In today’s competitive business landscape, efficient management of product returns is crucial for maintaining customer satisfaction and optimizing operational efficiency. One essential process in the realm of returns is Return Material Authorization (RMA). This article provides a comprehensive overview of Return Material Authorization, delving into its definition, significance, and the steps involved in implementing an effective RMA procedure.
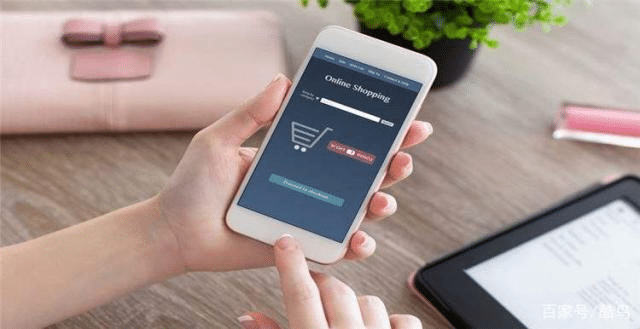
What is Return Material Authorization (RMA)?
Return Material Authorization (RMA) is a formal process used by businesses to manage and control the return of products or materials from customers, suppliers, or distributors. It serves as a systematic way to track, evaluate, and resolve issues related to returned goods. RMA involves obtaining proper authorization, documenting the return details, and implementing appropriate procedures for handling returned items.
The primary purpose of RMA is to streamline the return process, ensuring that it is well-documented, efficient, and in compliance with established policies. It allows businesses to maintain control over returned products, assess their condition, determine appropriate resolutions, and minimize financial losses associated with returns.
Importance of RMA in Supply Chain Management:
Return Material Authorization plays a critical role in effective supply chain management. It addresses the need for managing product returns in a standardized and organized manner, benefiting both the businesses and their customers. Some key reasons why RMA is important in supply chain management include:
- Customer Satisfaction: Offering a well-defined and efficient product return process enhances customer satisfaction by providing a hassle-free and transparent experience. It demonstrates a commitment to customer service and strengthens customer loyalty.
- Inventory Management: RMA enables businesses to gain better visibility and control over returned products. By tracking and analyzing return data, companies can identify trends, understand reasons for returns, and optimize inventory levels accordingly.
- Cost Reduction and Savings: Implementing an effective RMA process helps minimize financial losses associated with product returns. It allows businesses to assess and determine the appropriate course of action for returned items, whether it involves repair, replacement, refund, or other resolutions.
- Opportunities for Product Improvement: RMA provides valuable insights into product quality issues, defects, or recurring problems. Analyzing the data collected through the RMA process helps identify areas for product improvement, leading to enhanced customer satisfaction and reduced returns in the future.
- Strengthened Customer Relationships: A well-managed RMA process demonstrates a commitment to customer service and builds trust. By promptly and satisfactorily addressing return requests, businesses can strengthen their relationships with customers, leading to repeat purchases and positive word-of-mouth referrals.
Key Objectives of Implementing RMA:
Implementing an effective RMA process involves achieving specific objectives that contribute to the overall success of the business. Some key objectives include:
- Streamlining Return Operations: RMA aims to establish clear and standardized procedures for handling product returns. It ensures that all involved parties, including customers, suppliers, and internal teams, follow consistent guidelines for initiating and processing returns.
- Efficient Documentation: RMA seeks to capture essential information related to returned items, including the reason for return, product condition, and customer details. Proper documentation facilitates accurate tracking, evaluation, and resolution of returns while maintaining a comprehensive record for future reference.
- Minimizing Costs and Losses: RMA aims to minimize financial losses associated with returns by implementing appropriate resolution strategies. By assessing the condition of returned products and determining the most cost-effective solution (repair, replacement, refund, etc.), businesses can optimize their return management processes.
- Timely Resolutions: RMA emphasizes prompt and timely resolutions to return requests. By establishing efficient communication channels, quick evaluation procedures, and streamlined return methods, businesses can ensure that customers’ issues are addressed in a timely manner, enhancing customer satisfaction.
- Continuous Improvement: RMA serves as a feedback mechanism for identifying process gaps, product quality issues, and customer concerns. By analyzing return data and regularly reviewing the effectiveness of the RMA process, businesses can identify areas for improvement and implement necessary changes for better outcomes.
Return Material Authorization is a crucial process within supply chain management that benefits businesses by optimizing return operations, enhancing customer satisfaction, reducing costs, and providing valuable insights for product improvement.
