Product inspections are critical for importers who take securing their supply chain seriously. When to conduct product inspections? What the types of products inspections you might do? Today, we are going to show you some examples of quality inspections in action.
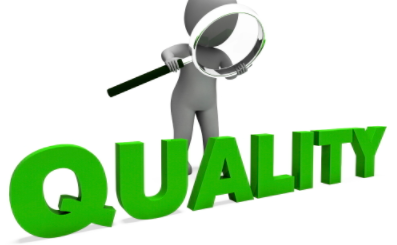
When To Do Product Quality Inspection
Having learned about the different inspection levels and AQL tables, you know how to set the number of samples to check and how many defects can be accepted (if any). With these settings and your detailed product specifications, a QC inspector can check your products and reach a conclusion (passed or failed). But an important question for importers is.
We already know how to set and how many defects can be accepted with these settings and your detailed product specifications ik, you see inspector can go into your supplies factory and check your products and reach a conclusion about whether they pass or fail on quality but an important question that you need to answer is when should I do the product inspections.
Inspections are really important for buyers who want to secure their supply chain. It’s a fact that spending a few hundred dollars on products inspections where we check and fix issues early can really reap a lot of benefits in the future. You could save weeks of delays avoid needing to ship products quickly by air which is expensive and also avoid receiving lower quality products from your suppliers which you’ve then got to either try and sell to your customers, simply can’t sell at all. There are typically four key types of product inspections that occur at different times throughout production.
4 Product Inspections At Different Points Of The Production Process
There are product inspections which catch problems early and those which verify quality before shipment. Big arrow there that is the state of finished production. So first we look at pre-production inspections, these are great for at the start of production, because they help things get off on the right foot, you can check the raw materials and components being used in production. Some sneaky factories might try to swap in cheaper materials or components to increase their margin, while decreasing your quality. This needs to be kept an eye on the inspectors will also be able to see that the operators are following exactly the right processes to create your products at great quality from the get-go.
Next we go on to during production inspection or do pro. This allows you to get a great idea of average product quality quite early on in the production process and a benefit means that you’re able to ask the supplier to correct any issues which are found before they take hold and affect all the products which are being made you can conduct this. As soon as the first finished, products come off the line, but these first few samples might not be representative of the whole order. So usually we say that it’s better to think about doing a do Pro between around 10 to 30 percent of the way through production. In production to the final pre-shipment random inspection or FRA inspecting goods after they’re made impact is the standard QC solution for most importers.
Your inspector will really check every detail including counting total quantity and confirming the packaging is okay. These usually happen really quickly just before shipment to avoid delays. Inspectors usually start after all the products are finished being produced and almost packed, so 80% or more of the shipment is already being packed. Finally, loading supervision, this helps you to make sure that the factory is shipping the right product in the right quantity. With the right loading plan, it could help stop sneaky suppliers from swapping out good products for poor quality ones just before shipment.
Examples of 3 Different Inspection Scenarios
Example 1: you buy 5000 widgets from a new supplier
Let’s have a look at examples of three different inspection scenarios where we can see these inspections in action. Firstly you’re buying 5000 widgets from a new supplier, you don’t know this Factory they’re new. So you need to be cautious and adopt inspection of all. If we refer to the AQR tables based on our purchase number of 5000. We need to select 200 samples to check the inspection fails. If we’ve got one or more critical defects 11 or more major or 15 or more minor defects. Because it’s a new supplier, you might want your inspector to check all the product functions on a few samples. Just to make double sure this test obviously takes a little of time because they’ve got to go into quite detailed checking each sample for that you’ll choose special level s2 and this brings up 8 Pauls out of the 200 that need to be checked 200 samples can roughly be checked by one person in one day. So a third-party QC firm like southeast would quote you on Monday for this job. If it’s a standard product, and you’ve got flexibility with timing.
Example 2: you buy 30,000 watches from an unknown factory
A final pre-shipment random inspection should be great for this order example to you buy 30,000 watches from an unknown factory or factories. The reason we’re talking about unknown factories is that your supplier has given orders to several workshops to produce your goods, but they won’t tell you who. These items are rather valuable per piece, so because of your lack of information, a stricter level three inspection is probably the most appropriate. The AQL tables tell us that we have to inspect 500 out of the 30,000 samples. The maximum number of defects is zero critical twenty one major and twenty one minor out of the five hundred. If a visual check on all samples and a function accuracy check on a few pieces is enough, it probably takes two to three Mondays to conduct this inspection. So when would we inspect your hands are tied here a little because if the supplier refuses to disclose their suppliers’ factory information. You have to inspect the goods at only your supplies premises, that means that you’ll be doing a final random inspection, once they’ve received the finished goods.
Example 3: you buy four different styles of garments from a good factory.
You already know that this factory’s workmanship is quite good, but you want an inspector to check all the conformity elements and in particular the measurements, because their garments. You trust this Factory you know them, so inspection level one should be enough. These products actually go for quite high prices, so your tolerance for defects is low one point five percent for major defects and four percent for minor for garments. Generally no critical defects. Fit is quite important, especially for brassiere and briefs, so three to five samples of each size of those should be measured individually.
There are four different types of products remember, so there should be four different inspections. Based on the different quantities and code letters that we’re seeing in the AQL tables. There are three hundred and seventeen pieces in total including the different types of clothing and 63 of those samples also should be measured individually. It will probably take two inspectors, perhaps three on Monday to do this inspection. In this case, the best time for these garments to be inspected is during production after enough finished products have come off the lines. This means that if any of the garments do have issues were able to work with the supplier to correct them before they produce all the many garments. Because the four products might not be processed at exactly the same time. The inspectors might come at different times to conduct the inspection when the products are being made. If an inspection of garments in this fashion is failed a Rhian spec ssin can probably be performed at the suppliers charge.
There are two types of inspection those that catch problems early and those that verify product quality before shipments. These complement each other quite well. You can start taking quality as early as when just around 5% of the production is complete. The earlier is checked, the more likely major issues can be stopped before they have serious effects on the production run. The final random inspection conducted quickly when production is finished and 80% packed is the most popular product inspection. Although this can be conducted in conjunction with other inspections too.
We’ve come to an end of when to inspect and indeed looked at some of the product inspections which may be useful for you. Hopefully you’re now after seeing all three parts of quality control basics, ready to start seriously conducting QC inspections and getting a very tight control over your quality.