One of the defects that can occur when manufacturing injection molded products is weld lines, which pose a risk of reducing the product’s strength. While preventing weld lines completely is not easy, it is possible to anticipate and mitigate their occurrence to some extent.
In this guide, we will provide you with essential knowledge about weld lines, including the causes and methods for prevention.
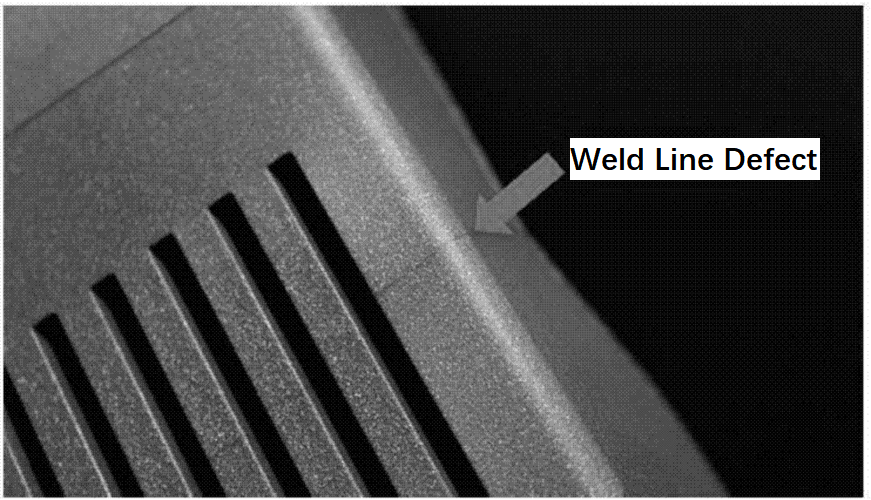
What is Weld Line?
Common molding methods for plastics include “vacuum forming,” “compression molding,” and “laminate molding” for thermosetting resins, and “injection molding,” “blow molding,” and “extrusion molding” for thermoplastic resins.
Among these methods, the molding process where weld lines occur is “injection molding,” which is a molding method for thermoplastic resins.
Weld lines refer to line-shaped patterns that appear on the surface of the molded product, resembling scratches on the product at first glance.
In reality, although it is just a line-shaped streak, the area where weld lines occur has reduced strength due to inadequate blending of the resin. Even a slight impact can easily cause cracks or breakage, posing a high risk of molding defects that can lead to complaints from clients and consumers.
Causes of Weld Lines in Injection Molding
Why do weld lines occur in injection molding? Here I will explain the causes of weld lines and why the occurrence of weld lines can lead to reduced strength.
To understand the causes of weld lines, you first need to know what injection molding is.
Injection molding is a molding method where melted resin is injected from an injection machine into a mold to form products. It is suitable for making thin-walled products and products with complex shapes, and has various merits such as being able to quickly produce large quantities of products without needing finishing steps.
Weld lines occur during injection molding at the location where the injected resin branches and then re-joins within the mold.
As mentioned above, injection molding is often used to make products with complex shapes, and the resin injected into the mold branches off in various directions. As the resin flows through these branches, its temperature drops. If the tip of the resin has already solidified when the flows re-join, they cannot blend together well. The solidified resin collides, creating a visible weld line. This is the main cause of weld line generation.
There are two main types of weld lines depending on the mold design:
Opposite flow weld
In a mold with a hole, the resin branches and flows in a circular pattern, with the tips merging from opposite directions. Since the solidified tips collide head-on, a deep V-shaped groove forms at the joint, making the weld line very conspicuous.
Parallel flow weld
Resin injected from multiple gates flows in the same direction and merges. Because the flows are parallel when merging, the V-shape is shallower than in opposite flow welds, and the weld line is less pronounced. Another pattern occurs when injecting resin into a mold with extremely different thicknesses. The resin flows easily through thicker sections but has more difficulty flowing through thin sections. When the resin flows from a thin section to a thick section, it tends to solidify more, making weld lines more likely to form.
Can weld line occurrence be predicted?
At the beginning, I explained that completely preventing weld lines is not easy, but it is possible to anticipate the possibility of weld lines and take measures to address them. Specifically, let’s start by anticipating the potential occurrence of weld lines.
As mentioned earlier, one of the main factors contributing to weld line formation is the shape of the molded product. Particularly when manufacturing a new product, there is a higher probability of weld line formation if all the resin is injected into the mold at once. Therefore, the key to effective weld line countermeasures is to create short shots at the locations where weld lines may occur to anticipate their occurrence.
The term “short shot” is commonly used to refer to the molding defects of plastic where the mold is not completely filled and a part of the product is missing. However, here it refers to the processing method used with a new mold. Initially, the filling amount is not set to the maximum, but gradually increased while switching to lower holding pressure. This method is effective for understanding the necessary conditions in cases where the manufacturing conditions are unclear.
Using this method, multiple stages of short shots are molded, starting from just before the anticipated location of weld line formation to the position after its occurrence. This allows the flow of resin over time to be visualized and enables further identification of the specific locations where weld lines are formed. By anticipating where weld lines are occurring, it becomes possible to consider suitable countermeasures. Therefore, let’s first anticipate the locations where weld lines may occur.
