Even if it is said that resin molding processing is said to be a mouthful, there are various methods such as “injection molding“, “extrusion molding”, “transfer molding”, “compression molding”, etc. And since there are various types and causes of defects that occur during molding, it will take a lot of time and cost if you do not grasp the causes and countermeasure methods of each. However, now that the shortage of human resources is becoming chronic, there are many cases where even if you know the cause and countermeasures, you can not cope with it.
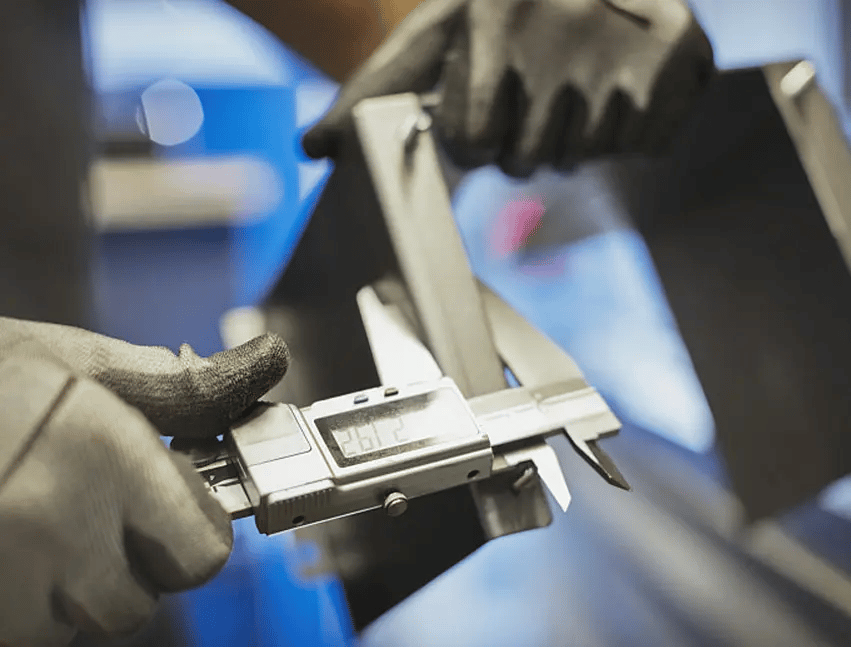
Therefore, we recommend quality inspection using AI. This time, after looking at the main types and countermeasures for molding defects, we will tell you about quality control by AI that minimizes the time and effort of correspondence.
What Is Injection Molding Defect?
In order to know the main types of molding defects and countermeasures, it is first necessary to know what molding defects are. Molding defect refers to the occurrence of defects or defects in terms of appearance or performance of the molded product when resin molding.
What are Resin Molded Products?
A resin-molded product is a product that is molded by melting resin (plastic), putting it in a mold, cooling it, and hardening it. As mentioned at the beginning, there are various molding methods, but the most commonly used is injection molding, which is suitable for mass production. It is called injection molding because it injects molten resin in a form similar to injecting a syringe.
Types Of Major Molding Defects, Causes, And Countermeasures
There are various types of molding defects, but the main types, their causes, and countermeasures are as follows:
Burr
Burr refers to a state in which resin protrudes during molding and unnecessary parts remain in the molded product. It can be inferred that there are many causes of gaps that protrude such as “the tightening of the mold into which the resin is injected is loose”, “the accuracy of the mating surface of the mold is low”, “the temperature of the resin is high”, “the injection speed is too fast”, etc.
Therefore, it is necessary to take measures such as “increasing the pressure of tightening”, “increasing the accuracy of the mating surface part of the mold”, “lowering the resin temperature”, and “adjusting the injection speed”.
Cobwebbing
Stringing refers to the state in which the part that is not firmly solidified stretches like a string when the mold in which the resin is injected is opened. In many cases, the cause is that the temperature of the nozzle part of the molding machine is high and the resin does not completely harden.
Possible countermeasures include “lowering the temperature of the nozzle” and “prolonging the cooling time.” However, if the temperature is lowered too much, molding may deteriorate, so be careful.
