Non-destructive testing (NDT) refers to inspection techniques used to investigate the interior of an object without damaging it. There are various methods of NDT, each with its own strengths and weaknesses. Therefore, when conducting quality inspections, appropriate methods must be combined based on factors such as the material of the manufactured product. In this article, we will explain the basics of NDT, including the objectives and differences in methods.
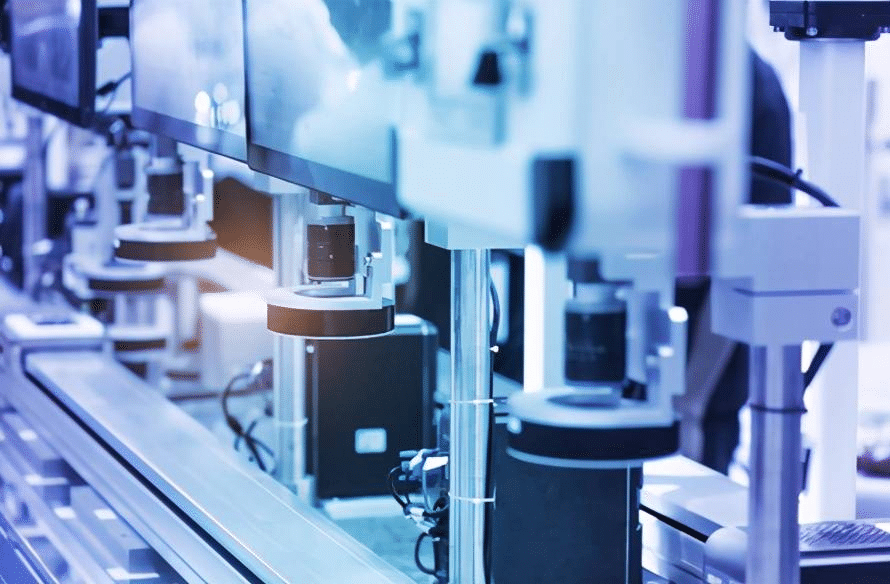
Inspecting products is an important process for those responsible for manufacturing to confirm that quality is being maintained. For inspectors, defects such as foreign objects or scratches may not be visible to the naked eye. However, it is not possible to shave off a part of the product to confirm it.
In such cases, NDT is an effective means of inspection. The most familiar NDT to us is probably the medical checkup. Chest X-rays and abdominal ultrasounds are essential diagnostic techniques for ensuring our health.
The origin of NDT can be traced back to 1895 when Roentgen discovered that X-rays could penetrate even opaque objects that did not allow light to pass through. NDT has been developed to detect welding line defects in steel equipment and is now used in various industries.
What is NDT (NDI)?
When a lump is found in a sealed container with contents that cannot be identified through visual inspection, it is impossible to confirm whether it is a gel-like substance or a foreign object. Cutting the container in half is a form of destructive testing that enables us to confirm whether it is a foreign object. However, when X-rays are transmitted to conduct visual inspection, the shape of the foreign object is clearly displayed as an X-ray image, and we can confirm whether it is a foreign object or not. This is non-destructive testing.
NDT refers to inspection techniques used to detect defects and deterioration on the inside or surface of an object without impairing its shape or function. Defects detected by NDT include “flaws” and “defects.” These have different meanings:
- “Flaws”: refers to unintended discontinuous parts. (Not harmful)
- “Defects”: refer to parts that are immediately harmful in themselves.
NDT detects “flaws.” Inspectors must confirm the detected “flaws” and determine whether they are harmful “defects.”
Objectives of Non-Destructive Testing
(1) Ensuring Reliability
“Reliability” refers to the property of a product that meets the required performance under certain conditions when operated for a certain period of time. This value is called reliability and is evaluated based on factors such as failure rate. For example, a product with a reliability of 100% for one year is considered unlikely to fail for one year. On the other hand, if the reliability for one year is 80%, there is an 80% chance of failure during that year. Non-destructive testing is performed to maintain this reliability over the long term.
(2) Cost Reduction
Factory equipment in the manufacturing industry deteriorates over time. Equipment that operates under high temperature and pressure is subjected to large loads every day. Equipment deterioration can lead to an increase in defective products, and if each piece of equipment fails, production will stop during that time. If an accident occurs, there will also be human and material damage. Non-destructive testing is used for inspections to identify factors that cause such cost increases.
(3) Improvement of Manufacturing Technology
By using non-destructive testing to detect defects and cracks in products, it is possible to reduce the defect rate. In addition, investigating the cause of such defects and providing feedback to the manufacturing process, can lead to the production of higher-quality products.
Types of Non-Destructive Inspection
Next, let’s take a look at the types of non-destructive testing:
1 – Radiographic Testing
This is a method of inspecting the interior of an object by irradiating it with radiation and developing it on a film. Defects such as inadequate fusion in welding or cavities such as blowholes become easier to penetrate by radiation, and the outline is developed on the film. It can be thought of as similar to an X-ray photograph. On the other hand, it is difficult to detect surface defects in materials, so it is desirable to use this method in conjunction with other tests that are designed to detect surface defects, such as magnetic particle inspection, which will be described later. There are also other major inspection methods such as X-ray computed tomography, gamma ray testing, and muon radiography.
2 – Ultrasonic Testing for Deep Defects
This is an inspection method with high detection accuracy for internal defects such as cracks with a planar shape inside a material. On the other hand, it is somewhat difficult to determine defects with certain shapes (especially spherical defects). In recent years, the development of phased array testing and time-of-flight diffraction (TOFD) methods has made it possible to estimate the size and shape of defects by imaging and numerical analysis of the ultrasonic reception signal obtained by controlling the transmission and reception waveforms. Additionally, it is not suitable for testing cast iron or austenitic steel.
3 – Electromagnetic Induction Testing for Deep Defects
This is a testing method that utilizes the electric current (eddy current) that occurs through electromagnetic induction. It is also called eddy current testing or eddy current flaw detection. Due to its nature, it is only used for inspecting materials that conduct electricity. When an AC current is applied to a coil brought near a material, a current that changes like an eddy current is generated inside it. If there is a flaw on the surface, the shape of this eddy current also changes. Therefore, by recording the phase of a good current in advance and comparing it with that of the test material, good/bad can be judged. Furthermore, it is used for a wide range of purposes, such as measuring the change of metal type, component, dimension, coating, and corrosion status by utilizing the change in ease of flow of eddy current due to differences in conductivity. However, it should be noted that it cannot be applied to non-conductive or internal defect testing. Additionally, it is not suitable for testing materials with complex shapes.
4 – Magnetic Particle Inspection
This is a method of inspecting surface defects such as cracks on magnetic metals by detecting changes in the magnetism of the metal. It is possible to inspect surface opening defects and shallow internal defects. As a method of detecting surface defects, it has good sensitivity and allows direct observation by the naked eye, so it has been widely used as the most promising method for a long time. However, due to its nature, it is not suitable for non-magnetic materials such as austenitic stainless steel.
5 – Acoustic Emission Testing
This is an inspection that detects initial signs of crack generation, etc. from the sound generated by the strain of the material. It is used for monitoring crack generation during operation or crack progression, as well as for monitoring during the pressure resistance test of pressure vessels, etc., and has been most practically applied in that field. Its characteristic is that it detects cracks earlier than other testing methods, but the disadvantage is that it cannot detect existing defects.
6 – Penetrant Testing
This is a detection method in which the surface of a material is wetted with a penetrant liquid and then wiped off, and the penetrant that has penetrated into the defect is made visible to the naked eye by absorbing it with powder or the like.