Welding technology using ultrasonic waves is highly safe because it does not use heat, and is widely applied to food, hygiene, metals, and resin processing. However, there are several elements to welding, and if you do not know the principle, you may not be able to achieve the desired effect.
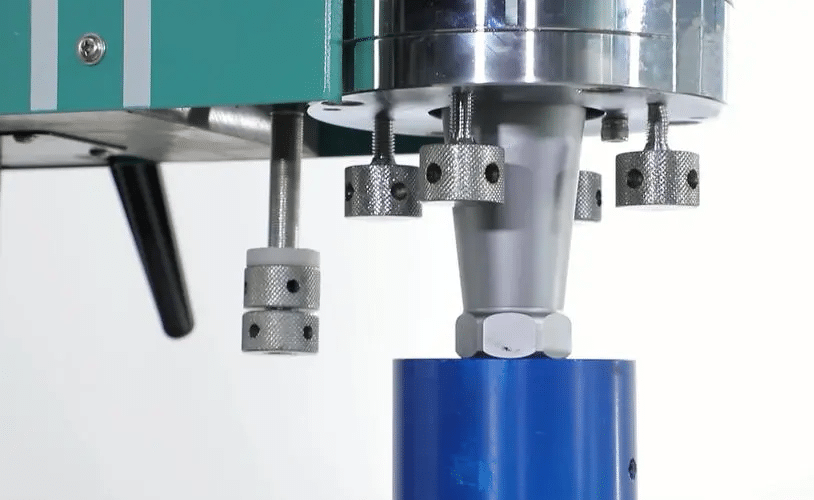
In this post, we focused on ultrasonic welding and summarized its features, safety, and case studies.
1. What is the mechanism of ultrasonic welding? Simple and fire-free and safe welding principle
Ultrasonic welding is a simple mechanism and is very safe because it does not use fire. In addition, the bonding strength is high, and the time required for joining is almost instantaneous.
(1) Mechanism of ultrasonic welding
Ultrasonic welding is a simple mechanism that applies very fine vibrations (about 40,000 times per second at 40 kHz) and heats the joint surface to weld it.
For example, two plates are put together and an ultrasonic welding machine is pressed against the top to provide ultrasonic vibration. Vibrations are transmitted to the material, and vibrations are also generated in the other material that is combined. Vibration creates frictional heat between the two materials, which causes them to melt and mix, causing them to stick together.
(2) Ultrasonic welding can be used for a wide range of materials
Ultrasonic welding can be used for a wide range of materials that are deformed by heat. For example, plastics, metals, and textile products. Since there is no contamination of foreign substances such as fasteners and adhesives during welding, it is also widely used in food packs. Nonwoven masks are also actually ultrasonically welded. Since it can be welded quite sturdily and is highly safe, it is used in a wide range of applications.
2. What are the characteristics and disadvantages of ultrasonic welding? Points to note when actually welding
Ultrasonic welding machines have a wide range of applications due to their simple and safe mechanism. While there are many advantages, of course there are also disadvantages. By keeping the features down, it is possible to introduce it more effectively.
(1) Advantages of ultrasonic welding
There are several advantages of ultrasonic welding, including the following:
- Compatible with a wide range of materials that deform due to heat
- Continuous welding is possible
- More welding points can be added and welded at the same time
- Short welding time enables speedy work
- Economical with no consumable parts or materials
- The device is relatively small and does not take up much space
- Welding is possible even if the surface is dirty without foreign matter contamination
As mentioned above, there are many advantages and high safety, so the number of introduction cases is increasing. Another advantage is that the welding time is fast, and it is easy to improve productivity when introduced.
(2) Disadvantages and problems of ultrasonic welding
Ultrasonic welding machines have many advantages and will not seem to have many drawbacks. However, there are not a few disadvantages, specifically the following three points.
- Difficult to weld large parts
- Not good at objects with complex or irregular shapes
- Difficult to weld three-dimensional shapes
In ultrasonic welding, if the target material is large, it is necessary to increase the vibration (lower the frequency). However, if the vibration is made too large, the impact on the part itself will also increase. Care must be taken if the material is large, as there is a risk of scratches on the parts.
In addition, it is not suitable for materials with complicated shapes that do not easily generate frictional heat between materials. Even with a three-dimensional shape, there will be places where constant pressure cannot be applied, so it is better to think of other means.
(3) Precautions for actual use
Ultrasonic welding can be done without using a lot of heat, but depending on the applied pressure and temperature, it may not have sufficient bonding strength.
- Welding time (Time to apply vibration)
- Frequency (how many kHz)
- pressure (how much pressure is applied to the material)
Since the welding strength changes depending on the combination of the above three, it is necessary to set an appropriate value for management. As I explained earlier, if the frequency is too low, the material will vibrate too much. If the pressure is too high, the material itself may deform.
3. Introducing 3 introduction examples that have improved by actually using ultrasonic welding
To see how ultrasonic welding has actually been used and how it has improved, take a look at case studies. We will introduce three examples of this introduction, so please refer to them.
(1) Introducing it to the welding of automobile parts to improve production efficiency
Automotive parts are often made from a combination of many resins. Therefore, the welding quality must be of a fairly high standard.
For example, tightness is important for some parts, while others require machining at precise dimensional levels. Some parts require strength, while others require clean processing.
If these processes take too long, the production volume will plateau, but ultrasonic welding can solve all problems. In fact, there are many cases where the use of ultrasonic welding has dramatically increased production volume.
(2) Achieving both airtightness and safety in food preservation
Packaging in the processing and preservation of food is a very delicate issue. While airtightness is essential from the viewpoint of flavor and shelf life, safety is also required. However, adhesives cannot be used because there is a risk of contamination with foreign matter. Ultrasonic welding is also useful in these cases.
Especially commonly used are tea bags, capsule-type condiments and food packaging. Pouch containers and zippers are also often used to wrap paper cartons and cups because they can be safely enclosed.
(3) Ideal for processing non-woven fabrics
Nonwoven fabrics are not only masks, but are also a general material used in the manufacture of diapers, women’s products, and nursing care products. Therefore, the processing of non-woven fabrics is often required to be hygienic. In addition, many products are rubbed or pulled every time a person moves, so it is necessary to use a processing method that maintains strength.
With ultrasonic welding, both requirements can be met. Depending on the equipment to be introduced, in some cases, embossing and cutting can be done at the same time.
One plant saw a higher level of quality and productivity efficiency gains as a result of implementation.