In today’s competitive business landscape, maintaining operational productivity and minimizing downtime are paramount. Industrial machinery plays a vital role in the smooth functioning of manufacturing facilities, power plants, and other industrial sectors. A breakdown or failure of these machines can lead to significant financial losses, production delays, and compromised safety. This is where Factory Acceptance Testing (FAT) enters the picture as a crucial step in the manufacturing process.
Factory Acceptance Testing involves subjecting new or modified equipment to comprehensive testing protocols within the confines of the factory before installation or commissioning. It is designed to validate that the machinery meets predetermined specifications, performs as intended, and complies with industry standards and regulations. By simulating real-world operating conditions, manufacturers can identify and rectify potential issues, verify functionality, and ensure that the equipment aligns with the buyer’s requirements.
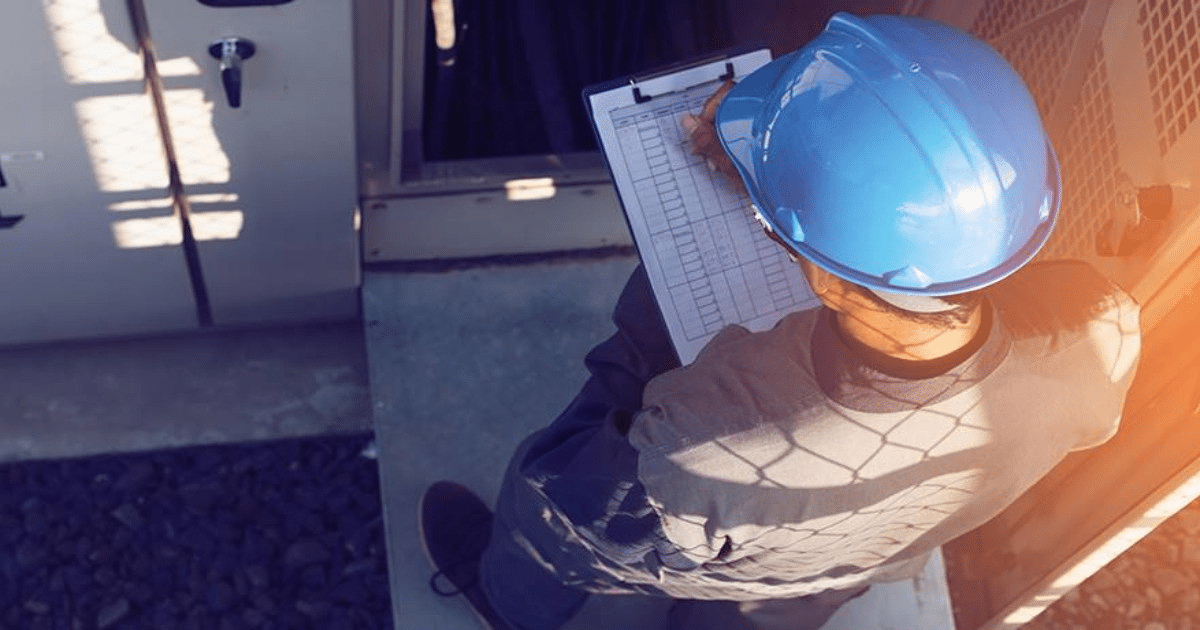
FAT is not limited to a specific industry; it encompasses a wide range of sectors, including automotive, pharmaceuticals, aerospace, energy, and more. Regardless of the industry, the primary objective of FAT remains the same: to enhance the reliability, efficiency, and safety of industrial machinery. By meticulously examining critical parameters, conducting performance tests, and verifying compliance with technical specifications, FAT provides an assurance that the equipment is reliable and ready for operation.
In the subsequent sections, we will explore the various benefits of Factory Acceptance Testing and discuss the key considerations involved in its implementation. Through a comprehensive understanding of FAT, manufacturers can streamline their operations, mitigate potential risks, and ultimately deliver robust, high-quality equipment to their customers.
What is Factory Acceptance Testing (FAT)?
Factory acceptance testing (FAT) is a process of testing equipment or systems at the manufacturer’s facility before it is delivered to the customer. The purpose of FAT is to verify that the equipment meets the customer’s requirements and is ready for installation and use.
FAT is an important part of the procurement process for any equipment or system. It helps to ensure that the customer receives the equipment they need and that it is ready to use when it arrives.
The Importance & Benefits of Factory Acceptance Testing
Factory Acceptance Testing (FAT) is crucial in ensuring the quality and functionality of industrial equipment or systems before they are shipped to the customer’s site. Here are some key reasons highlighting the importance of Factory Acceptance Testing:
- Quality Assurance: FAT provides an opportunity for manufacturers to validate that their products meet the specified requirements and standards. By conducting rigorous testing in a controlled environment, any potential defects or malfunctions can be identified and rectified before the equipment is delivered.
- Risk Mitigation: FAT helps mitigate risks associated with equipment failures or malfunctions at the customer’s site. By thoroughly testing the equipment before it leaves the factory, potential operational issues can be identified, reducing the probability of costly downtime or safety hazards.
- Compliance and Regulations: Many industries have specific regulations and standards that need to be met. FAT ensures that the equipment complies with the industry-specific regulations, safety standards, and any contractual requirements agreed upon by the manufacturer and customer.
- Customer Satisfaction: By conducting Factory Acceptance Testing, manufacturers build trust and confidence with their customers. It demonstrates their commitment to delivering high-quality products that function as intended. Identifying and addressing issues during FAT helps reduce the chances of unexpected problems arising after installation.
