Various measuring instruments are used for CNC machine tools to check whether the workpiece before machining is installed accurately and to measure whether the workpiece after machining is cut to a specified size. Reliable dimensional measurement can be said to be the starting point of CNC manufacturing. Even with expensive machine tools, precision machining is not possible without “measuring” technology!
In this article, we will easily introduce measuring instruments used in actual metalworking sites, such as analog “dial gauges” that are measured by hand and “3D measuring machines” equipped with sensors.
What is Dimension Measurement?
A measuring instrument is a device or machine that measures the dimensions of an object, and it can be said that it is one of the displacement meters because it can measure the amount of movement of the object.
This includes calipers and micrometers that are measured by hand, but recently machines that can automatically measure dimensions and do not require tools are also sold. Some models use machines to reduce human measurement errors and measure places that cannot be measured by calipers or micrometers. The principle varies greatly depending on the machine and must be selected according to the application.
Since the numerical variation increases while using the measuring instrument itself, periodic correction using a more accurate measuring instrument cannot be applied. This correction is also known as calibration or calibration. It is important to manage the accuracy of the measuring instrument under regular calibration.
Since metals are susceptible to thermal mutations, thorough temperature control is important for precise measurements. According to JIS standards, the dimensions specified in the drawings are defined as “values in an environment of 20 °C”.
Types of Dimension Measuring Tools (Measuring Instruments) Used in Metal Processing
Measuring tools or measuring instruments are tools for workers to “measure with their hands”. Caliper stuck in the engineer’s pocket, is familiar as a standard tool in the field, but in addition, various measurement tools such as saws and micrometers are used in metalworking sites.
Depending on how the measuring tool is used, even the same workpiece may be uneven in the measured value depending on the operator or the workpiece may be scratched. In order to use it accurately, it is important to accumulate daily experience.
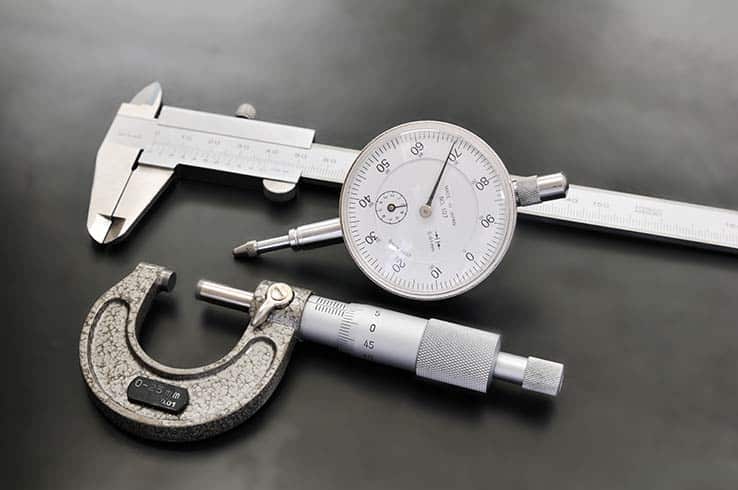
- Caliper
Calipers are one of the most common measuring tools in metalworking. It is widely used not only in “measurement at the time of work installation” and “measurement after processing” of NC machine tools, but also in various industries such as machine design and automobile maintenance.
By integrating the workpiece into two claws called “measurement jaws”, it can be easily measured in units of 0.05 mm, and the outer diameter, inner diameter, and depth can be measured with a single saw. The standard length is 300 mm, but there are also long types of 1000 mm or more.
There is also a “digital caliper” whose numerical display has become digital. The digital type can be measured in 0.01 mm increments by reading the internal scale by the sensor. Digital calipers are easy to handle even for beginners, but since batteries are required compared to analog, they are also preferred in the field.
- Micrometer
Micrometers are one of the most common measuring tools in metalworking. By interspersing the workpiece while rotating the measuring instrument, it can be easily measured in units of 0.01 mm. Since the center of the workpiece and the center of the measuring instrument overlap at the time of measurement, the measurement accuracy is higher than that of the sawduce.
Due to the structure of the main unit, the measurement range is limited to 25 mm, so it is necessary to prepare multiple micrometers depending on the type of workpiece (for 0 to 25 mm, for 25 to 50 mm, for 50 to 75 mm, for 75 to 100 mm, etc.). A dedicated micrometer such as an “inner micrometer” for inner diameter measurement and a “depth micrometer” for depth measurement is required.
