In the manufacturing industry, proper process control at the manufacturing site is directly related to profits. Therefore, companies involved in manufacturing must use appropriate methods to manage manufacturing. However, there are also challenges in manufacturing management, such as insufficient manpower and human error. These issues can be solved by systemizing management. This article provides an overview of manufacturing management, the advantages of systemization, and points to consider when selecting a system.
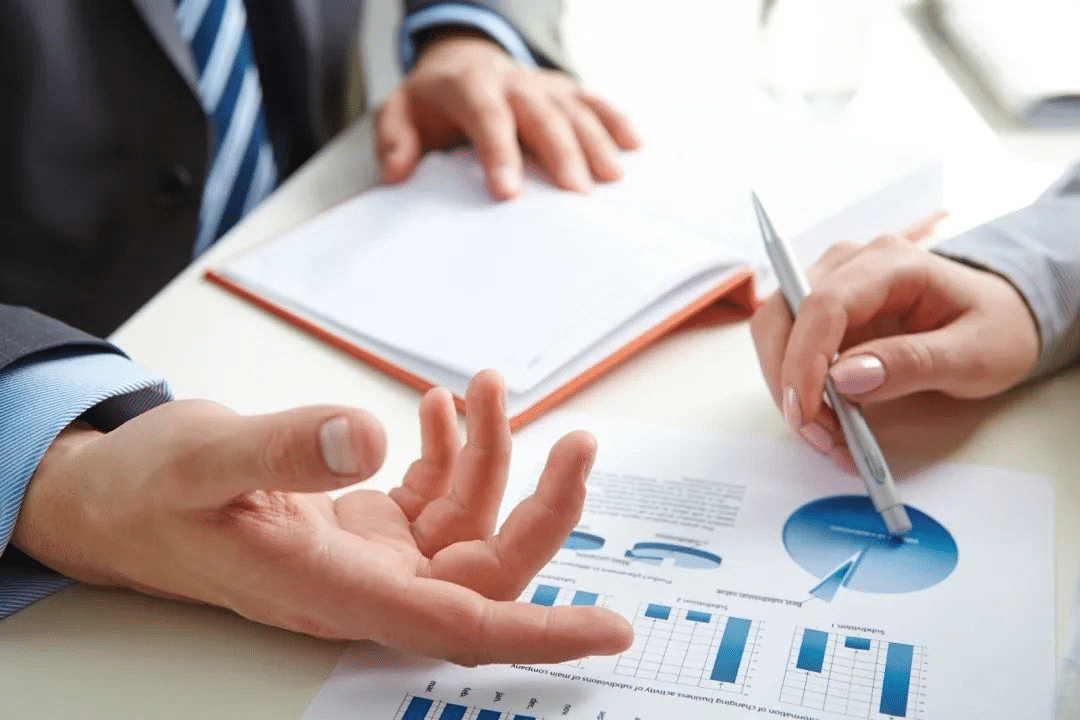
What is Manufacturing Management?
In the manufacturing industry, a variety of management tasks arise. The best known examples are production control and quality control. Manufacturing management is a type of administrative task that is included in production management, and is mainly concerned with the management of progress and processes on the manufacturing floor.
Management Of Work Processes In Manufacturing Site
Production control is the management of work processes in a manufacturing site. If a problem occurs in a process, it can lead to defective products, an increased workload for employees, and delays in production due to lack of resources. In order to avoid such a situation, proper manufacturing control is required at the manufacturing site.
One specific initiative is to check the facilities and equipment used in production. If any of the facilities and equipment required for the work is malfunctioning or showing signs of malfunctioning, there is a risk that the target production volume may not be met. To prevent this from happening, we will conduct a thorough check of the facilities and equipment.
Manufacturing management also includes the assignment of personnel necessary for production. Failure to assign the appropriate number of personnel can lead to work delays. Since work delays can also lead to delays in the delivery of production, proper management is required. Furthermore, inappropriate staffing may place an undue burden on certain employees and must be managed carefully.
Difference Between Production Control, Manufacturing Control, And Quality Control
Production control is the management of a series of production-related processes, such as purchasing raw materials, manufacturing, checking quality, and coordinating production periods. In addition to managing how many orders are received and which and how many products are to be produced by when, it also includes cost control to maximize the organization’s profit.
Manufacturing management is also included in production management. It is as if manufacturing management is included in the larger circle of production management.
Quality control is the management of maintaining product quality. Quality control cannot be neglected because good or bad quality directly affects the organization’s sales and profits. Each process is strictly checked to ensure that the work is being done correctly and that the finished product is free of scratches and stains. Quality control is one of the controls included in manufacturing control.
Three Benefits of Systematizing Manufacturing Management
There are many benefits to be gained by systemizing manufacturing management. It can help solve a variety of issues faced by manufacturing sites and help them evolve into organizations that can respond to a variety of needs.
What Is Manufacturing Management System?
A manufacturing management system is a system or tool that makes management more efficient. Today, a variety of systems have been released, and their implementation can improve operational efficiency and reduce labor shortages.
Manufacturing management can also be done using analog methods. Employees visually check and record the work performed in each process. While this type of analog management is possible, it is not very efficient.
Analog management requires more resources. It requires additional personnel in addition to those who work in the field, which adds to the cost. Also, the fact that management that relies on human hands and eyes can lead to human error is not to be underestimated.
Systemizing production management will enable more efficient management than ever before. Since human errors do not occur and reliable management can be performed, productivity can be expected to increase.
Three Advantages of System Implementation
One of the benefits that system implementation brings is the elimination of labor shortages. In addition, the system will be able to handle huge amounts of data and reduce human error. Another benefit of system implementation is the ability to respond flexibly to the diversifying needs of the market.
Elimination Of Manpower Shortages
The introduction of a system will lead to the elimination of manpower shortages. This is because the system allows employees to do what they used to manage. The number of personnel to be transferred from limited staff to management can be minimized, and resources can be used more effectively.
In addition, when it comes to proper management of a manufacturing site, the person in charge must have the appropriate skills and experience. In some companies, such personnel may be scarce and an excessive burden may be placed on certain employees. On the other hand, if a system is introduced, even employees without high skills or abundant experience can be involved in management, thereby eliminating manpower shortages and excessive burdens on employees.
Furthermore, it will also reduce the cost of education and training. If the system can analyze the data it collects on work and derive how to efficiently produce high quality deliverables, it can be passed on to new employees to shorten their training time.
Coping with huge amounts of data
Manufacturing management generates a wide variety of data. The more data that is handled, the greater the burden on the employees in charge of management, and the less they can process. Systematizing production management will enable you to cope with the huge amount of data and automate the management process.
Another advantage is the reduction of human errors. The style in which employees acquire a vast amount of data on a case-by-case basis inevitably leads to the occurrence of human error. Incorrect values may be recorded, and this may have a negative impact on production.
On the other hand, a system avoids such risks. Even if the amount of data to be handled is huge, the system handles it appropriately and does not record incorrect values. No more mistakes, no more double entry of data, and increased productivity.
Responding to Diverse Needs
As times have changed, market needs have also changed drastically. Traditionally, a style of mass production of a small number of varieties was required, but in recent years, the trend toward high-mix low-volume production has accelerated.
Going against this trend will lead to shrinking profits for the organization. Companies that cannot respond to the needs of the times and the market will be weeded out and their market dominance will be lost to competitors. In order to survive in these changing times, it is necessary to transform to a production system that meets the demands of the times.
The introduction of a manufacturing management system will enable you to respond to diverse needs. The system will allow you to respond flexibly to small-lot production of various types of products and meet the needs of the market without compromising production efficiency.