- Time and Cost Efficiency: Identifying and rectifying issues during FAT is generally more cost-effective and time-efficient than addressing them after installation at the customer’s site. FAT minimizes the need for on-site troubleshooting and rework, thereby reducing installation and commissioning time.
- Documentation and Traceability: FAT provides a comprehensive record of the testing process, including test procedures, results, and any modifications made. This documentation serves as a reference for future troubleshooting, maintenance, or upgrades, ensuring proper traceability and facilitating efficient support.
While newer file systems like NTFS and exFAT offer enhanced features and capabilities, the importance of FAT lies in its simplicity, compatibility, and long-standing support across different devices and operating systems.
The Process of Factory Acceptance Testing
The process of Factory Acceptance Testing (FAT) typically involves the following steps:
- Test Plan Development: The manufacturer and the customer collaborate to develop a detailed test plan that outlines the specific tests to be performed on the equipment or system. The test plan includes objectives, test procedures, acceptance criteria, and any industry-specific regulations or standards to be followed.
- Test Setup: The manufacturer prepares the equipment for testing by configuring it according to the customer’s requirements. This includes installing necessary software, calibrating instruments, connecting peripherals, and ensuring that all components are in place.
- Test Execution: The actual testing takes place based on the agreed-upon test plan. Different tests and scenarios are performed to validate the equipment’s functionality, performance, and compliance with requirements. This may involve running specific operational modes, simulating various conditions, or executing predefined test cases.
- Defect Identification: During the testing process, any defects, malfunctions, or deviations from specified requirements are documented. These issues may range from minor operational glitches to critical failures. The manufacturer’s testing team systematically identifies and categorizes the defects for further analysis.
- Issue Resolution: Once defects are identified, the manufacturer takes appropriate actions to rectify the issues. This may involve troubleshooting, making adjustments, repairing or replacing components, or implementing software updates. The aim is to address the identified issues and ensure that the equipment meets the required performance standards.
- Retesting: After resolving the identified defects, the equipment undergoes retesting to confirm that the issues have been successfully addressed. The previously failed tests are repeated to verify that the equipment now meets the acceptance criteria outlined in the test plan.
- Documentation and Reports: Throughout the FAT process, detailed records are kept, including test procedures, test results, defect logs, modifications made, and any other pertinent information. These documents serve as an official record and provide traceability for future reference, support, and maintenance.
- Acceptance Decision: Upon successful completion of the FAT process, both the manufacturer and customer review the test results and documentation. Based on the agreed-upon acceptance criteria, a joint decision is made regarding whether the equipment has passed the FAT and is ready for shipment and installation.
The specific steps and procedures may vary depending on the industry, equipment type, and contractual agreements between the manufacturer and customer. However, the general aim of the FAT process is to ensure that the equipment meets the specified requirements, standards, and regulations before it is delivered to the customer’s site.
The Different Types of Factory Acceptance Testing
There are many different types of factory acceptance testing (FAT), depending on the industry and the equipment being tested. Some of the most common types of FATs include:
Mechanical FAT: This type of FAT tests the mechanical components of an equipment, such as its structural integrity, alignment, and movement.
- Electrical FAT: This type of FAT tests the electrical components of an equipment, such as its power supply, wiring, and circuitry.
- Control system FAT: This type of FAT tests the control system of an equipment, such as its software, sensors, and actuators.
- Software FAT: This type of FAT tests the software of an equipment, such as its functionality, performance, and security.
- Environmental FAT: This type of FAT tests the equipment’s performance in different environmental conditions, such as temperature, humidity, and vibration.
- Safety FAT: This type of FAT tests the equipment’s safety features, such as its guards, interlocks, and emergency shutdown systems.
The specific tests that are performed during a FAT will vary depending on the equipment being tested. However, all FATs should include the following steps:
- Review of the equipment’s specifications and drawings.
- Visual inspection of the equipment.
- Functional testing of the equipment.
- Performance testing of the equipment.
- Safety testing of the equipment.
- Documentation review.
The results of the FAT are used to determine whether the equipment meets its acceptance criteria. If the equipment does not meet the acceptance criteria, it may be necessary to rework or replace the equipment.
In addition to the above, there are also some specific types of FATs that are used in certain industries. For example, the aerospace industry uses a type of FAT called a Functional Configuration Audit (FCA). An FCA is a comprehensive review of the design, manufacturing, and testing of an aircraft or spacecraft. The FCA is used to ensure that the equipment meets all of the requirements of the applicable regulations.
The oil and gas industry uses a type of FAT called a Pre-commissioning Test (Pre-COM). A Pre-COM is a test that is conducted before an oil and gas production facility is placed into service. The Pre-COM is used to verify that the facility is ready to operate safely and efficiently.
The pharmaceutical industry uses a type of FAT called a Validation Acceptance Test (VAT). A VAT is a test that is conducted to verify that a pharmaceutical manufacturing process is capable of consistently producing products that meet the required specifications.
Factory acceptance testing is an important part of the quality assurance process. By conducting a thorough FAT, the customer can ensure that the equipment they are purchasing meets their needs and expectations.
Factory acceptance testing is an important part of the procurement process for any equipment or system. It helps to ensure that the customer receives the equipment they need and that it is ready to use when it arrives.
By understanding the importance of FAT, the different types of FAT, and the benefits of vFAT, you can help to ensure that your next FAT is a success.