A sampling plan is a method used to determine and ensure product quality. Here we’ll go through the sampling plan definition, purposes, elements, and different types.
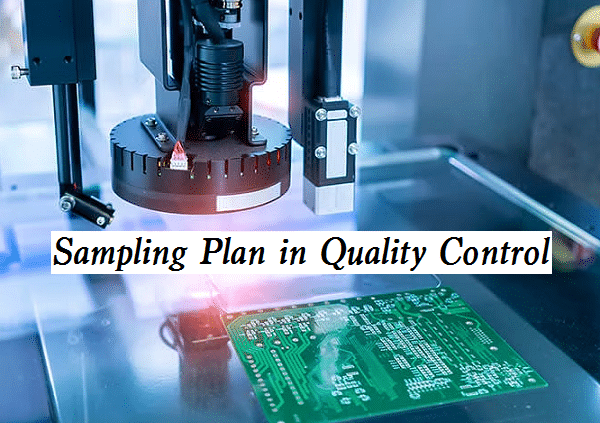
What is Sampling Plan in Quality Control? – Elements & Purposes of Sampling Plan
A sampling plan in quality control is a documented procedure that defines how a sample of items will be selected and inspected to assess the quality of a production process. Sampling plans are used to determine the acceptability or rejectability of a production lot, based on the quality of the sample taken.
A typical sampling plan includes the following elements:
- Sampling size: The number of items to be inspected in the sample, based on the size of the production lot and the acceptable quality level.
- Sampling method: The method used to select items for the sample, which may be random or systematic.
- Acceptance criteria: The criteria used to determine whether the production lot meets the quality standards, based on the number of defective items found in the sample.
- Rejection criteria: The criteria used to reject a production lot that fails to meet the quality standards, based on the number of defective items found in the sample.
- Inspection frequency: The frequency at which samples are taken and inspected, based on the production volume and the criticality of the product or process.
What is the purpose of a sampling plan?
The purpose of a sampling plan is to provide a systematic and objective approach to quality control while minimizing the costs and time involved in inspecting every item in a production lot. The key goals of a sampling plan are:
- To determine the quality level of a production lot: By selecting a sample of items from a production lot and inspecting them according to a predetermined sampling plan, it is possible to determine the quality level of the entire lot.
- To provide a statistically valid basis for decision-making: A well-designed sampling plan ensures that the sample accurately reflects the quality of the entire production lot, and provides a statistically valid basis for decision-making regarding the acceptability or rejectability of the lot.
- To reduce costs and save time: Inspecting every item in a production lot can be time-consuming and costly. By using a sampling plan, it is possible to minimize the costs and time involved in quality control, while still maintaining high levels of quality.
- To ensure consistency and reliability: A sampling plan provides a consistent and reliable approach to quality control, ensuring that the same criteria and methods are used to assess the quality of every production lot.
Types of Sampling Plans in Quality Control
There are several types of sampling plans in quality control, each with its own advantages and disadvantages.
- Random sampling: In this type of sampling plan, items are selected randomly from the production lot for inspection. Random sampling is simple and easy to use, but may not always be representative of the entire production lot.
- Stratified sampling: In stratified sampling, the production lot is divided into subgroups or strata, and items are selected from each stratum for inspection. This can provide a more representative sample of the production lot but can be more complex to implement.
- Attribute sampling: Attribute sampling is used when inspecting items for specific characteristics, such as defects or non-conformances. In this type of sampling plan, items are either accepted or rejected based on the number of non-conformances found in the sample.
- Variable sampling: In variable sampling, measurements are taken on a sample of items to determine whether they meet specific quality standards. This can be more precise than attribute sampling but can be more time-consuming and complex.
- Sequential sampling: Sequential sampling is used when the quality of a production lot needs to be determined quickly. In this type of sampling plan, items are inspected one at a time until the acceptable or rejectable quality level is determined.