Reverse engineering is a method that is currently attracting attention because it brings great benefits in the development and part manufacturing processes. For example, it has many effects such as shortening the development period and reducing development costs in the development process, restoring aging molds, and duplicating parts without drawings in the manufacturing process. On the other hand, issues such as the complexity of the coordinate measurement work and the high level of technology and man-hours required were issues.
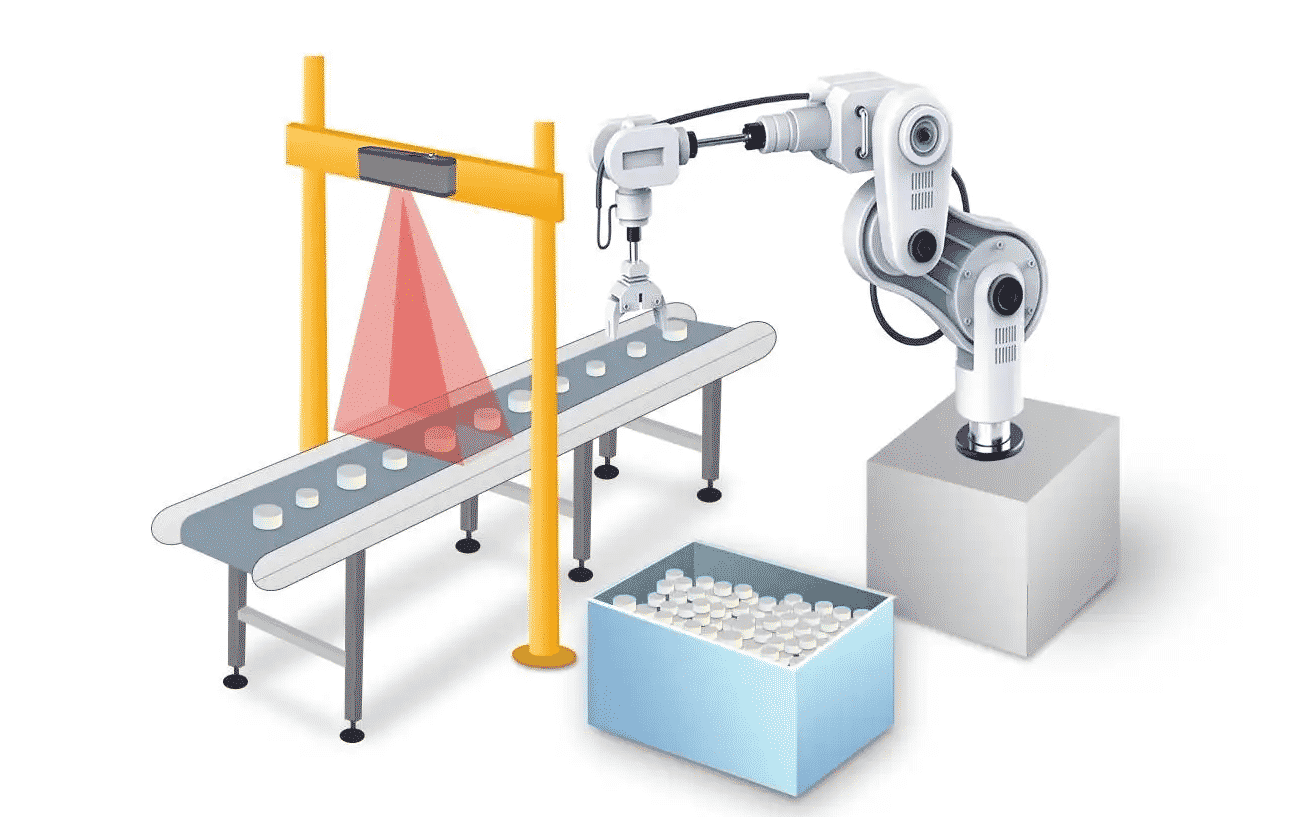
However, 3D scanners, which have become popular in recent years, are expected to solve these problems. Here, we will explain the basics of reverse engineering and the 3D scanners used in it. In addition, we will introduce the points of problem solving.
What is Reverse Engineering?
Reverse engineering is the process of analyzing the structure of products, parts, and software, and investigating and measuring components, source code, etc. to clarify technology and design.
In the manufacturing and processing industries, it is a method of measuring the shape of products and parts and creating design drawings. Normally, products are created based on blueprints, but since they proceed in the process of creating blueprints from products, they are called reverse engineering.
