Analyzing the differences between TQM and Lean Six Sigma, TQM is a process developed after the quality inspection phase and the statistical quality control phase (SQC) that emphasizes the involvement of all employees in focusing on the generation, formation, and realization of all quality. Lean Six Sigma is built on many of the commonly used statistical process control tools and TQM. It enhances the process through more demanding statistical analysis and by providing more rigorous problem-solving (DMAIC).
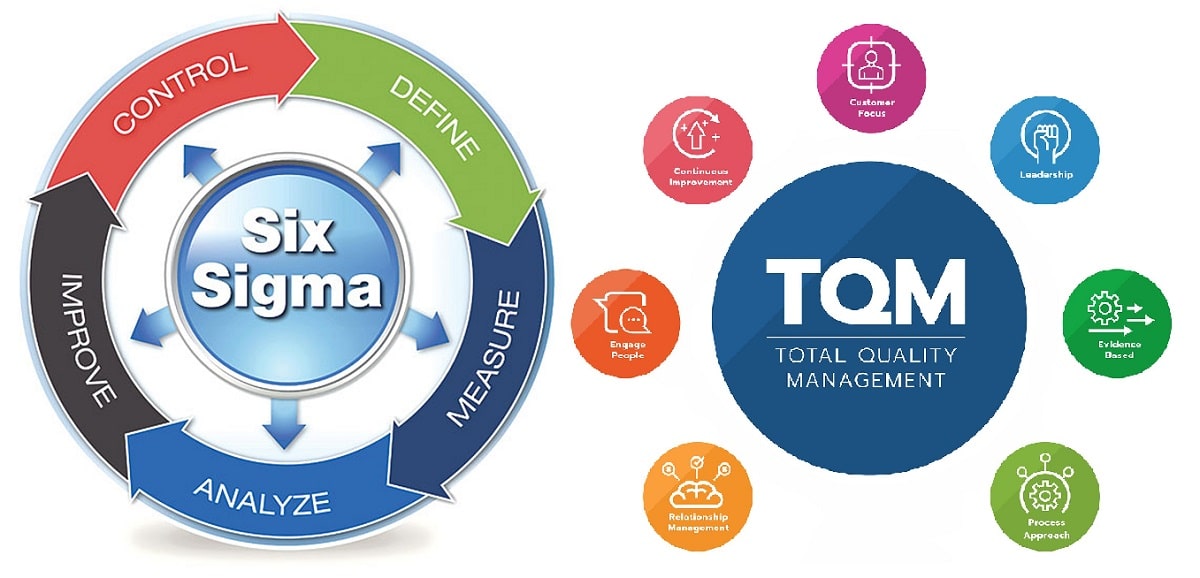
What is TQM (Total Quality Management)?
TQM, a strategy to focus the entire organization on continuous improvement, arose in the 1980s in response to Japanese competition (and the work of W. Edwards Deming) and became popular through the early 1990s. Six Sigma began at Motorola and gained popularity in the mid-1990s, largely because of the visible efforts of GE. Its goal was to improve the company’s quality to only three defects per million by systematically making incremental changes to processes and carefully measuring the results statistically.
What is Six Sigma?
Six Sigma is similar in concept to TQM, focusing on problem-solving techniques and using statistical methods to improve processes. Six Sigma emphasizes the importance of measurement because only data does not lie and is the real truth. To do this, Six Sigma uses techniques and concepts such as probability theory, statistics, and operations research. It instills a culture of “statistical thinking” and “objective (or data-based) decision-making” within the organization. But while TQM emphasizes organization-wide employee involvement, the Six Sigma approach is to develop experts (known as Green Belts and Black Belts [1]) who work on important issues and who teach others in the company as well.
Differences between TQM and Lean Six Sigma
There are many similarities between TQM and Lean Six Sigma, after all, Lean Six Sigma, as a latecomer, learned a lot from TQM. The difference between Lean Six Sigma and TQM is the introduction of statistics and data analysis, which no one dares to underestimate today with the popularity of “big data”. But there still some differences between the two quality management methodologies.
1. Organizational Culture
In the past, corporate culture was often limited to the investment and payment of bosses and employees, and customers could only passively accept the output. In today’s highly competitive business world, the voice of the customer is gradually being taken seriously, and the process management of products and services has led to changes in organizational structure and corporate culture. Lean Six Sigma uses process reengineering and project management to improve the response speed to customers and drive the organization to efficiently break through bottlenecks to obtain ten times faster improvement. Rather than focusing on qualitative theoretical elaboration, it focuses on an action-oriented approach, with cross-functional teams and a clear division of labor, in a standardized and systematic methodology. Combined with a financial and direct and effective incentive system, Lean Six Sigma is more embedded in the corporate culture of organizational change. The implementation of TQM in the name of the system and the Lean Six Sigma program in the name of the program are mutually enriching, creating greater organizational resilience and differentiated competitive advantage.
2. The Main Focus Of The Process Is Different
Although this TQM has the modifier “comprehensive,” many of its quality initiatives are centered on production or manufacturing processes, with little attention to service, logistics, marketing, and other equally important aspects. Lean Six Sigma pays attention to all business processes, and it is effective not only in manufacturing processes, but also in service and transportation processes, where it can generate more opportunities. Therefore, Lean Six Sigma management is more “comprehensive” than TOM.
3. Problem Solving Tools and Education Training
Although the education and training required for Lean Six Sigma is more complex than TQM, the most important refinement in human resource education for Lean Six Sigma, compared to TQM, should be the mutual growth of Black Belts and Green Belts through coaching and implementation, under the premise of achieving project improvement, to train future leaders for the company. On the other hand, TQM is generally a departmental training, and the effect is often not ideal, while Lean Six Sigma elite training for Black Belts and Green Belts from the top down has outstanding effect.
4. Project Promotion
TQM and Lean Six Sigma both have projects that emphasize project improvement activities, but TQM is driven by the quality control department, with related personnel working part-time to conduct quality management team activities (QCC), and its improvement projects mostly focus on quality aspects. Lean Six Sigma, on the other hand, uses the DMAIC improvement model, with full-time black belts and part-time advocates and green belts, and Lean Six Sigma management, which prioritizes solving key problems and optimizing core processes, leading to breakthrough improvements. A system that achieves and sustains successful business management by paying close attention to customers, process management, process improvement and the judicious use of data and its facts. Six Sigma emphasizes customer-driven, outside-in customer standards as the true standard. While QC team activities, although they may also lead to breakthrough improvements, they emphasize “small” topics when selecting topics, starting with small problems and things around them, and solving more problems within the scope of QC team members.
5. Different Levels Of Leadership Attention
In all companies where TQM has been successful, the enthusiastic involvement of management can be seen. More commonly, however, senior company management was not enthusiastic about the implementation of TQM. In all companies implementing Lean Six Sigma, there is no doubt that senior leaders have confidence and enthusiasm for Lean Six Sigma, and along with this enthusiasm comes a relentless effort to implement Lean Six Sigma. Leaders recognize that Lean Six Sigma is synonymous with business renewal, and that continuous change is essential to the survival of the business and to its continued success.