In the dynamic world of quality control, businesses face a critical decision: Should they embrace the meticulousness of 100% inspection or opt for the efficiency of sampling? It’s a choice that can significantly impact product integrity, operational costs, and customer satisfaction. As organizations strive to strike the delicate balance between accuracy and expediency, understanding the trade-offs between these approaches becomes paramount. In this article, we delve into the intriguing realm of quality control, exploring the advantages, disadvantages, and the intricate trade-offs involved in the age-old debate of 100% inspection versus sampling. Buckle up as we embark on a journey through the realms of precision and efficiency, revealing the path to achieving optimal quality assurance strategies.
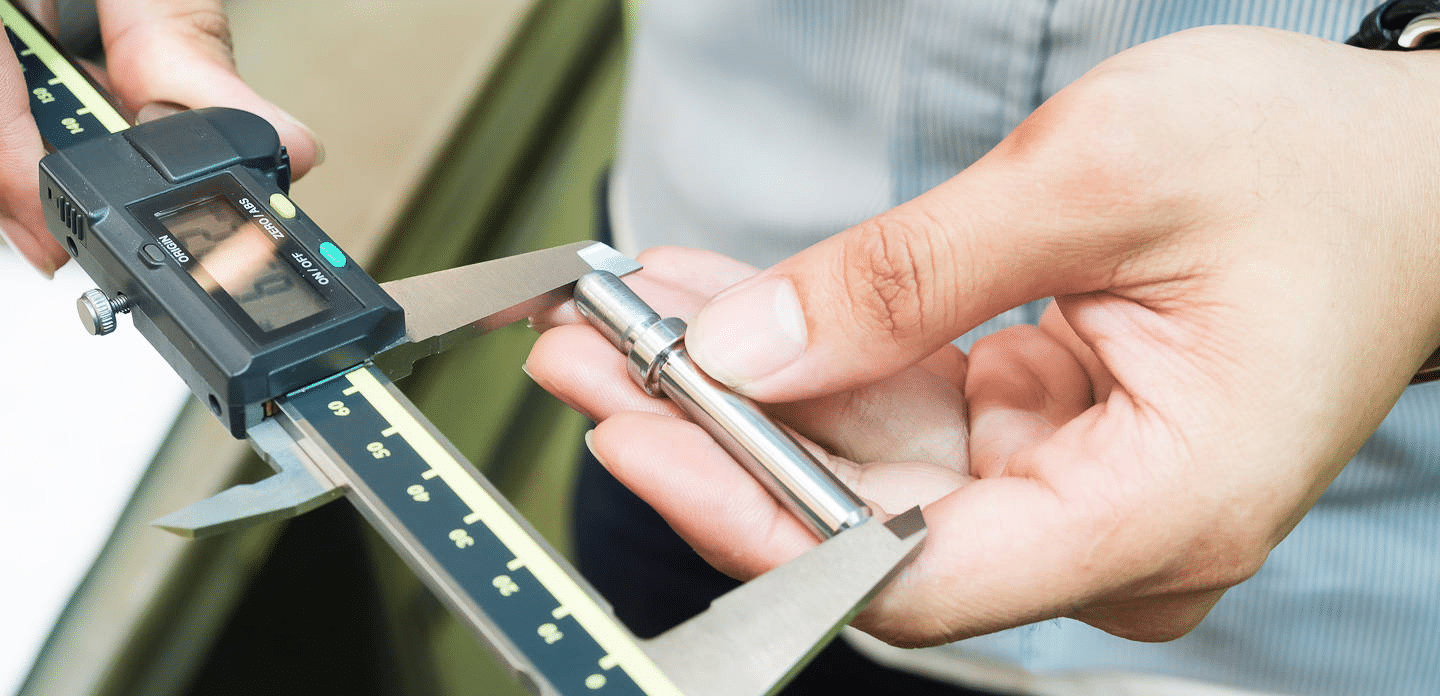
The Case for 100 Percent Inspection:
One approach to ensuring product quality is conducting a comprehensive examination of every individual item, known as 100 percent inspection. This method offers the following advantages:
- Maximum Quality Assurance: With 100 percent inspection, there is a higher likelihood of identifying and addressing all defects, deviations, or non-conformities. This meticulous scrutiny can lead to enhanced overall product quality and customer satisfaction.
- Risk Mitigation: By inspecting every single item, businesses can minimize the risk of faulty or defective products reaching the market. This reduces the chances of product recalls, returns, and potential damage to the brand’s reputation.
The Trade-offs of 100 Percent Inspection:
While 100 percent inspection provides comprehensive quality control, it also carries certain trade-offs that organizations must carefully evaluate:
- Cost and Time Constraints: Conducting a full inspection for every product can be a time-consuming and resource-intensive process, resulting in increased costs. It requires significant manpower, infrastructure, and equipment to execute efficiently.
- Reduced Throughput: The time-consuming nature of 100 percent inspection can limit the overall production capacity. Slower throughput can impact manufacturing timelines, especially for organizations working with large volumes or time-sensitive projects.
Sampling as an Alternative:
Sampling is a statistical technique that involves inspecting a subset of items from a larger batch. This approach aims to estimate the quality of the entire batch based on the analysis of a representative sample. The advantages of sampling include:
- Cost Efficiency: Sampling can significantly reduce inspection costs, as it requires fewer resources and less time compared to 100 percent inspection. It allows organizations to allocate their resources more effectively, potentially leading to cost savings.
- Improved Efficiency: Sampling offers a faster inspection process, enabling organizations to maintain higher production rates. This can be particularly advantageous for businesses dealing with time-sensitive orders or tight deadlines.
The Trade-offs of Sampling:
While sampling offers certain advantages, it also presents some trade-offs that businesses need to be aware of:
- Risk of Undetected Defects: Sampling inherently carries the risk of missing defective items. Although statistical techniques aim to ensure representative sampling, there is always a possibility that some defective units may go undetected, potentially compromising overall product quality.
- Variability in Inspection Quality: Depending on the proficiency and consistency of inspectors, there may be variations in the thoroughness and accuracy of inspections across different sampling batches. This can introduce inconsistencies in the quality control process.
Striking the Right Balance:
Choosing between 100 percent inspection and sampling requires careful consideration of the specific needs, industry requirements, and resources of each organization. Often, a hybrid approach that combines both methods can offer an effective compromise. This might involve conducting 100 percent inspection for critical components or high-risk areas, while utilizing sampling for less critical or high-volume items.
The decision to implement 100 percent inspection or sampling is a complex one, involving trade-offs between quality assurance, cost efficiency, and production throughput. Businesses must evaluate their priorities, resources, and risk tolerance to find the optimal balance. Ultimately, organizations that invest in robust quality management systems, continuous process improvement, and employee training can mitigate risks associated with both inspection approaches, ensuring high-quality products that meet customer expectations.