Inspection is an important step in the maintenance of machine parts in the mechanical industry. What items need to be checked and how to inspect them?
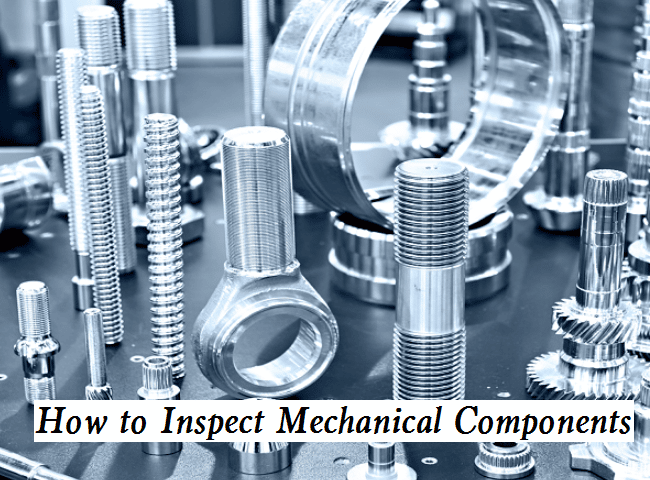
Inspection Items of Mechanical Components
During the quality inspection and maintenance of the machine parts, a lot of characteristics need to be inspected and verified.
1) Geometric accuracy
Geometric accuracy includes dimensional accuracy and shape and position accuracy, but sometimes the maintenance work is not to pursue the geometric size of a single part but to require relative fitting accuracy, which is often an important part of the inspection work. The common form and position accuracy in maintenance include roundness, cylindricity, concentricity, coaxiality, parallelism, and perpendicularity.
2) Surface quality
The inspection of the surface quality of the parts in the maintenance work is not limited to the inspection of the surface finish, but the inspection of the used parts for scratch, burning, galling, and other defects.
3) Mechanical properties
According to the characteristics of mechanical maintenance, in addition to the hardness of the mechanical properties of the part materials, other indicators are generally not checked, but some properties encountered in the process of parts manufacturing and maintenance, such as balance, spring stiffness, etc., cannot be ignored.
4) Hidden defects
During the manufacturing process of parts, there may be original defects such as slag inclusion and cavity inside, and micro-cracks may occur during the use process. These defects cannot be found directly from general observation and measurement, but they may have serious consequences on the machinery. Therefore, during mechanical maintenance, some parts must be comprehensively inspected purposefully.
Inspection Methods of Mechanical Components
There are many methods for part inspection, based on the actual situation of mechanical maintenance, here are some common solutions.
1) Sensory examination
This is a method to identify the technical condition of parts only by the visual sense of the inspector without checking the equipment. This method is simple and convenient, and it is also easy to distinguish the defects of a large number of disassembled and inspected parts in mechanical maintenance. Therefore, this method is still useful. However, this method cannot be used to check parts with high accuracy requirements, and the inspectors are required to have rich experience.
2) Instrument and tool inspection
A lot of inspection work is carried out with instruments and tools. Due to the different working principles and types of instruments and tools, they can be divided into general measuring tools, special measuring tools, mechanical instruments and meters, optical instruments, electronic instruments, etc.
3) Physical inspection
This is a method to detect the technical condition of parts by using the changes caused by the workpiece with electrical, magnetic, optical, acoustic, thermal, and other physical quantities. The realization of this method is also combined with the inspection method of instruments and tools. This method is usually used to check the hidden defects inside the parts without damaging the parts themselves. Now it is generally called nondestructive testing. Nondestructive testing technology is developing day by day in recent years. Now magnetic particle method, penetrant method, ultrasonic method and radiographic method are widely used in production.
How to Ensure the Quality of Part Inspection
1) Strict technical standards
Most mechanical parts and mating parts have specified technical standards, which is the main basis for inspection. If there is no reliable basis to believe that the standards need to be modified, these standards should be strictly followed, and it is never allowed to lower the standards and put unqualified parts into use.
2) Select proper inspection equipment
In addition to selecting inspection equipment according to the nature and scope of inspection items, special attention shall be paid to the requirements of accuracy. For example, when measuring the length, when the accuracy is required to be within 1mm, use a steel ruler; When the required accuracy is within 0.1mm, a vernier caliper is generally used; When the accuracy is required to be 0.01mm, micrometer and dial indicator are required; When the accuracy of 0.001 mm is required, a comparator is required. If the accuracy of the inspection equipment is lower than the required accuracy of the measured object, it is simply unable to meet the quality inspection requirements, and attention must be paid to prevent it.
3) Improve the technical level of the inspection operation
The technical level of inspection operation directly affects inspection accuracy. Whether it is self-inspection by maintenance personnel or inspection by full-time inspectors, the operator is required to master the inspection equipment used and specify the inspection requirements for inspection objects. Therefore, attention should be paid to the improvement of inspection technology, special training should be provided for the use of special and important inspection equipment, and various inspection personnel should be relatively stable.
4) Reduce inspection error
Any inspection result will inevitably have errors, and its impact is multifaceted. Therefore, the following aspects should be prevented and eliminated:
- The inspection equipment has its own accuracy level, which shall be calibrated regularly, and shall be maintained to keep its due accuracy;
- The error caused by temperature shall be corrected. Among the environmental factors that affect inspection accuracy, the influence of temperature is the largest. For example, the influence of linear expansion in length inspection, and the property change caused by temperature change in electronic devices should be corrected in more precise measurements.
- Most of the errors caused by improper operation or inaccurate reading are accidental errors, so the average value of multiple measurements can be taken, which can greatly reduce its error level.
- Establish sound and reasonable inspection rules and regulations.