What is the main objective of a business project? Indeed, several answers to this question are possible and they may all be valid. A point common to these objectives is of course the final satisfaction of the customer. In other words, the more satisfied your client is, the more your objectives will have been achieved and your project will be a sign of success. But how do you go about achieving these goals? Based on our experience here at IPQCCO.COM, in order for a customer to be satisfied, the strategy is to have a clear process in place as part of an overall project quality management program.
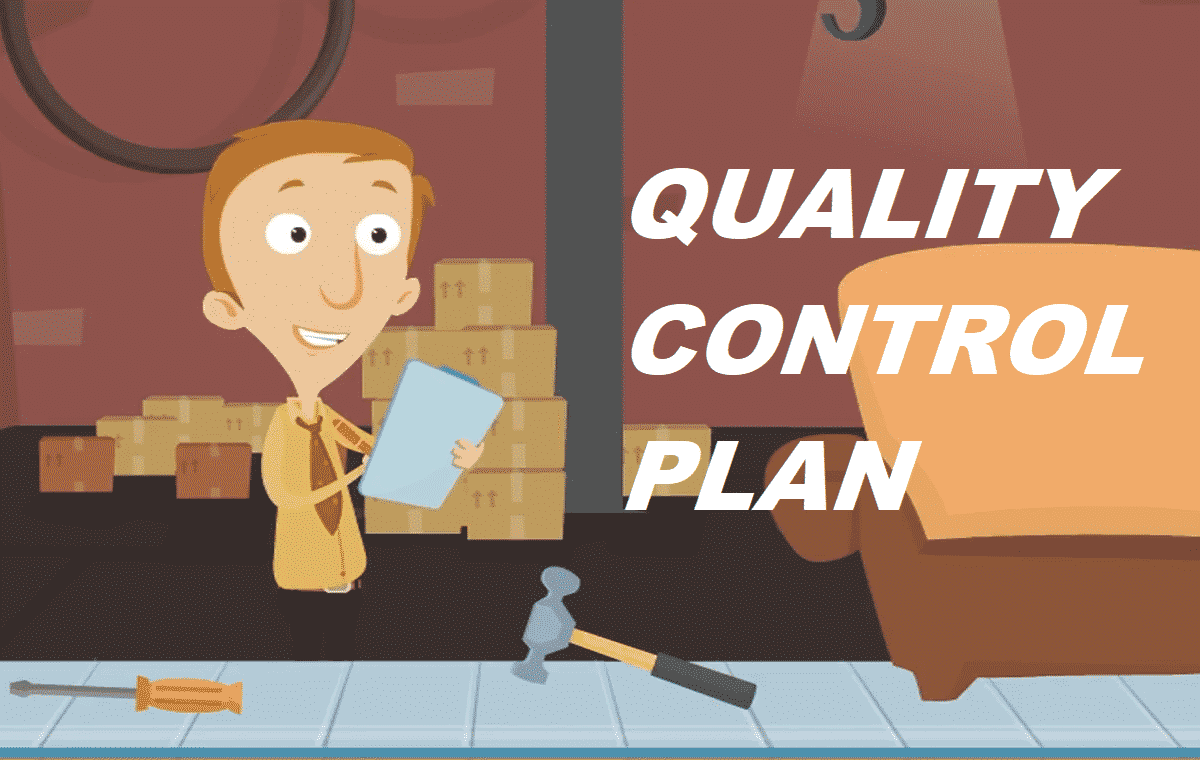
QCP allows the client to be confident in the delivery of the expected results. In other words, it is a formal program where the method will be described, planned as well as the activities carried out to meet the client’s expectations. On your side, the QCP will allow you to be able to manage when you are in the execution phase and to deliver the expected level of quality.
What is Quality Control Plan (QCP)?
The quality control plan will include the processes and techniques that you will employ to meet the quality requirements. When you are in the process of developing the program; most of the time, the quality requirements and associated criteria are not yet known.
Quality Control Plan Essential Factors
In summary, the essential ingredients for the QCP: Find out about the quality requirements – Generally speaking, this is the process that you will use to find out how the client will assess the quality of the results you have presented to them.
- Define quality standards
Establish and announce the quality standards that you will follow when carrying out the project.
- Define the people in charge of the process
What functions need to be formalized to meet the quality criteria? You will need to describe them and determine the tasks related to their responsibility. You’re right, the project manager is responsible for the overall results, but depending on the size of the project, quality support may be designated. This area includes controllers, auditors, third-party control specialists, etc.
- Define the Criteria for Completeness and Accuracy
We are sure you’ll agree if we tell you that the best way to satisfy the customer is to ASK them what would make them happy and how they would like things to happen. be done. Working upstream with the client to define the keys to success is essential and even crucial for a profitable long-term relationship. Once you have done that, all you have to do is make those words a reality and surpass yourself. This approach is called “give them what they want, then sell them what they need”. You will tell me it goes without saying, but please avoid incomplete deliveries.
- How can you ensure consistent quality?
In order for the customer to be sure of consistent quality, you will need to disclose your quality assurance (QA) processes. Even if this or these process (s) are carried out by third parties, you are advised to present and define the main QA activities as well as the techniques employed.
What tools will you use to measure quality? – This is where you will need to list and specify the tools you will use throughout the project lifecycles.
- How will we control the quality?
This is where you will need to explain the process of implementing a quality control process and the related activities. The activities of the QC process should be carried out continuously throughout the project. Here, too, you can learn more about the specific activities and techniques used for quality control.
To conclude, the quality management program is an integral part of the success of your business not only for satisfying your customer but for your future. However, it is important to recognize that the workload is substantial. However, good construction project managers are always on the lookout for tools that can help them optimize the workflow without compromising quality.