Screw thread is a fastening connection structure widely used in the industrial field. In military products, the majority connections are completed through threaded parts. Whether the thread is qualified directly affects the assembly performance and safety.
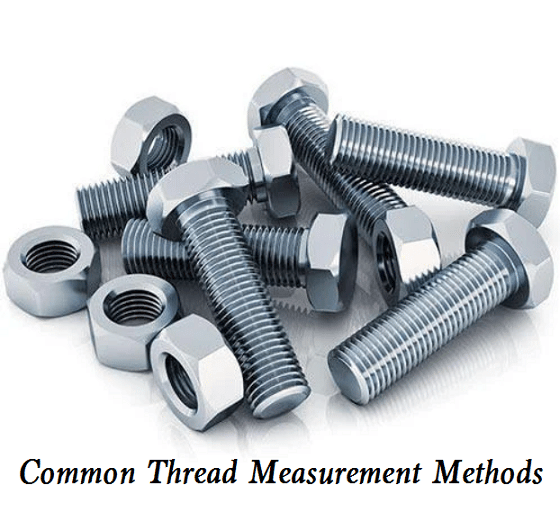
Common Thread Measurement Methods
In the measurement of thread parameters, according to the measuring equipment, the measurement methods of threads can be divided into the following categories.
1) Go/no-go gauge inspection
The traditional go/no-go gauge inspection method can only meet the minimum inspection requirements in thread inspection. The advantages of this test method are fast, economical, and practical. For enterprises with high production technology levels, the use of qualified thread-forming tools and special thread processing equipment (such as thread taps, dies, thread rolling machines, thread rolling machines, etc.) can better control the quality level of threads. The main disadvantage of this inspection method is that it can only qualitatively check whether the pitch diameter of the thread is qualified. It can only know whether the pitch diameter of the thread is between the minimum single pitch diameter and the maximum active pitch diameter. It is impossible to know the specific value of the thread size. The parameters such as half angle error, pitch error, and various shape errors cannot be controlled quantitatively separately.
2) Thread micrometer
The thread micrometer belongs to a special screw micrometer. The thread micrometer has a special measuring head. The shape of the measuring head is made to match the thread profile, that is, one is a V-shaped measuring head, which is consistent with the convex part of the thread profile, and the other is a conical measuring head, which is consistent with the tooth profile groove. The micrometer has a set of interchangeable measuring heads, and each pair of measuring heads can only be used to measure threads within a certain range of pitch. According to the technical indicators of the thread micrometer, the maximum comprehensive error is ± 0.028mm. Because the probe has a certain angle error, and the thread pitch and flank angle of the external thread of the workpiece also have a large error, the measurement uncertainty of the middle diameter can reach 0.10mm when using the absolute method. This method is used to measure the pitch diameter of external thread of workpieces with low precision requirements.
3) Three wire
Three wire method uses a group of three measuring wires with the same determined diameter, and the pitch diameter of the thread is measured indirectly. By putting three measuring needles into the tooth sockets on both sides of the thread and measuring the overall outer diameter with a lever micrometer, the single pitch diameter of the thread is calculated through the functional relationship between the pitch diameter of the thread and the diameter of the measuring needle, the tooth angle and the pitch. In order to simplify the calculation process, a measuring needle with appropriate diameter shall be selected.
4) Comprehensive measuring instrument
The high-precision thread comprehensive measuring instrument adopts the contact thread measuring method. Compared with the traditional measuring method and non-contact measuring method, it has great advantages and feasibility. It has the advantages of high accuracy, convenient use, and strong functions. It has great reference value for thread measurement.
5) Imaging method
The commonly used testing equipment for measuring screw threads by image method are projectors and universal tool microscopes. The projectors measure various parameters of studs by visual positioning and coordinate translation through magnified contours of the measured parts. Because of the visual boundary alignment and the limitations of the projection method in measuring the pitch diameter of the screw threads, the accuracy of the projection method is generally very rough. The universal tool microscope uses the optical system to project the thread profile into the eyepiece field of view, and uses the grating ruler to translate, which can be used to check various thread parameters. Especially, the lens deflection can effectively solve the problem of helix angle, and has high measurement accuracy for threads.
6) Laser triangulation
Laser triangulation, as another nondestructive testing method, has received extensive attention. Based on the triangulation principle of traditional optics, the data point set of the axial profile of the thread surface is obtained, and then the parameters of the thread are calculated. This measurement method has the characteristics of non-contact, high precision, easy control, and can also be applied to the high-speed measurement of small size. However, this method is affected by the environmental temperature and the surface characteristics of the measured object, and the influencing factors should be taken into account in the later data image processing.
7) CMM measurement
CMMs are widely used in the measurement of boxes, racks, gears, cams, worm gears, worms, blades, curves, surfaces, etc. in machinery, automobile, aviation, military, mold and other industries. Through the reconstruction of CMM, there are many methods to measure thread parameters. However, CMM is a widely used general equipment, which lacks probes for thread measurement, and requires customized probe heads for small size threads. The software development is also restricted by the software platform of CMM itself, so it is difficult to customize the contour following control system for thread geometry. And its cost is much higher than that of special thread measuring equipment.
8) Stylus scanning thread profile measuring instrument
The stylus scanning thread profiler continuously scans and measures the upper and lower profile surfaces of the axial profile of the thread, and then calculates the pitch diameter, major diameter, minor diameter, pitch, tooth half angle, taper, and other parameters of the thread according to the obtained profile information.