Methods to Prevent Weld Lines
If weld lines can be reasonably predicted, countermeasures can be implemented. Here I will introduce four main methods to prevent weld lines.
Increasing Resin and Mold Temperatures
The first method is to increase the resin and mold temperatures. Weld lines occur because the heated resin loses heat as it flows through the mold and cools down. Therefore, the resin and mold temperatures are set higher than current settings, keeping the resin flowing for as long as possible without lowering its temperature. Delaying the solidification time of the resin reduces the risk of weld lines forming.
The advantage of this method is that countermeasures can be implemented using the existing mold as-is. Since there is no need to recreate the mold from scratch, this can be considered a relatively easy countermeasure.
However, raising the resin temperature requires applying more heat than before, and increasing the mold temperature necessitates modifications like installing cartridge heaters in the mold. So there is additional cost and labor involved.
Changing the Gate Position
Gate refers to the entrance area where resin flows into the mold. The role of the gate is to “control the speed at which the resin is injected and flow into the mold” and “to adjust the pressure by preventing the resin from flowing back due to the gate solidifying first when the resin is injected.” There are various ways to do this, such as “controlling resin temperature by adjusting the width of the gate and generating frictional heat.” Changing the position of the gate can also be used as a countermeasure against weld lines. Specifically, gates are installed in locations where weld lines are likely to form, and resin can be injected at a high temperature to prevent weld lines from forming. Another measure against weld lines is to install multiple gates instead of just one, to avoid creating countercurrent welds as much as possible.
By the way, gates come in various shapes. Weld lines can be prevented by installing gates appropriately according to the shape of the product and mold. Here we will introduce the main gate shapes.
Direct Gates
Normally there is a runner channel between the mold and gate where resin flows, but direct gates install the gate directly into the mold with no runner. This type of gate is suitable for simple shapes and thick-walled products. However, a downside is that the cut surface area is larger when removing the product from the mold and cutting the gate.
Side Gates
Side gates are installed on the side surface of the mold. They allow multiple gates to be used and are common for many products. Proper placement can help reduce weld lines. However, more gates means more time-consuming gate removal work after molding.
Jump Gates
Like side gates, jump gates involve multiple gates, but instead of the mold side, they are placed on the top or bottom surface. Used when cut marks on the product sides are undesirable. However, they can be more difficult to cut than side gates.
Changing the Mold Design
The final countermeasure is altering the mold design itself to reduce weld lines. Specific methods include:
Eliminating or reducing through-holes
Through-holes in molds allow water, air, oil etc. to control resin cooling and solidification, but can also contribute to weld lines. For weld-prone areas, making holes smaller or removing them entirely slows cooling and reduces weld risks.
Minimizing extreme thickness variations
Extreme differences between thick and thin sections make resin flow favor thick areas, increasing weld lines in thin sections. Measures like adding ribs around thin sections, and gradual transitions from thick to thin, reduce extremes and suppress weld formation.
Changing the mold design takes time and cost, but prevents issues at the source rather than workaround fixes. For high-volume production, it can be an optimal solution for minimizing weld line problems.
Implementing Heat-and-Cool Molding
Heat and cool molding, also known as weldless molding, is a molding method where the surface of the mold is heated to delay the cooling and solidification of the resin, and then rapidly cooled and solidified when the resin merges. This significantly reduces the occurrence of visible weld lines by preventing the formation of a pronounced V-shaped groove at the merging point.
There are two main advantages of heat and cool molding. Firstly, by heating the mold surface, the cooling of the outer part of the resin can be suppressed, allowing for a maintained high-flow state. Secondly, since the resin flows rapidly within the mold, there is no need to apply high pressure to the resin during injection.
As for disadvantages, it is necessary to prepare molds that can withstand rapid temperature changes because the mold surface needs to be heated and then rapidly cooled. Additionally, the longer molding cycle increases energy consumption, leading to potentially higher production costs and an impact on product pricing.
Furthermore, it’s important to note that heat and cool molding does not completely eliminate weld lines, but rather reduces their visibility. Therefore, additional measures are required to address the other drawback of weld lines, which is a potential reduction in strength.
Inspection Method for Weld Lines
The most straightforward method for inspecting weld lines is visual inspection. By comparing the molded product with standard and defect samples, weld lines can be identified. The advantage of this method is that it can be carried out without extensive equipment or machinery, resulting in cost savings.
However, there are several challenges. One significant challenge is the variability in inspection quality due to human involvement, even with the presence of defect samples. Additionally, education costs are incurred as experience and knowledge are required.
In the manufacturing industry, which is often plagued by chronic labor shortages, relying solely on visual inspection that requires securing and developing personnel may be difficult.
Therefore, automation of visual inspection is recommended. Although it requires initial investment compared to visual inspection by humans, it enables consistent quality inspection and allows operation even with a labor shortage. From a long-term perspective, it can be said that there are significant benefits to conducting stable inspections while controlling costs.