Quality management includes quality assurance and quality control. So what is the relationship between QM, QA and QC?
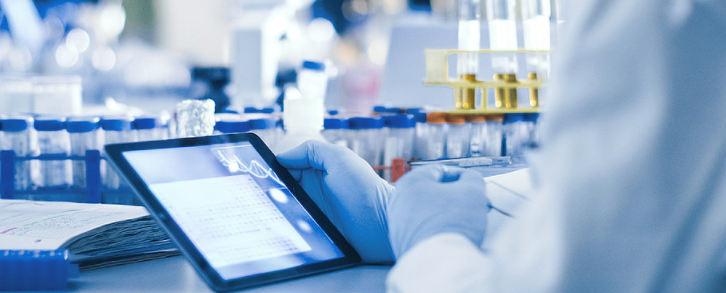
Quality Management Vs Quality Assurance Vs Quality Control
Quality management is all management activities related to quality. Quality assurance is similar to quality control, which is the monitoring of quality, but quality assurance is generally used for inspection method control, such as MSA, and quality control lies in the control of product quality in the production process, controlling various factors affecting product quality from the source of production, so as to ensure that the products produced are qualified.
Quality Control (QC): A part of quality management and emphasizes quality requirements. Specifically, it refers to the sampling, inspection and review of raw and auxiliary materials, packaging materials, intermediate products and finished products according to the specified methods and procedures, so as to ensure that the composition, content, purity and other properties of these materials and products meet the determined quality standards.
Quality assurance (QA): A part of quality management, which emphasizes the guarantee that should be provided to meet the quality requirements. Quality assurance is a broad concept, which covers all factors affecting product quality. It is the sum of all measures taken to ensure that drugs meet their intended use and meet the specified quality requirements.
Quality management (QM): It refers to the organized and planned activities to establish quality policies and quality objectives and achieve quality objectives.
Quality unit, Qu / quality operations (Qo): GMP stipulates that enterprises must establish a quality management department. Moreover, in order to ensure that the quality management department makes independent decisions on product quality and quality related issues, the enterprise shall establish an independent quality management department to perform the responsibilities of quality assurance and quality control. According to the actual situation of the enterprise, the quality management department can set up quality assurance department and quality control department respectively. The quality management department shall participate in all quality related activities and affairs. Therefore, in the department setting of the enterprise, the rapid and effective operation of the quality management department shall be ensured. The responsibilities independently performed by the quality management department in the quality management system shall be specified in accordance with the requirements of relevant laws and regulations, and the responsibilities of the personnel of the quality management department can be entrusted to the designated personnel with equivalent qualifications; In addition to the responsibilities specified in GMP, the scope of work of the quality management department is sometimes extended to registration, clinical research and other fields.
What Links Does Quality Control Generally Include
This means that the cost of content should be controlled widely, but it does not mean that the cost of content should be controlled widely. Different enterprises in all walks of life have different control priorities. The control content can generally be considered from two perspectives: the cost formation process and the cost classification.
1. Control before production this part mainly includes: product design cost, processing technology cost, material procurement cost, production organization mode, material quota and labor quota level, etc. These contents have the greatest impact on the cost. It can be said that 60% of the total product cost depends on the quality of cost control at this stage. This control work belongs to the prior control mode. The real cost has not occurred when the control activity is implemented, but it determines how the cost will occur, and it basically determines the cost level of the product.
2. The control of manufacturing process is the main stage of the actual formation of cost. Most of the costs are incurred here, including raw materials, labor, energy and power, consumption of various auxiliary materials, material transportation expenses between processes, and expenses of workshops and other management departments. Whether various schemes and control measures of pre production control can be implemented in the manufacturing process, and whether most of the control objectives can be achieved are closely related to the control activities at this stage. It mainly belongs to the permanent control mode. As the accounting information of cost control is difficult to be timely, it will bring many difficulties to in-process control.
3. The control in the circulation process includes product packaging, off-site transportation, advertising and promotion, sales organization expenses, after-sales service and other expenses. At present, when it is emphasized to strengthen the market management function of enterprises, it is easy to take various promotion means regardless of cost, but offset the profit increment, so quantitative analysis should also be made.