Line production is a method that enables the smooth and high-volume production of the same product by organizing various processes into a predetermined sequence. It is excellent for the production of single products as machines and equipment can be arranged in the order of the processes, allowing for efficient mass production. However, line production alone cannot guarantee the production of inexpensive and high-quality products. Inspection is essential. In line production, both “inline inspection” and “offline inspection” are utilized.
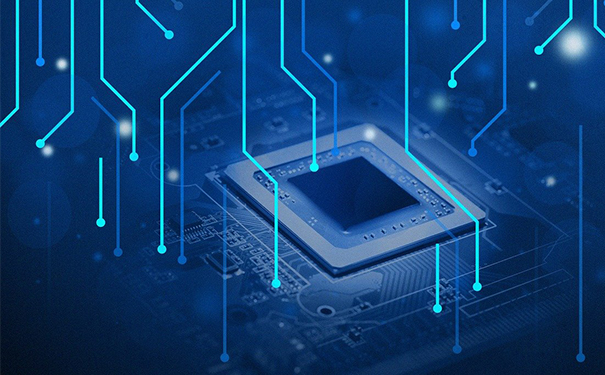
In this article, we will provide an overview of “inline inspection” and “offline inspection” in line production, along with their respective advantages and disadvantages.
What is Inline Inspection?
Inline inspection refers to the inspection method that incorporates an inspection process within the production line. It is characterized by its ease of conducting 100% inspection and its high productivity.
However, visual inspection has limitations due to human physical and cognitive capabilities. Therefore, it is common to automate the process using inspection equipment.
Methods of Inline Inspection
In inline inspection, sensors are installed along the production line to measure the target objects. Based on pre-set threshold values, the system determines the quality of the products.
The specific methods may vary depending on the site. For example, by preparing samples of good and defective products in advance, settings can be established for dimensions or detection counts to be classified as defects based on CCD camera images. If any foreign object is detected in a product, the system automatically performs quality determination according to the set criteria. If the detected foreign object exceeds the specified level of defect, further analysis such as counting is conducted, and the product’s quality determination is outputted.
Inline Inspection Tools
An inline inspection tool, also known as an inline inspection system or machine, is a device or system used to perform inspections directly on the production line. These tools are designed to automate the inspection process and provide real-time feedback on the quality and characteristics of products as they move through the production line.
Here are a few common inline inspection tools:
- – Borescope/endoscope – A flexible tube with a camera used for visually inspecting the interior of enclosed spaces. It can be used to inspect pipes, engines, structures, etc. without disassembling them. Video or fiber optic borescopes are common.
- – CMM (Coordinate Measurement Machine) probe – A touch probe attached to an articulated arm on a CMM. It allows for highly precise dimensional measurement of internal features without disassembling the part.
- – Dial indicators/dial gauges – A measurement tool with a spindle that indicates displacement on a graduated dial. Often used with attachment extensions to reach internal features for runout or concentricity measurements.
- – Micrometers/calipers – Precision measurement tools that can be fitted with extensions to reach into confined spaces for internal diameter, bore, thickness, etc. measurements.
- – Probes – General term for custom or specialized measurement probes, often attached to a CMM, thickness gauge, hardness tester, etc. Probes come in many forms to fit test applications. Common examples include depth probes, thread probes, gap probes.
- – Non-contact sensors – Measurement tools like eddy current probes, laser sensors, ultrasound probes that can take readings of internal features without contacting the part. Useful where contact measurement could damage fragile components.
- – Boroscopes with measurement optics – Endoscopes equipped with tools like micrometers, probes, gages integrated into the viewport for internal visual inspection and measurement.
Advantages and disadvantages of Inline Inspection
Pros
The main benefits of inline inspection are as follows:
- 1. Easy implementation of 100% inspection.
- 2. Immediate detection of abnormalities on the spot.
- 3. Reduction in labor costs through automation.
Inline inspection is well-suited for conducting 100% inspection as it can be performed directly on the production line. The ability to detect abnormalities on the spot allows for prompt feedback. While there are initial costs involved, inline inspection is compatible with automation, which can help reduce labor costs.
Inline inspection is suitable for situations where quality assurance and addressing labor shortages are important considerations.
Cons
The main drawbacks of inline inspection are as follows:
- 1. Requires facility design for automation.
- 2. Involves complexity and time for equipment installation.
- 3. Incurs initial costs.
