Dimensional accuracy refers to the accuracy of the dimensions of a specified part, such as the length, diameter, thickness, and keyway width of the workpiece. This dimensional accuracy is important for the part to be integrated into the machine and operate properly. If the dimensions are incorrect, it can cause the machine to fail.
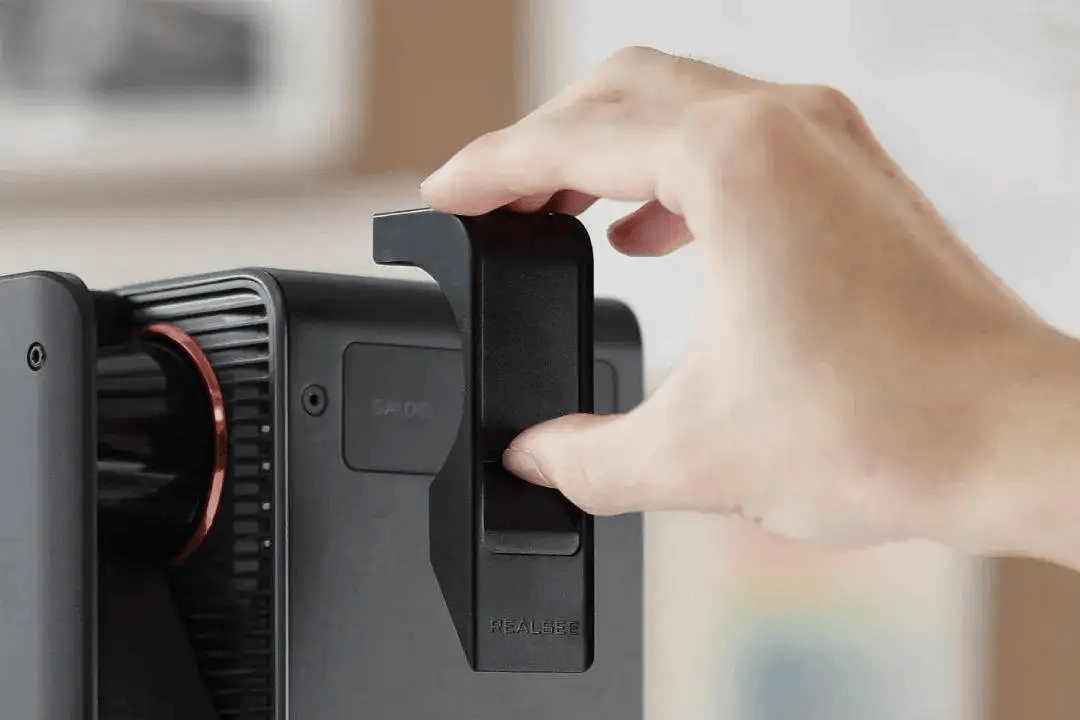
To prevent this, tolerances must be indicated in the drawing so that the dimensional accuracy of the critical parts is available when designing the part. For example, when designing a bearing with an outer diameter of Φ25 axis, it is necessary to indicate a larger tolerance of Φ25 inner diameter Φ25 + 0.1. This is because if there is no tolerance instruction, it will be processed to fit within the general tolerance, and there is a possibility that the inner diameter is Φ24.98 and the shaft with the outer diameter Φ25 does not enter. In order to achieve dimensional accuracy, it is necessary to set the tolerance correctly.
Dimensional Accuracy and Meaning of Dimensional Inspection
There are two main meanings of inspecting dimensions in Quality Inspection:
The first is to check whether the process is processed according to the drawing. The manufacturer is obliged to ensure that the processed product is made according to the drawings. Therefore, it is necessary to inspect the dimensions according to the drawing. In addition, dimensional inspection prevents the outflow of defective products and guarantees the quality of the company.
The second is to improve quality. Manufacturers need to constantly improve quality. Quality is maintained by dimensional inspection, and even if there is a defective product, it can be found. Defective products contain hints to improve product quality. Analyze defective products, identify the cause, and make improvements at the manufacturing site. By running this cycle, quality will naturally improve. Dimensional inspection is carried out for this purpose.
Tolerance
Dimensional accuracy is specified in Tolerance standard:
What is tolerance?
Tolerance is the range of values that are acceptable even if they deviate from the target value.
For example, suppose you receive a request to cut a bar stock with a length of 100 mm to 80.00 mm, and when you measure the finished product with a caliper, it is 80.00 mm. However, since measurement is subject to various influences and the measuring instrument itself has some errors, it is not possible to prove that the actual size is really 80.00 mm. This is called measurement uncertainty.
Also, with this designation, we don’t know if a deviation of about 79.95mm or 80.10mm is OK or NG. The difficulty of the work varies greatly between having to make 80.00mm and making 80.00mm±0.1.
