As high-precision measuring equipment, the measurement error problem of CMM has always existed. In order to further improve the application value of the equipment, relevant scholars have proposed corresponding compensation methods for various errors of CMM inspection, so as to eliminate various errors as much as possible and obtain accurate results.
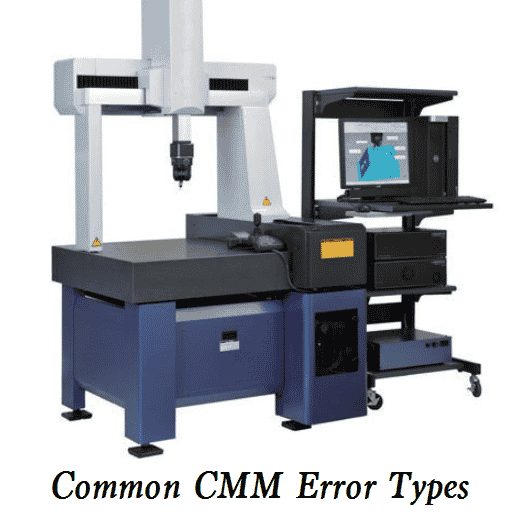
Common CMM Error Types
On the basis of relevant theories, the error types of CMM can be divided into two categories, static error, and dynamic error. The characteristic of static error is that its error value will always remain at a stable level, while the dynamic error will increase with the growth of existence time. Therefore, in terms of error compensation, we should first understand the two errors and then choose the corresponding method. The following will introduce the causes of the static error and dynamic error of CMM.
1) Static error. The static error of CMM is generally caused by the instantaneous influence of external factors on the equipment structure. The error caused by such influence is not easy to change because the influence is transient, but this performance does not mean that the influence of static error is small, because the error value of static error is usually greater than the initial value of dynamic error, Even the dynamic error cannot exceed the static error value after a period of development, so we should pay attention to the static error. For example, in the measurement of the coordinate measuring machine, the probe and probe are worn, and then a static error will be formed.
2) Dynamic error. There are many reasons for the dynamic error of CMM, such as temperature, dust, labor, and other external factors. In most cases, this kind of error will increase the error value with the extension of time, but in special cases, it will show unstable dynamic performance. For example, in CMM measurement, the surrounding temperature and dust will increase with time, and the corresponding measurement error value will also increase, which is the conventional expression of dynamic error; Under artificial factors, due to the characteristics of artificial instability, the measurement speed of its incoming point will be unbalanced, but the specific performance can not be predicted, thus forming an unstable dynamic error performance.
In addition, from the comprehensive perspective of static error and dynamic error, although the static error itself will not change due to time growth, it will show dynamic performance under other factors. For example, the wear phenomenon of probe and probe will become more and more serious in the long-term application, which is a kind of dynamic performance. For this phenomenon, it will affect the calculation based on the current static error value in error compensation, To ensure the accuracy of calculation results.
Error Compensation Methods of CMM
According to the relevant theories, there are three main error compensation methods for CMM, namely, temperature compensation method, software correction compensation method, and measurement force error compensation method, which will be analyzed below.
Temperature compensation
Temperature is an important factor causing CMM error, and under this condition, static error and dynamic error may exist at the same time, so using the temperature compensation method in measurement is an important measure to eliminate measurement error. Among the relevant theories, the temperature compensation method is divided into three parts, namely, structural parameter calibration under standard temperature, real-time temperature acquisition, and error coefficient compensation. The specific contents of the three steps will be analyzed below.
1) Calibration of structural parameters at standard temperature. Among the static errors caused by temperature, it is necessary to confirm the minimum error parameters of the equipment under normal temperature conditions, that is, the parameter values of all structures of the CMM before it is not affected by temperature. After confirmation, a standard comparison parameter set can be obtained, which is mainly used for the subsequent error value comparison.
2) Real-time temperature acquisition. After completing the calibration of the above parameters, it is necessary to calibrate the CMM that currently has a temperature error. Carry out actual measurement and acquisition according to each parameter item in the calibration parameter set to obtain the current parameter set of the equipment. Then compare the calibration results of the parameters with the actual acquisition results to obtain the gap between the current CMM error and the standard parameters for subsequent compensation and adjustment.
3) Error coefficient compensation. According to the comparison results of the above temperature real-time acquisition and calibration parameters, the temperature thermal deformation error formula can be used for compensation. In the compensation process, the ratio of the actual error of the CMM obtained by comparison to the parameter error should be substituted into the formula, and the equipment parameters can be adjusted to the level consistent with the calibration parameters through numerical compensation.
In addition, from the above analysis, it can be seen that the application of the temperature compensation method is relatively complex and requires many comparisons. In order to ensure the smooth application of this method, it is recommended to use simulation software to simulate the calibration parameter equipment and error equipment, so as to obtain two models. With the help of the intuition of the model, the calculation process can be simplified.
Software correction compensation
The software correction compensation method is a method to compensate for the dynamic error of CMM, which is very common in practical applications. In the specific application, it can be seen from the temperature, environment, and manual analysis results of the above dynamic errors that the dynamic errors can be divided into two types, which are called real-time dynamic errors and non-real-time dynamic errors. For the real-time dynamic errors, in the software correction and compensation method, the on-site error data can be directly adjusted to make it consistent with the standard parameters; For non-real-time errors, the current error coefficient of the equipment is obtained by using the acquisition system and then combined with the standard coefficient for correction.
Measuring force error compensation
In the application of CMM, if the measuring force is abnormal, it is easy to lead to the bending of the sidebar and the corresponding error phenomenon. This kind of error belongs to non-real-time dynamic error. For this kind of error, in addition to the software correction and compensation method mentioned above, the measuring force error compensation method can also be used for adjustment. In the specific application, firstly, the simulation software (or other modeling software) is used to establish the structural model of the probe and measuring rod of the CMM. Secondly, the current measuring force is input into the model to see whether the measuring rod is bent and the degree of bending. If there is bending, the measuring force in the model is reduced until the measuring rod is not bent and meets the measurement demand position, Finally, the force parameters measured by the model can be input into the CMM to achieve the desired effect.