To automate the inspection process, facility design is necessary. Additionally, there is complexity and effort required for installation. As inline inspection requires the introduction of equipment on the production line, there are initial costs involved.
If you are looking to avoid the complexity and costs associated with equipment installation, inline inspection may not be the most suitable option.
What is Offline Inspection?
Offline inspection refers to the inspection process conducted outside of the production line. It is characterized by its ability to perform precise inspections. However, it often requires additional work and time, such as transporting the products to be inspected from the production line and conducting measurements.
It is helpful to think of inline inspection as incorporating the inspection process within the production line (In Line), while offline inspection separates the production line from the inspection process (Off Line).
Methods of Offline Inspection
Offline inspection is commonly performed for complex or physical inspections that are difficult to carry out or manage on the production line. It is also used in cases where continuous production lines cannot accommodate inline inspection machines. In some cases, offline inspection is conducted at the start and end of production, and if no abnormalities are found, it is considered that the products in the batch are of good quality.
In manufacturing facilities with multiple production lines, it can be challenging to introduce the same inline inspection machine to all lines. In such cases, offline inspection through sampling may be conducted for quality assurance purposes.
Offline Inspection Tools
Offline inspection tools are devices or systems used to conduct inspections outside of the production line or production environment. These tools allow for thorough and precise inspections of products or components that may not be suitable for inline inspections.
Here are some common offline inspection tools used to inspect parts externally without needing to be directly installed on the part:
- – Coordinate measuring machines (CMMs) – Very precise measurement systems that use probes to take dimensional readings of a part’s exterior geometry. Parts need to be removed from the production line.
- – Optical comparators – Use magnification and projected scales/lines to precisely compare parts to CAD models or check for geometric tolerances and features. Parts are placed in the field of view.
- – Depth micrometers – Can precisely measure depth of features, holes, grooves, etc. on a part’s exterior.
- – Micromasters/macroscope systems – Combination of microscope and measurement components to closely examine small details and features on a part surface.
- – Surface plate and micrometers – Flat tables with attached precision measurement tools like micrometers, height gauges used to measure flatness and dimensions of a part placed on the surface plate.
- – Roundness testers – Rollers or air bearing spindles rotate a part while sensors detect out of roundness deviations on features like diameters, holes, etc.
- – Form measurement machines – Non-contact scanners that create a 3D map of a part’s outer surface geometry to check for inaccuracies.
- – Hardness testers – Indent metal parts to precisely measure surface hardness using standardized scales like Rockwell or Vickers.
- – Profilometers – Trace an probe along surfaces to measure roughness, waviness and other surface texture parameters important for sealing, wear, etc.
- – Multi-sensor CMMs – Higher end CMMs equipped with additional sensors for more complex inspections like scanning probes.
Advantages and disadvantages of offline inspection
Pros
The main benefits of offline inspection are as follows:
- 1. Convenient for conducting precise inspections.
- 2. Enables sampling inspection.
- 3. No initial costs involved.
Since offline inspection is conducted outside the production line, it does not affect the speed of the production line. This allows for time-consuming and precise inspections, making it well-suited for sampling inspection. Additionally, offline inspection does not require the introduction of specialized equipment, resulting in no initial costs.
Cons
The main drawbacks of offline inspection are as follows:
- 1. Quality variations may occur with human inspection.
- 2. Not suitable for 100% inspection.
- 3. Incurs labor costs for human inspection.
Maintaining consistent quality is challenging with human inspection, and it is not suitable for conducting 100% inspections due to the limited number of inspections that can be performed per person. Furthermore, increasing the number of inspectors leads to higher labor costs.
Differences Between Inline and Offline Inspection
The main differences between inline and offline inspection are:
1. Location: In-line inspections are performed on the production line, while offline inspections are performed off-line.
2. Inspection method: In-line inspection is performed using automated inspection equipment and sensors, while offline inspection is typically performed by human eyes or hands.
3. Inspection target: In-line inspection is suitable for products with large production volumes or products with simple shapes. On the other hand, offline inspection is suitable for products with complex shapes, high unit costs, and low production volumes.
4. Inspection accuracy: In-line inspection uses automated inspection equipment to maintain a certain level of quality, but offline inspection involves human eyes and hands, which can lead to variations in quality.
Therefore, in-line inspection and offline inspection must be used depending on the product characteristics and production conditions. In-line inspection is effective for efficient mass production, while offline inspection is suitable for inspecting high-quality or complex products.