Benefits of Return Material Authorization:
Enhanced Customer Satisfaction: Implementing an efficient RMA process contributes to enhanced customer satisfaction. By providing a clear and streamlined process for product returns, businesses demonstrate their commitment to customer service. Customers are more likely to have a positive experience if they can easily initiate a return, receive timely updates on the status of their return, and have their issues resolved in a satisfactory manner.
Improved Inventory Management: RMA plays a significant role in improving inventory management. By capturing data on returned products, businesses gain valuable insights into reasons for returns, product defects, or quality issues. This data enables them to make informed decisions about inventory levels and adjust procurement or production processes accordingly. Effective inventory management helps minimize stockouts, reduce carrying costs, and ensure optimal product availability for customers.
Cost Reduction and Savings: One of the key benefits of implementing RMA is the potential for cost reduction and savings. By having a structured process to assess returned items, businesses can determine the most appropriate course of action for each return, such as repair, replacement, refund, or disposal. This helps minimize financial losses associated with returns, reduces unnecessary expenses, and improves overall profitability. Additionally, analyzing return data can uncover patterns or trends that allow businesses to proactively address root causes and prevent future returns.
Opportunities for Product Improvement: RMA provides valuable insights for product improvement. By analyzing return data, businesses can identify recurring issues, common defects, or areas for enhancement. This information helps in refining product design, manufacturing processes, and quality control measures. Addressing these issues leads to higher-quality products, reducing the likelihood of returns in the future and contributing to improved customer satisfaction.
Strengthened Customer Relationships: A well-executed RMA process strengthens customer relationships. When customers have a positive experience with returns, they feel valued and supported by the business. By efficiently handling return requests, providing clear communication, and offering fair resolutions, businesses can enhance trust and loyalty. Satisfied customers are more likely to become repeat buyers and recommend the business to others, positively impacting the overall brand image.
Return Material Authorization Procedure
The Return Material Authorization procedure is a structured process that ensures efficient handling of product returns while maintaining documentation, accountability, and timely resolutions. While specific procedures can vary based on industry and company policies, the overarching steps involved in the RMA process typically include:
Request Initiation:
The RMA process begins with the initiation of a return request. This can be initiated by the customer or initiated internally in cases of business-to-business returns. Clear communication channels, such as online portals, customer service representatives, or dedicated email addresses, should be available for customers to submit their return requests.
RMA Documentation and Forms:
Upon receiving a return request, the business issues a formal RMA number and provides relevant documentation to guide the customer through the return process. This documentation includes return instructions, any warranty information, and forms that capture necessary details, such as product serial numbers, purchase dates, and reasons for return.
Assessment and Evaluation:
After the return request is received, the business assesses and evaluates the returned product. This involves inspecting the item for damage, verifying its eligibility for return based on predetermined criteria (e.g., within warranty period, unused condition), and determining the appropriate resolution for the return.
Return Method and Shipping:
Once an item is approved for return, the customer is provided with instructions on appropriate packaging, labeling, and the chosen return method. This can include providing shipping labels or coordinating with the customer on return shipping arrangements. It is essential to use reliable shipping carriers and track the shipment to ensure the return’s successful transit.
Product Receiving and Inspection:
Upon receiving the returned item, the business inspects the product to validate its condition and compliance with return criteria. This involves documenting the received product’s physical condition, comparing it with the customer’s return reason, and conducting any necessary quality control inspections.
Solution Determination:
Based on the assessment and inspection, the business determines the appropriate resolution for the return. This can involve repair, replacement with a new or refurbished item, refunding the purchase amount, issuing store credits, or offering an alternative solution as per the business’s policies and customer requirements.
Processing and Record-Keeping:
Once the solution is determined, the business processes the return accordingly. This may involve updating inventory systems, issuing credit notes or refunds, and updating accounting records. It is crucial to maintain comprehensive records of the return, including RMA numbers, customer details, return reasons, resolutions, and any associated costs. These records provide valuable data for analysis and process improvement.
The Return Material Authorization procedure should be consistently followed, and businesses must have a robust system in place to track and monitor the status of each return. Regular evaluation of return metrics and analysis of data can identify areas for improvement in the RMA process, ultimately leading to enhanced efficiency and customer satisfaction.
Return Material Authorization plays a pivotal role in streamlining the return processes of businesses across various industries. By understanding its definition, implementing a well-defined RMA procedure, leveraging technology solutions, and measuring efficiency, organizations can minimize the impact of returns on their operations. With continuous improvement efforts, businesses can enhance customer satisfaction and achieve operational excellence in their RMA processes, ultimately contributing to long-term success.