The first article inspection may be performed in different ways according to the products and requirements. What are the different types of first article inspection? We’ll also talk about the differences between FAI and PPAP.
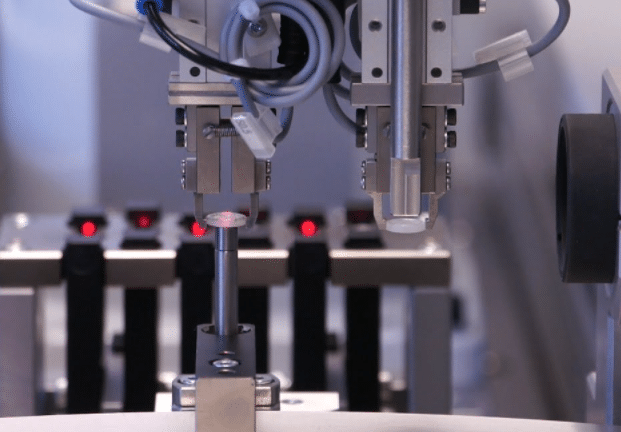
What are the Types of First Article Inspections?
First Article Inspection (FAI) is a critical process in manufacturing that verifies the initial samples of a new product or component. The purpose of an FAI is to ensure that the product or component meets all the specified requirements before mass production begins. There are three types of First Article Inspection (FAI).
- Full FAI: This is the most comprehensive type of FAI, where the entire product or component is inspected in detail. A full FAI is typically required when a new product is introduced or when there are significant changes made to an existing product. This type of inspection includes a complete review of the design, manufacturing process, and all related documentation.
- Partial FAI: A partial FAI is used when only specific characteristics of a product or component need to be inspected. This type of inspection is typically used when there are minor changes to an existing product, or when a product has been produced previously and the manufacturing process is well-established.
- Verification FAI: A verification FAI is performed to ensure that any changes made to a product or component during its production cycle do not affect the product’s original design or performance. This type of inspection is typically performed on components that have been produced previously, and the changes made to the component are minimal.
What is Production Part Approval Process?
The Production Part Approval Process (PPAP) is a quality control process used in the manufacturing industry to ensure that parts or components produced by a supplier meet the design and specification requirements of the customer. PPAP is typically used in the automotive industry but is also used in other industries that require stringent quality control processes. The purpose of PPAP is to provide evidence that the production process is capable of consistently producing parts or components that meet all the design and specification requirements. This evidence is documented and shared with the customer as a way of demonstrating that the supplier is capable of producing high-quality parts or components on a consistent basis.
The PPAP process typically includes the following steps:
- Initial Sample Inspection: The supplier produces an initial sample of the part or component and submits it to the customer for inspection.
- Document Review: The supplier provides the customer with detailed documentation on the manufacturing process, including process flow diagrams, control plans, and inspection procedures.
- Dimensional Inspection: The supplier measures the part or component to ensure that it meets all the required dimensions and tolerances.
- Material Testing: The supplier tests the material used to produce the part or component to ensure that it meets the specified requirements.
- Performance Testing: The supplier tests the part or component to ensure that it meets the required performance specifications.
- Submission of PPAP Documents: The supplier compiles all the documentation and test results and submits them to the customer as part of the PPAP submission.
- Approval and Ongoing Monitoring: The customer reviews the PPAP submission and either approves the production process or requests additional testing or changes. Once approved, the supplier is required to monitor the production process and provide ongoing PPAP submissions to demonstrate that the process remains capable of producing high-quality parts or components.
Differences Between FAI and PPAP – First Article Inspection vs PPAP
First Article Inspection (FAI) and Production Part Approval Process (PPAP) are two quality control processes used in manufacturing. While both processes serve a similar purpose, there are some key differences between FAI and PPAP.
- Timing: FAI is performed before the start of production, while PPAP is performed during production. FAI is typically done on the initial production run of a new part or product, while PPAP is done on a regular basis during production runs to ensure that the process remains stable.
- Purpose: The purpose of FAI is to verify that a new part or product meets all of the design and specification requirements before production begins. The purpose of PPAP is to ensure that the production process is capable of consistently producing parts or products that meet all of the design and specification requirements.
- Scope: FAI typically involves a comprehensive review of the design, manufacturing process, and related documentation, while PPAP is typically limited to the review of specific production processes, parts, or components.
- Documentation: The documentation required for FAI and PPAP is different. FAI typically involves the completion of an FAI form, while PPAP requires the completion of a PPAP submission that includes more detailed documentation on the production process and quality control methods.
- Applications: FAI is commonly used in the aerospace and defense industries, while PPAP is more commonly used in the automotive industry.