The final inspection is a critical step in the quality control of manufacturing to ensure the quality of the finished products. Why do you need a final inspection and how is product final inspection done?
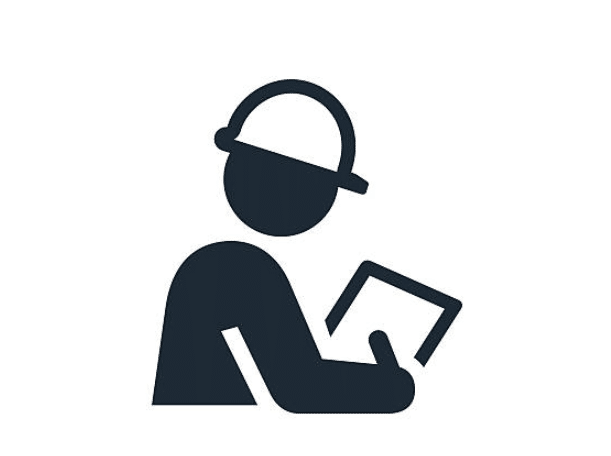
What is the Final Inspection in Quality Assurance?
A final inspection is a critical step in quality assurance that is performed at the end of the production process to ensure that the final product meets all the required quality standards and specifications. The purpose of the final inspection is to identify and address any defects or issues that may have occurred during the manufacturing process and to ensure that the product is safe for use and meets customer expectations.
During the final inspection, the product is thoroughly examined and tested to ensure that it meets all the specified requirements, such as size, shape, color, functionality, and safety. This may involve visual inspections, measurements, functional tests, destructive testing, and other types of quality control methods. Any defects or non-conformities are documented, and corrective actions are taken to address them.
It is an essential part of quality assurance that helps to minimize the risk of product recalls, customer complaints, and other quality-related issues that can have a negative impact on a company’s reputation and bottom line.
Why Do You Need a Final Inspection?
Product final inspection is essential for several reasons:
- Ensure Quality: The primary purpose of final inspection is to ensure that the product meets all the required quality standards and specifications. The final inspection helps to catch any defects or issues that may have occurred during the manufacturing process and ensure that the product is of high quality and safe for use.
- Minimize Risk: Final inspection helps to minimize the risk of product recalls, customer complaints, and other quality-related issues. Catching any defects or issues before the product reaches the customer helps to avoid any negative impact on the company’s reputation and bottom line.
- Compliance: Final inspection is often required to meet regulatory or industry standards. For example, products in the medical or aerospace industries must meet stringent safety and quality requirements, and final inspection helps to ensure compliance with these standards.
- Customer Satisfaction: A high-quality product is critical for customer satisfaction. The final inspection helps to ensure that the product meets customer expectations and performs as intended.
- Continuous Improvement: Final inspection data can be used to identify opportunities for process improvement. Any defects or issues found during the inspection can be analyzed to identify the root cause and make any necessary improvements to the manufacturing process.
The purpose of the final inspection is to ensure the product is of high quality, meets customer expectations, and complies with regulatory and industry standards. It helps to minimize risk and identify opportunities for process improvement, leading to improved customer satisfaction and a stronger bottom line.
How is Product Final Inspection Done?
Product final inspection is a critical step in the quality control process, and it involves several steps to ensure that the product meets all the required quality standards and specifications. The following are the typical steps involved in product final inspection:
- Visual Inspection: The product is visually inspected to ensure that it meets the specified dimensions, shape, and color. Any visible defects such as scratches, dents, or discolorations are noted, and corrective action is taken if necessary.
- Functionality Test: The product is tested to ensure that it functions correctly and meets the specified performance requirements. This may involve testing the product’s features, such as buttons, switches, or moving parts, to ensure they work as intended.
- Safety Test: If the product is designed for safety-critical applications, it may undergo additional safety tests to ensure that it meets the required safety standards. For example, if the product is an electrical appliance, it may undergo electrical safety testing.
- Measurement and Calibration: The product is measured using calibrated instruments to ensure that it meets the specified dimensions and tolerances.
- Packaging and Labeling Inspection: The product packaging and labeling are checked to ensure that they are correct and meet the specified requirements. This may involve checking the labeling for accuracy and ensuring that the packaging protects the product adequately.
- Documentation Review: The inspection team reviews the product documentation to ensure that it meets the specified requirements and that all necessary information is present.
- Record Keeping: The inspection team documents all the results of the inspection, including any defects or non-conformities found and corrective actions taken.