Similar to calipers, there is also a “digital micrometer” whose numerical display is digital. The digital type can measure in units of 0.001 mm.
- Dial Gauge
Micrometers are highly accurate measuring tools used in metalworking sites. It is used to measure displacement in microns rather than measuring size, such as paralleling of workpieces attached to nc machine tool tables and cores of NC lathe workpieces.
Since it is not possible to measure with a dial gauge alone, use it by attaching it to a jig or magnet stand. In addition, the stylus at the tip can be replaced according to the shape of the work such as rollers and needles. There are various types such as “lever type” and “digital type”.
- Pin Gauge
Pin gauges are round bar measuring tools that are precisely finished to a given size. It is often used for inspection of inner diameter after hole machining. (If the pin gauge passes through the hole, if it does not pass, fail, etc.)
It is difficult to handle, and attention should be paid to thermal expansion due to temperature changes and the occurrence of rust. It is made of highly durable materials such as ceramics and cemented carbides.
- Ring Gauge
The ring gauge is a donut-shaped measuring tool that is precisely finished to the specified size. It is used for the opposite purpose of pin gauge, such as inspection of bar material after turning.
- Limit Plug Cage
The limit plug cage is a round bar measuring tool that is precisely finished to a predetermined size. Gauges of “street side” and “stop side” are attached to both ends of the tool respectively.
It is used in the inside diameter inspection of the hole with a tight tolerance (If you insert the tool into the hole, the “street side” enters and the “stop side” does not enter, it is pass).
Compared to calipers and micrometer, it is characterized by less variation in measurement by workers.
- Block Gauge
A block gauge is a block-shaped measuring tool that is precisely finished to a given size. It has the highest accuracy among measuring tools and is also used to calibrate measuring instruments. The high parallelism ensures accurate dimensions when stacked.
It is difficult to handle, and care must be taken to prevent thermal expansion and rust due to temperature changes (Do not touch the measurement surface directly with your bare hands, and handle it with chamois or waste cloth).
It is made of highly durable materials such as ceramics and cemented carbide.
- Feeler Gauge (Thickness Gauge)
Feeler gauge is a thin plate-shaped measuring tool finished to the specified size. By sandwiching it between objects, the size of a slight gap is measured. By combining thin plates of different thicknesses, it is possible to measure gaps of various sizes.
- Height Gauge
Height gauges are measuring tools for measuring workpiece heights. The height gauge and workpiece are placed on a surface plate (horizontal table) and measured in the same manner as height measurement.
The tip of the measuring instrument is made of cemented carbide, and it is also possible to do injury work (writing reference lines and hole positions on the surface of the workpiece).
- Pressure Sensitive Paper
Although it is a little different from the measuring tool, a special film called “pressure sensitive paper” may be used to check for slight gaps and adhesion. By sandwiching the pressure-sensitive paper and putting the surface in close contact with each other, a slight gap develops a color, and fine adjustment is made based on the color development.
Types of Measuring Machines Used in CNC Machining
A measuring machine is a mechanical device with a built-in sensor. Even complicated shaped workpieces can be easily measured, and there is no variation in measured values due to differences in workers. Work efficiency is higher than that of analog “measurement tools”, and work can be easily inspected.