Silver Streak
Silver streak refers to a condition in which silver-white streaks remain on the surface of the molded product in accordance with the direction in which the resin flows. Possible causes include “insufficient drying of materials”, “there is a temperature difference between the cylinder part of the molding machine and the mold”, “the injection speed is too fast and the air is involved”.
The most important countermeasure is to dry the resin sufficiently before molding. Since the main cause of silver streaks is the generation of moisture caused by lack of drying or temperature differences, it is necessary to prevent the generation of moisture by “drying the resin firmly” and “adjusting the temperature of the cylinder part of the molding machine and the mold”.
Flow Mark
Flow mark refers to a state in which traces of melted resin remain as a ring-shaped wavy pattern on the surface of the molded product. In an environment such as “the temperature of the resin is low” or “the injection rate is slow”, it is thought that the main cause is that the resin cools down while flowing in the mold.
Since it is necessary to improve the fluidity because the resin does not harden during molding, countermeasures such as “increasing the temperature of the resin” and “increasing the injection speed” are considered. It is also effective to set the pressure at the time of injection to a higher level.
Short Mold
A short mold, also known as a short shot, is a condition in which a specific part of the mold is cooled without the resin being filled. As a result, when the mold is opened, only the part where the short mold occurred is chipped.
The cause may be “insufficient resin”, “poor fluidity of resin”, “low temperature of mold”, “insufficient injection pressure”, etc.
As countermeasures, “increase the amount of resin to be injected”, “raise the temperature of the mold”, “increase the injection pressure”, etc. are effective. In addition, as a cause of poor resin flowability, there is a possibility that the performance of the molding machine is insufficient, so it may be necessary to change the molding machine.
Void
A void is a bubble. When processing into a shape with thickness and uneven thickness, only the surface of the thick part hardens first, and the inside contracts and solidifies later, which causes vacuum bubbles to occur.
The cause is that the cooling time between thin and thick parts is not evenly due to “low mold temperature”, “high injection temperature”, “the position where the resin is injected is not appropriate”, “the resin drying is insufficient”, etc.
As a countermeasure, it is necessary to devise a way to make the cooling time between thin and thick parts uniform, such as “raise the temperature of the mold”, “lower the temperature of injection”, “set the position where the resin is injected so that it can be injected at right angles to the thick part”, “sufficiently dry the resin”.
Sled
A warpage is a condition in which a part of a molded product warps. This occurs when the shrinkage of the filled resin is not evenly distributed by location. The causes are “short cooling time”, “high mold temperature”, “short injection and packing time”, “low injection pressure”, “slow injection speed”, etc.
As a countermeasure, in order to eliminate the situation where shrinkage becomes uneven depending on the location, “take a longer cooling time”, “lower the temperature of the mold”, “take a longer time for injection and packing”, “increase the injection pressure and increase the injection speed”, etc.
Weldline
Weld line refers to a state in which when the injected resin branches once in the mold and merges again, it cannot merge well and a linear mark occurs. The cause is that the temperature at the point where the divergent resin merges is low, and it solidifies before merging. In addition, the flow resistance in the mold is large, and one of the causes of weld lines is that the resin does not flow smoothly.
As a countermeasure, it is effective to increase the speed and pressure amount when injecting resin. It is also necessary to raise the temperature of the resin so that it does not harden at an early stage.
In addition, it is also important to keep the flow resistance as small as possible, such as increasing or shortening the area where the resin flows in the mold, and finishing the surface smoothly.
Crack
A crack is a condition in which a part of a molded product is missing or has a thin crack. Cracks are sometimes referred to as crazing rather than cracking.
Cracks are caused by internal stresses generated inside the mold that have been subjected to external forces. The causes include “high injection and holding pressure”, “high injection speed”, “low mold temperature”, “short cooling time”, etc. In addition, the force when removing from the mold is too strong may also cause cracks.
Measures include “lowering the injection and holding pressure,” “slowing down the injection rate,” “increasing the mold temperature,” and “increasing the cooling time.” In addition, it is also an effective measure to slow down the speed when removing from the mold so as not to apply strong force.
