PPAP is one of the five tools of the TS16949 quality management system and is used for quality control in the production process of automotive vehicles or parts. PPAP is not simply the submission and approval of documents, but rather a complete process to confirm whether the supplier is capable of producing qualified products in bulk and with stability.
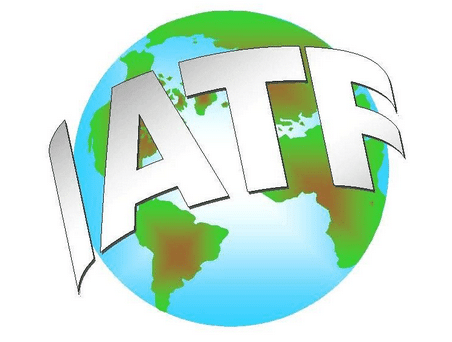
This article revolves around the following five steps to briefly explain the main tasks, inputs, and outputs of each stage of the PPAP process, and strives to identify and solve as many problems as possible before part production and process development.
I. PPAP Start-up Phase
In the start-up phase, it is best for SQE to jointly conduct a QAC review meeting with various departments of the supplier to fully interpret the drawing standards and requirements. Each department of the supplier and SQE inputs their experiences and lessons, and SQE inputs the work requirements and some special requirements of the OEM. It is best to reflect the key focus on the three major documents.
The purpose of this phase is to plan the entire APQP process, determine the plan nodes of the five stages of APQP, the list of PPAP submission documents, and the list of deliverables for each stage. At the same time, KPC/KCC list, mistake-proofing list, etc. need to be outputted.
II. OTS Approval Stage (Tooling Samples)
In this step, based on the supplier’s experience and capability requirements, the initial version of FMEA, process flowchart, control plan, and product traceability plan should be developed.
The OTS tooling sample is not a formal PPAP sample, mainly for the supplier to confirm whether their process capability can meet all tolerance and feature requirements. If SQE has time, it is best to track the production on-site and confirm the quality status of the tooling sample. If the supplier finds that their capability is not enough after the practice, they must be able to raise issues such as unreasonable drawings and overly strict tolerances. If it is not mentioned at that time, it will be difficult to change later. If the OTS sample does not meet the requirements, problem correction must be completed first.
The main focus is on the following documents and content:
- Three major documents;
- Dimensional measurement plan;
- Test outline;
- Supplier list;
- OTS sample and sample measurement report;
- Final signed drawing: drawing signed by the product engineer PE;
- Tooling and fixture list;
- Measuring tool list;
- Tool and inspection aid review and inspection documents;
- Mold and fixture inspection report.
III. PPAP Authorization Stage
Based on the actual situation and the supplier’s application, SQE evaluates whether the supplier has the conditions for PPAP production, determines the PPAP submission level, clarifies the PPAP trial production audit method, and determines the list of submission documents.
In this stage, the supplier submits a PPAP application, and SQE reviews the application materials and completes the authorization. If the PPAP production conditions are not met, corresponding effective measures should be developed in a timely manner for improvement, and the PPAP trial production plan should be re-established to avoid affecting the project nodes.
The main focus is on the following documents and content:
- The trial production control plan, production control plan, process flowchart/FMEA, and GP-12 related content have been preliminarily locked.
- OTS/drawings/supplier list/ADV/FE/AAR/3C/key components/software versions have been locked.
- The development status of tooling/mold/fixtures/inspection tools/equipment/production lines/process has been preliminarily locked.
- The required documents/operation/inspection guide and other documents/personnel training/KPC identification have been completed.
- Confirmation of internal and external turnover racks, line-side racks, and workstation tools has been completed.
- Completed critical supplier PPAP, quantity meets trial production requirements, and critical supplier implements GP12.
IV. PPAP Approval Stage
The first batch of PPAP samples is produced continuously for 8 hours or 300 pieces under the formal production tooling/mold/inspection tools/process/materials and operator. SQE should go to the supplier’s site, carefully review each process step with the control plan and PFMEA, and finally confirm the physical quality of the parts (dimensions/materials/performance) and PPAP sealed samples.
Raw materials: incoming inspection, confirmation of compliance with the supplier list, warehousing, turnover logistics
Production/inspection process:
- KPC project control effectiveness/KCC/mistake-proofing verification;
- Production/inspection personnel configuration;
- Compliance of the three major documents;
- Compliance of equipment/process parameters;
- Stability of tooling (mold/fixture) in the production process;
- Whether the operator and inspector follow SOS operations;
- Whether the production cycle (tooling/equipment) meets the requirements;
- Turnover/packaging/storage/shipping of semi-finished and finished products;
- Management of suspicious materials;
- Confirmation of part identification (traceability)
- Implementation of GP12.
- Confirmation of multiple cavity molds or machining equipment/production units/multiple production lines.
The main focus is on the following documents and content:
- Certificate of conformity;
- Full-size measurement report;
- Test report;
- MSA report;
- Initial process capability analysis report;
- PPAP on-site production problem correction report.
V. Mass Production
The main focus is on the following documents and content:
- PPAP on-site production problem correction;
- Tracking the correction of temporary PPAP approvals;
- PTR (if necessary, generally not required for new vehicle development);
- Implementation and withdrawal of GP12;
- Continuous improvement of outstanding issues.