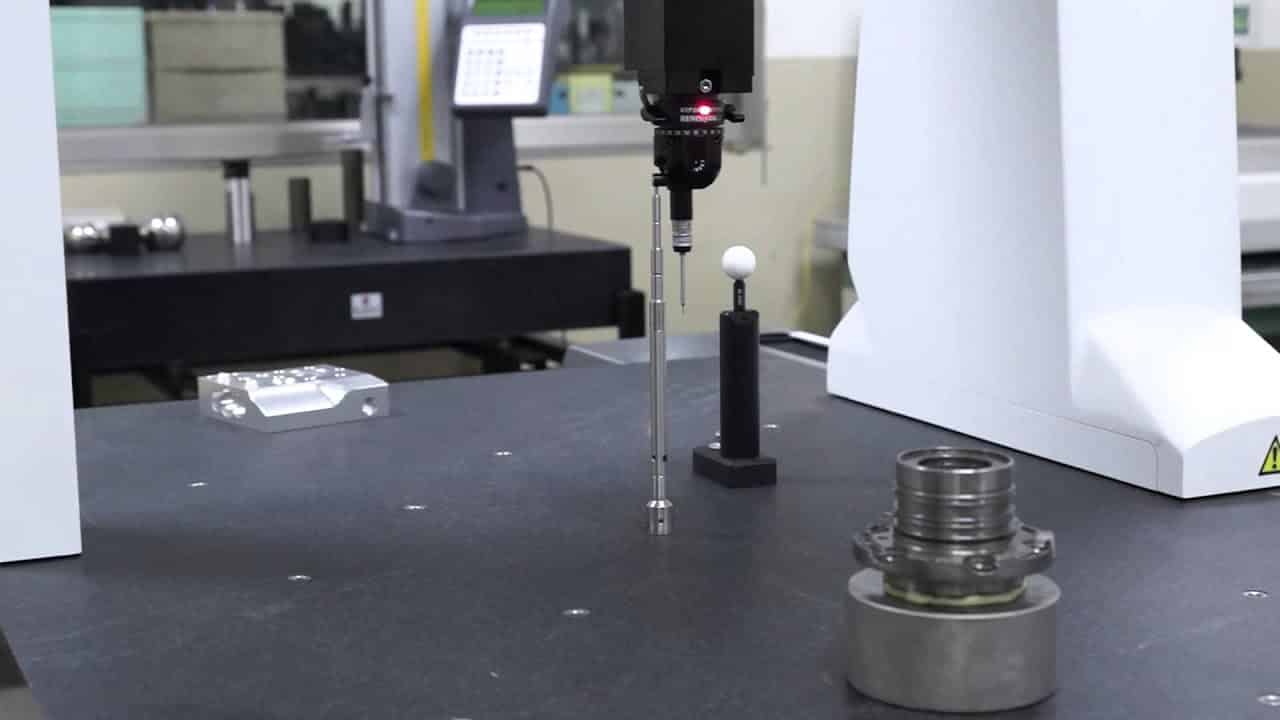
Various measurement principles such as “electricity” and “air” are used for measurement.
A coordinate measuring machine is a measuring machine for measuring the three-dimensional dimensions (width, depth, height) of a work. It is also called CMM, which is an acronym for English (Coordinate Measuring Machine). A contact probe or non-contact laser is applied to the workpiece to detect the X, Y, and Z coordinates. It is often used in conjunction with machine tools, such as checking the position of workpieces attached to pallets before machining, inspecting accuracy during machining, and inspecting defects after machining.
With the spread of CMM (CMM), the installation environment of CMM is also often installed in harsh environments as measuring machines.
However, even in harsh environments, the demand for measurement accuracy is increasing. You can easily perform measurements that are difficult with analog measurement, such as free-form surfaces cut by 5-axis machining and workpieces with complicated shapes. It goes well with 3D CAD, and by feeding back the measurement results to CAD, it is possible to create drawings from actual workpieces.
- Electric Micrometer
An electric micrometer is a measuring instrument that uses the amount of displacement of electricity. A probe for detection is applied to the work, and a slight amount of electrical displacement is amplified by an amplifier to convert it into a measured value (A device that is completely different from an analog micrometer).
By exchanging the probe for detection, it is possible to handle various measurements such as deep holes and thin workpieces. It is highly accurate and can display measured values in units of 0.001 mm.
- Air Micrometer
The air micrometer is a measuring machine that utilizes changes in air pressure. Compressed air from the air nozzle is applied to the workpiece, and the amount of change in the slightest pneumatic pressure is converted into a measured value (It is a device that is completely different from an analog micrometer).
By replacing the head for measurement, it can be used for various measurements such as outline and inner diameter. Since it is detected non-contactlessly, it is not affected by dust and oil, and there is no worry of damaging the workpiece.
- Image Measuring Machine
The image measuring machine is a measuring machine using camera scanning and image analysis. By simply placing the part on the stage and pressing the scan button, you can measure the dimensions of each part in a fraction of the way, regardless of the proficiency of the worker.
It is also possible to distinguish defective products by causing drawings from parts and collating with CAD data, greatly shortening measurement work.
Summary
In this article, we introduced various measuring instruments used in the field of metal processing, such as measuring tools such as “dial gauges” and “micrometers”, as well as “coordinate measuring machines”.
No matter how expensive a machine is, it is impossible to perform highly accurate processing without “measuring” technology. We hope this article will give you an opportunity to learn about the profound “measurement”.