Six Sigma is a quality management tool. Six Sigma management is a process innovation method to improve customer satisfaction and reduce operating costs and cycles.
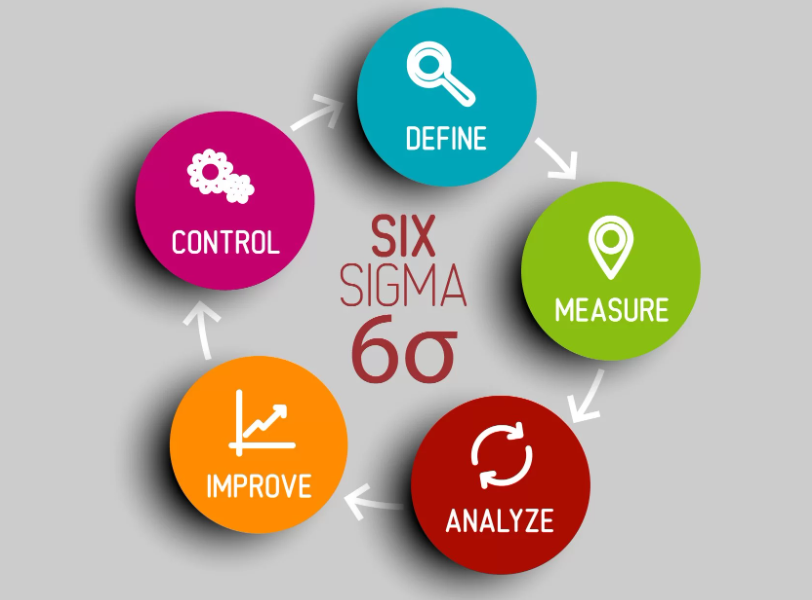
What is Six Sigma – Purposes of Six Sigma
Six Sigma is a concept and corresponding management system developed by Motorola in the 1980s and applied to all aspects of the company, the six sigma management method has evolved into a process and product quality improvement method based on statistical technology, and has evolved into the idea that organizations pursue fine management.
The basic connotation of Six Sigma management is to improve customer satisfaction and reduce the resource cost of the organization. It emphasizes the whole operation of the organization, not just a single product. The quality of service or process emphasizes that the organization should consider quality issues from the customer’s standpoint, adopt scientific methods, and pursue defect-free quality in all areas of operation, so as to greatly reduce the cost of the entire area of organization operation and improve the competitiveness of the organization.
The purpose of organizing and implementing it is to eliminate activities without added value, shorten the production cycle, enhance customer satisfaction, and thus increase profits. Six Sigma management will focus the organization’s attention on both the customer and the organization, which will undoubtedly bring about improvements such as customer satisfaction. Market share increased. The defect rate decreases. Cost reduction. The production cycle is shortened. Improve the return on investment and other performance.
Advantages of Six Sigma
- Improve the ability of enterprise management
Six Sigma management is driven by data and facts. In the past, enterprises’ understanding of management and management theory remained more verbal and written, while Six Sigma turned all this into practical and effective actions. - Saving enterprise operating costs
For enterprises, all defective products are either discarded, need to be reworked, or need to be repaired and replaced at the customer’s site, which will cost the enterprise. The implementation of Six Sigma management saved Honeywell $600 million in cost in 1999. - Increase customer value
The implementation of Six Sigma management can enable enterprises to achieve a virtuous circle from understanding and meeting customer needs to achieving maximum profits: the company first understands and grasps customer needs, and then uses the Six Sigma management principle reduces randomness and error rate, thus improving customer satisfaction. The medical equipment department of General Electric created a new technology after introducing Six Sigma management, which brought about a revolution in medical testing technology. Therefore, the hospital has improved the utilization rate of equipment and reduced the inspection cost. In this way, the company, hospital and patients were satisfied with the results. - Improve service
As six sigma management can be used not only to improve product quality, but also to improve service processes, the level of customer service can be greatly improved. The management team has successfully improved the payment relationship with Wal Mart, its largest customer, reducing bill errors and disputes by 98%, which not only speeds up the payment, but also harmonizes the mutually beneficial cooperation between the two sides. - Form a positive corporate culture
Under the traditional management mode, people often feel at a loss, do not know their goals, and work in a passive state. Through Implementation Six Sigma management, everyone knows what they should do and how to do it. The whole enterprise is full of enthusiasm and efficiency. Employees attach great importance to quality and customer requirements, and strive to do the best. Through training, they master standardized and standardized problem solving methods, and their work efficiency has been significantly improved. With strong management support, employees can concentrate on their work and reduce and eliminate fire fighting activities.