A Product B Reverse Engineering
(1) Shape measurement
(2) Analysis / data processing
(3) CAD data design document
What can be done with reverse engineering?
In reverse engineering, you can reproduce blueprints by measuring the real thing and creating CAD data. For example, you can reproduce blueprints such as parts that cannot be used because they are competitors of other companies, products for which the manufacturer has gone bankrupt or the product is old and no blueprints remain, or products for which detailed blueprints do not exist because they are prototypes.
Development by reverse engineering develops new products with reference to the blueprints of existing products, so development time and costs can be reduced. It also has the added benefit of shortening development cycles and bringing new products to market faster than other companies.
In the manufacturing process, restoration of aging molds and duplication of parts without drawings leads to the maintenance of manufacturing quality and the acquisition of new projects.
Laws to be observed in reverse engineering
Reverse engineering is a legal act. However, there are cases where products contain various patents and copyrights, so you must pay close attention so as not to infringe intellectual property rights when using the analysis results.
For example, if a patent related to technology is acquired, or if technical information violates the three requirements of trade secrets (confidentiality, usefulness, and non-public intelligence) of the Unfair Competition Prevention Act, it may not be available.
In order to use the information obtained by reverse engineering, it is necessary to confirm that it does not violate the patent law and the Unfair Competition Prevention Act.
3D Scanner Used in Reverse Engineering
It is no exaggeration to say that reverse engineering, which is indispensable for measuring the dimensions of each part of a product, has been realized by improving the performance and lowering the price of 3D scanners capable of 3D scanning. 3D scanners can be broadly divided into contact and non-contact types, each with its own strengths and weaknesses.
What is 3D Scanning?
3D scanning is a technology that converts the 3D shape of an object (product) into digital data, and is also called “3D digitization”. LED light, laser light, or probe is applied to the surface of the product to detect unevenness, and X (height), Y (width), and Z (depth) coordinate data are acquired to create 3D data. increase.
Contact 3D scanner
The contact type 3D scanner applies the contact to the measurement point called the “probe” and acquires the unevenness as coordinates. It has better measurement accuracy than the non-contact type, and can measure even products that cannot be measured by the non-contact type due to the gloss of the surface.
On the other hand, it is difficult to measure in a narrow area where the probe cannot be inserted. There are also restrictions on the size of products that can be measured. In addition, since it is a point or line measurement, it takes time to acquire the data if the object is a large surface.
A typical measuring machine is a portal type 3D measuring machine.
Non-contact 3D scanner
By shining LED light or laser light on the product, the time difference and reflection angle until the reflected light arrives are analyzed to acquire the 3D shape.
Scanning methods include pattern projection and laser cutting. In addition, there are stationary type and handy type, and you can use it properly, such as scanning with the stationary type first and then scanning the part that cannot be scanned with the stationary type with the handy type. However, the measurement accuracy of the handy type may decrease due to camera shake. In addition, even with the stationary type, it is required to be a 3D scanner that can not only grasp the overall shape but also measure coordinates, geometrical tolerances, and cross-sections.
X-ray CT scanner
The X-ray CT scanner is a 3D scanner that can measure not only the external shape but also the internal state. It is used for non-destructive inspection because it measures using the same principle as a medical CT scanner and can inspect not only external dimensions but also cracks, air bubbles, and foreign matter inside cast products and weld beads. However, the range of use is limited due to the high cost of the equipment.
Utilization of 3D Data in Reverse Engineering
CAD data can be created and simulation analysis can be performed based on 3D scanned measurement data. It is also possible to generate data for molding with a 3D printer or processing with CAM.
Create CAD data
CAD data can be created by generating data that expresses the shape of the surface called “surface data” from the measurement data and deleting unnecessary surface data. This allows you to create 2D-CAD or 3D-CAD data for products that do not have drawings.
Use for 3D printers and CAM
Interpolates data where 3D scanning could not be obtained to create a mesh data that is not chipped. This data is called “STL (Stereolithography) data” and is a type of file format for 3D-CAD software and is supported by most software. It is the most used file format, especially for rapid prototyping with 3D printers. By using this data, even products without drawings can be molded with a 3D printer. In addition, it can also be used in CAM, so you can control the NC machine tool and regenerate the product.
Used for simulation analysis
If you have CAD data, you can simulate various evaluations such as flow analysis, heat resistance evaluation, and strength evaluation. By evaluating and analyzing while changing the dimensions, it is possible to efficiently rotate the PDCA cycle. It also leads to the prevention of malfunctions.