Drawing
Drawing is a phenomenon also called “leaning off” or “nose drop”, and refers to a state in which resin leaks out from the tip of the molding machine. Normally, the molding machine injects a fixed amount of resin every time, so if the resin leaks out, it will not be possible to inject a sufficient amount. As a result, it is not possible to inject enough resin for the next mold, which causes short molding.
Causes of drawing include “slow injection rate” and “low injection pressure”. Therefore, it is necessary to take measures such as “increasing the injection speed” and “increasing the injection pressure”. However, if you increase the injection speed too much, the surrounding air will be caught and cause a silver streak, so you need to set the speed appropriately.
Jetting
Jetting is the condition in which a snake-crawled mark remains on the surface of a molded product. The main cause is that the resin injected from the molding machine first and the resin that came in later do not fuse well and solidify.
It is a phenomenon that occurs mainly when the injection speed is high, and the resin injected first strongly hits the bottom surface of the molded product, and the high-temperature resin that comes later collides with the place where it returns with the temperature dropped. Because of the temperature difference, it solidifies halfway, leaving a trace that looks like a meander.
As a countermeasure, it is a good idea to reduce the injection speed and raise the temperature of the mold so that it does not harden halfway.
Cold Slag
Cold slag refers to a state in which the temperature of the resin drops and solidifies when the tip of the nozzle where the resin is injected by the molding machine comes into contact with the mold. As a result, there is a risk that the resin does not flow well into the mold and causes a short mold, or the resin at a low temperature flows into the mold and becomes a flow mark.
As a countermeasure, it is effective to install a cold slag that serves as a reservoir for the resin when cold slag occurs on the mold side. If a low-temperature resin flows here, it will be possible to avoid inflow into the molded product.
In addition, cold slag can be prevented by increasing the temperature of the mold and increasing the injection speed. Furthermore, by shortening the nozzle touch time and reducing the time it takes to come into contact with the mold, the temperature drop of the resin can be avoided and cold slag is less likely to occur.
Yake
Yake refers to a condition in which resin is injected into a mold and the molded product becomes discolored due to excessive heating. As a cause, there is a case where the flow of resin is poor in the molded product, and the air in the mold and the gas generated from the molding material are accumulated and compressed in that part, and the resin becomes hot. In addition, the cylinders and nozzles of the molding machine are too hot, and the residence time is too long, which is also a cause of burning.
As a countermeasure, after lowering the injection speed and pressure, vents are installed to exhaust air and gases. It is also effective to reduce the molding temperature or, if the residence time is long, review the molding cycle and change to a molding machine of the appropriate size.
Issues and Solutions for Appearance Inspection of Molded Products
In the previous section, we have looked at the various types and causes of molding defects, as well as countermeasures. If you grasp these, even if a defect occurs, you can immediately understand the cause and respond appropriately.
However, first of all, it is necessary to conduct a visual inspection to determine whether these molding defects are actually occurring. The problem is that all the inspections have been done visually.
Partly due to the declining birthrate and aging population, the shortage of human resources has become a serious problem in many occupations at present, but it is also the same in the manufacturing industry. Under such circumstances, if it is necessary to visually inspect the appearance of resin molded products, other work hours will be cut by that amount, and the burden on employees will increase.
In addition, since experience and intuition are important in finding molding defects among mass-produced resin molded products, visual inspection tends to be dependent on the individual. Therefore, if you try to replenish personnel, it will take a considerable amount of time and cost to train.
Therefore, it is recommended to utilize an image processing system that prevents the dispensation of inspections and enables accurate and rapid visual inspections without relying on visual inspection.
The image processing system compares molded products at the surrounding shading level, and quickly detects defects and defects without overlooking fine scratches and dirt that are difficult to see visually. In addition, since detailed customization is also possible, you can flexibly set the judgment criteria for how far to make it defective. As a result, it is also possible to extract only fine dirt without detecting areas above a certain level, such as product shape and printing, as defects.
Summary
There are various types of molding defects, and in order to ensure the quality of products, it is essential to conduct inspections that can detect all kinds of defects. In addition to grasping the basics of quality control, it is also necessary to understand the latest technology.
Some materials summarize the basics of quality control and detection using the latest AI, so if you have problems with quality control, please take a look.