To account for measurement uncertainties and to clarify the required range of accuracy, all dimensions in the drawing include tolerances to show the permissible deviations.
Different tolerances
General tolerance
Among tolerances, those that do not specify a specific range are called general tolerances. (Also called ordinary tolerance)
Even if there is no specification, the tolerance to be within this range is determined at a minimum. Even though it is specified as 80mm, it is not a problem to come with a poor quality such as 80.99mm or almost 81mm.
Thanks to general tolerances, designers who create drawings do not have to write tolerances for dimensions of parts that do not require much accuracy. In addition, tolerances are negotiated not only in length, but also in angle.
Dimensional tolerance
In contrast to general tolerances, those that have a specified tolerance range are called dimensional tolerances. (Also called indicative tolerance or size tolerance) for example, it is expressed as shown in the figure below.
Fit tolerance
When shaft-shaped parts and parts with holes are used together, the fitting tolerance is used.
In the fitting tolerance, the tolerance range can be written with alphabets and numbers according to the standard, and uppercase letters (e.g. H7) are used for holes and lowercase letters (e.g. H6) are used for axes. Sometimes it is written only φ50 H6, sometimes it is written as φ50 (0 ~ +0.019), but both mean the same thing.
In addition, some fittings require sliding depending on the application, and some do not, and there are types such as gaps, intermediate fits, and clutters.
- Gap: Sliding fits.
- Fit: Fitted fit. It comes off when hit with a wooden hammer.
- Fitting: Fitting with strong force such as a machine. Basically, it does not come off.
Even among the gaps, the amount of clearance required depends on whether it is better to slide easily or as much as possible, so the designer selects a combination of tolerance ranges that are considered appropriate.
Geometric tolerance
Geometric tolerances are tolerances in shape and positional relationships such as distortion and misalignment, which cannot be expressed by length and size alone.
For example, even with the aforementioned gap blink parts, even if the diameter accuracy is good, if there is warpage or distortion, it will not fit or slide smoothly.
Means and Tools of Dimensional Inspection
There are two methods for inspecting dimensions: one is to use measuring tools such as calipers and micrometers, and the other is to use inspection equipment such as image measuring instruments and three-dimensional measuring instruments.
Since the method of using the measuring tool is measured by a person, it tends to differ depending on the proficiency level of the inspector. On the other hand, it can be easily measured, so it does not take much time to inspect. Measuring tools include calipers, micrometers, block gauges, and pin gauges.
On the other hand, the method of using inspection equipment is measured by a machine, so it is possible to perform more accurate inspections regardless of the inspector. However, it is necessary to set the object to be measured, operate the machine, and prepare the inspection conditions for accurate measurement, and it takes time for inspection. Inspection equipment includes image measuring instruments and 3D measuring instruments.
How to use and features of Dimensional Inspection Tools
Here are four typical inspection tools:
Calipers
Calipers are measuring tools that measure length. It can measure down to 0.01 mm and basically uses this tool for inspection. However, the measurement accuracy guaranteed by the manufacturer is ±0.2. The reason for this lies in Abbe’s principle. Abbe’s principle is that the exact value cannot be obtained unless the measuring element (jaw in the case of calipers) and the scale are one straight line. Therefore, calipers can cover up to the intermediate level, but it becomes stricter when it becomes more refined. A measuring tool that follows Abbe’s principle is a micrometer. Therefore, areas with severe tolerances are inspected using a micrometer.
Measuring gauge
A measuring gauge is a simple inspection instrument with guaranteed dimensions. Measurement gauges include block gauges, pin gauges, plug gauges, and screw gauges. The most distinctive feature of the measurement gauge is that it can easily and accurately inspect parts that cannot be measured with calipers and micrometers. For example, it is possible to inspect places that cannot be reached by calipers and micrometers, such as deep hole diameters and micron-level dimensional tolerances (H7 tolerances, etc.). In addition, since the accuracy itself is guaranteed, accurate inspection can be performed regardless of the proficiency of the inspector.
Image measuring instrument
Covers objects that cannot be measured with calipers or gauges. For example, soft materials such as rubber and flat complex objects (such as gears) can be accurately measured. It can also measure dimensions with higher accuracy than calipers. It is mainly used to measure the distance between holes, angles, and P.C.D. There is a size limit, and it is difficult to obtain the accuracy of dimensional measurement related to the Z-axis.
3D measuring instrument
Basically, most workpieces can be measured. We mainly inspect geometric tolerances and objects with complex shapes (robot parts, etc.) made by 3D printers. In addition, since the accuracy is in micron units, the actual size value of tight tolerances such as hole diameter of H7 tolerance can be obtained.