklist.
- If significant clues that may lead to non-conformity are found, they should be recorded and investigated even if they are not listed on the checklist.
- Information obtained through interviews should be verified through actual observation, measurement, and recording.
2.2.1 – On-Site Audit Precautions:
- Auditors should randomly select samples
- Trust the samples
- Do not completely deviate from the checklist
- Look for objective evidence through problem phenomena
- When non-conformities are found, trace them to the necessary depth
- Confirm the facts with the responsible person of the audited organization
- Always maintain objectivity, fairness, and courtesy.
2.2.2 – On-Site Audit Note Contents
- Evidence of non-conformities found during the audit
File name, number, version; Product or service name, identification; Area/workstation; Equipment name/location; Record name/identification/time; Description of the non-conformity
- Audit clues
2.2.3 – Nature of Non-Conformities
- Systemic Non-Conformity: Management system documents do not comply with standards, regulations, contract requirements
- Implementation Non-Conformity: Failure to follow management system documents
- Effectiveness Non-Conformity: Although the management system documents are followed, they lack effectiveness
2.2.4 – Types of Non-Conformities
- Major Non-Conformity:
Systemic failure in the operation of the management system
Regional failure in the operation of the management system
Non-conformities with significant impact on the operation of the product or management system.
- Minor Non-Conformity:
For meeting the requirements of the management system process or documentation, it is an isolated, occasional, minor problem in nature.
For ensuring the effectiveness of the audited area’s management system, it is a minor issue.
2.2.5 – Key Points of Describing Non-Conformities
- Accurately describe the observed facts, including the time, location, people, and circumstances, making them traceable and verifiable.
- Strive for brevity and conciseness, summarizing and extracting the core non-conformities and avoiding irrelevant or redundant information.
- Analyze and summarize statistical data and do not omit any useful information.
2.3 – Audit Team Meeting
- Held after the on-site audit and before the closing meeting, or regularly during the audit process (at the end of each day)
- Attended by all audit team members
- Discusses audit findings
- Communicates audit information and leads
- Coordinates audit direction
- Audit team leader prepares the audit summary.
2.4 – Closing Meeting
- Attendees sign in
- Express gratitude
- Reinforce audit objectives and scope
- Confirm implementation of the audit plan
- Formally identify non-conformities
- Clarify any issues
- Announce audit conclusions
- Propose corrective actions and requirements
- Conclude the audit.
STEP 4 – Follow-up Verification
4.1 – Development of Corrective Actions
The department responsible for the non-conforming item shall analyze the causes of the problem.
- Corrective action plans should be developed based on the causes of non-conformance.
- The description of the corrective action should be specific.
- Auditors can assist the audited department in analyzing the causes of non-conformance and proposing corrective action recommendations.
- Corrective actions should be approved by the responsible person of the audited party.
4.2 – Corrective Measures
- Corrective measures may include
- Revision of existing documents
- Training of personnel
- Improvement of current work methods to align with documents
- Increasing resources
4.3 – Audit Follow-up
Verification Time
- Verification should occur at the deadline specified in the nonconformance report, or earlier if the audited party implements corrective measures before the deadline.
Verification Content
- Has the plan been completed as scheduled?
- Have all measures in the plan been completed?
- What has been the effect since corrective measures were taken? Have similar nonconformances occurred?
- Are there any records of implementation that can be checked?
- If the nonconformance resulted in changes to quality system documentation, was the document control process followed?
Verification Record
- The verification record should briefly describe the verification content and conclusions.
- If the verification results indicate that the nonconformance report cannot be closed, note the date for further follow-up or the number of a new nonconformance report.