Quality management generally includes three aspects: incoming material quality management, process quality management, and shipment quality management. Enterprises can control the quality from the above three aspects and find the best method. IQC is a solution for the company to deal with suppliers and a gateway to control the quality of suppliers.
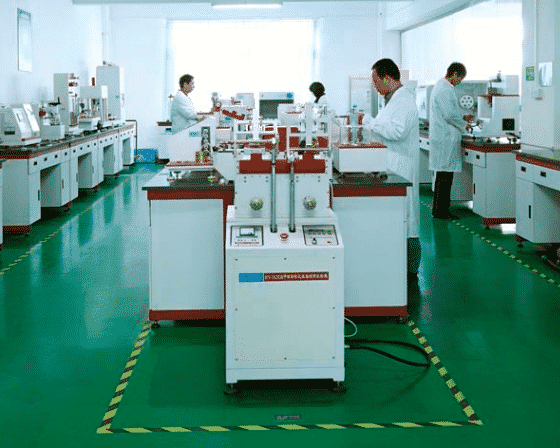
What is Incoming Quality Control?
Incoming Quality Control (IQC) refers to the quality confirmation and verification of purchased raw materials, components or products, that is, when the supplier sends raw materials or components, the quality is inspected by sampling, and finally it is judged whether the batch of products is accepted or rejected.
Importance and Advantages of Incoming Quality Control
IQC is the first quality control gate of suppliers before production. If unqualified products are put into the manufacturing process, it will lead to unqualified manufacturing processes or final products and cause huge losses. IQC not only affects the quality of the company’s final products but also affects various direct or indirect costs. In the manufacturing industry, the four main items that have a direct impact on product quality are usually design, incoming materials, manufacturing process, and storage and transportation. Generally speaking, design accounts for 25%, incoming materials for 50%, manufacturing process for 20%, and storage and transportation for 1% to 5%. To sum up, incoming material inspection plays an overwhelming role in the company’s product quality, so we should raise the incoming material quality control to a strategic position.
Responsibilities of IQC Inspector
- Inspection
The main work is incoming material inspection, and IQC inspection can be briefly described as all or main characteristics of outsourced and purchased materials, which can be confirmed with reference to the relevant standards of the material; Or confirm whether it meets the use requirements. - Deal with material quality problems
IQC shall also track and deal with the quality problems found in the quality inspection process, as well as the major material quality problems fed back by production and market, and establish preventive measures within IQC. - Statistics and feedback of material quality problems in the whole process
The quality data in the process of receiving and inspection of incoming materials shall be counted and fed back to relevant departments in the form of weekly report and monthly report as the basis for the quality control and management of incoming materials of suppliers. - Participate in the process optimization of material related departments
Participate in relevant process optimization in logistics control, and put forward suggestions and opinions on process optimization related to material inspection in logistics.
Methods of IQC Inspection
Incoming inspection, also known as acceptance inspection, is the control point to prevent defective materials from entering the material warehouse. It is also the main information source for evaluating the supplier. The quality reliability of the supplier and the quantity, unit price, and volume of materials shall be planned as full inspection, sampling inspection, and exemption from inspection. The requirements are as follows:
- Full inspection: small quantity and high unit price
- Sampling inspection: materials with large quantity or frequent
- Inspection exemption: materials with large quantity, low unit price or general subsidy or certified as inspection exemption manufacturers or limitations
Among them, acceptance sampling is mostly used by customers to evaluate whether the batch incoming materials of suppliers are acceptable. Under the following circumstances, the advantages of sampling inspection will be particularly prominent.
- Destructive testing of incoming materials is required.
- Due to cost and time reasons, full inspection cannot be realized.
- The acceptable products of incoming suppliers have a good history.
Important Terms of Sampling Inspection
1. Quantitative Data
The quantitative sampling scheme mainly judges whether the incoming batch is acceptable by the defect quantity of the incoming batch. 0 defect plan is also included in the quantitative sampling scheme. It mainly determines whether the incoming material is acceptable by checking whether the acceptable quality level (AQL) is within the acceptable range, that is, only a certain number of defective products.
2. Qualitative Data
The qualitative sampling plan mainly judges whether the incoming materials are acceptable based on the measurement results. Considering the cost and efficiency, the sampling quantity required by the qualitative sampling plan is usually much less than that required by the counting quantitative plan. The qualitative sampling plan of SPC Software is mainly based on the following four input parameters: acceptable quality level (AQL), Lot Tolerance Percent Defective (LTPD), producer risk, and customer risk.
3. Acceptable Quality Level (AQL)
The acceptable quality level (AQL) is usually defined as the rate of nonconforming products that can be accepted in the submitted batch at 95%. 95% of the time, the submitted batches with quality equal to or higher than AQL will be received. If a batch is rejected, there is 95% confidence that the quality of the batch is worse than AQL. Similarly, the probability of rejection of batches with AQL quality is 5%. AQL is not the necessary quality level for the batch produced or received. It’s not even a quality goal. It is only a simple percentage of non-conformities based on the producer’s risk or the probability of rejecting acceptable batches.