Production Control is one of the initiatives that manufacturing companies are implementing for smooth production activities. In production control, we perform overall management necessary for production activities such as planning, materials, personnel, and equipment. Production control is a very important initiative for manufacturing companies, as proper management and productivity improvement will lead to the growth of the company.
There are a few ideas and terms that should be kept at least in terms of production management. Among them, QCD is a particularly important idea. This time, we will explain what QCD refers to in the manufacturing industry, its way of thinking and how to improve it.
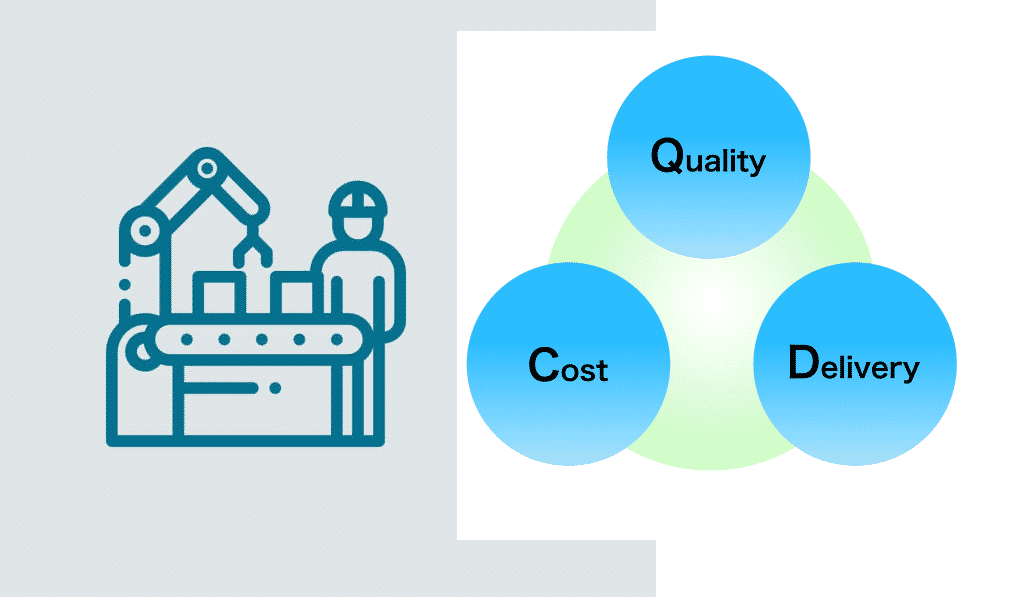
What Is QCD for Production Control?
QCD (Quality, Cost, Delivery) is a coined word that takes the initials of three elements that should be considered when conducting production management in the manufacturing industry in general. Each points to the following elements:
Quality (Quality Management)
Establish and thoroughly establish a line of product quality passing. If this is not the case, take measures such as not shipping as defective products or taking measures such as adding steps to cross the passing line.
Cost (Maintain Cost)
Create a budget to achieve a defined quality and delivery date by calculating human and monetary costs. If there are fluctuations in costs such as raw material costs and labor costs, check and adjust whether the budget is ultimately exceeded.
Delivery (Manage Delivery)
Clarify the production process until the product is shipped, calculate man-hours and time, and schedule it. Pre-Shipment Inspection is necessary. Always check that it is progressing on schedule, and identify and adjust the cause of any disturbances.
Currently, there are several derived types of QCD, some of which are typical examples:
EQCD: Environment + QCD
SQCD: Safety + QCD
QCDS: QCD + Service
QCDF: QCD + Flexibility
While the company’s objective is to pursue profits, its csr initiatives for Corporate Social Responsibility are also beginning to be emphasized. CSR and Factory Audit refers to activities in which a company is a social entity and engages in solving environmental problems and developing local communities in order for its stakeholders (stakeholders: consumers, business partners, investors, employees and their families, society, etc.) to build a better future. Since manufacturing companies are also required to engage in CSR, derived types such as EQCD and SQCD have been born in addition to QCD.
How To Improve QCD in Balanced Way?
Each of the above tasks is different, but it is common to “manage the process from production start to shipment”. In other words, “QCD is balanced” refers to “optimal state that is reasonable for the production process”, and improvement of the production process leads to improvement of QCD.
It is said that improving these factors can improve customer satisfaction, but the most important factor is quality. No matter how cheap the product is or the fast delivery, if you don’t meet the quality your customers want, they won’t be satisfied. When thinking about improving QCD, don’t forget that it’s “quality first”.
However, each element has a “trade-off” relationship that prioritizes one and sacrifices the other elements. While it is true that there are no trade-offs such as automating production lines or there are small-impact improvements, improving one element generally affects other factors.
For example, improving quality can cost more, take longer production time, and faster delivery times can result in poor quality and higher delivery costs. When improving QCD, you have to pay attention to maintaining the balance of each other, while keeping quality in mind.
How To Improve Quality, Cost, Delivery by Optimizing Production Management?
The optimization of QCD will lead to an increase in product quality and profit margins, which in turn leads to the growth of the company. However, as explained in the previous section, since each element of QCD has a trade-off relationship that affects each other, it is important to have a viewpoint of improving the overall QCD in a balanced manner rather than improving each element individually.
When we aim to improve QCD, we tend to focus on each element, but the purpose is to improve productivity and corporate growth. It is a good idea to take improvement measures while taking a bird’s-eye view of the entire process, regardless of the term QCD.
3 Steps To Improve Production Processes For Optimized QCD
How do you improve your production processes? There are three main steps to improving the process. “Grasp the current situation”, “Implementation of improvement measures”, and “Verification and improvement” are . Finally, we’ll show you how to improve the process, with what you need to do in each step.
Step 1 – Investigation of issues by interviewing from the field to grasp the current situation
When we take improvement measures, we start by understanding the current situation in any industry. The same is true for improving production processes in the manufacturing industry. By grasping the business workflow and calculating man-hours how each production process is linked, and hearing from the field, you can extract issues that were not visible numerically.
Step 2 – Implementation of improvement measures Identify issues and measures to be addressed
Next, we will devise and implement improvement measures based on the issues we have grasped in Step 1. If there is a significant cost to improve the process, large-scale measures such as automating the entire plant can be taken. However, small and medium-sized enterprises rarely have large budgets, so it is important to identify issues to be addressed and select effective measures.
Currently, in the manufacturing industry, measures to automate simple tasks such as picking, palletizing, and conveying by introducing industrial robots are attracting attention. The reason is that robots are becoming smaller and cheaper, making them easier for small and medium-sized enterprises to introduce them.
In addition, if the lack of skills of young workers is a problem, training is possible, and measures such as adding confirmation work to reduce the defect rate may be considered. There are countless improvement measures, so consider them according to your company’s challenges and budgets.
Step 3 – It is important to always improve after the implementation of effectiveness verification and improvement
Improvement efforts are not over with the implementation of measures. After doing so, verify whether it actually works and identify the factors behind success or failure by doing During Production Inspection and Production Monitoring. If it works, you can continue to improve QCD by considering new measures to make it even more effective, or by identifying the cause and working on improvements again if it doesn’t work.
When making QCD improvements, production management personnel tend to look at improving each element because they are constantly managing QCD. However, each element of QCD has a trade-off relationship, so if you do not improve the whole thing instead of one by one, you will not get a big effect. In order to achieve QCD improvement, it is effective to identify issues and take improvement measures from the entire production process.