Various measuring instruments are used to inspect products. For example, innumerable measuring instruments such as straight scales, measures (nogis, micrometers, etc.), pressure gauges, flow meters, current meters, voltmeters, etc. are used for quality inspection. Periodic calibration of the instrument is required to ensure that the instrument shows the correct value. In addition, traceability is required to confirm that the calibration has been performed correctly. Inspectors must make sure that the measuring instrument is calibrated when witnessing. This is because the measured value directly leads to the pass/fail judgment of the product.
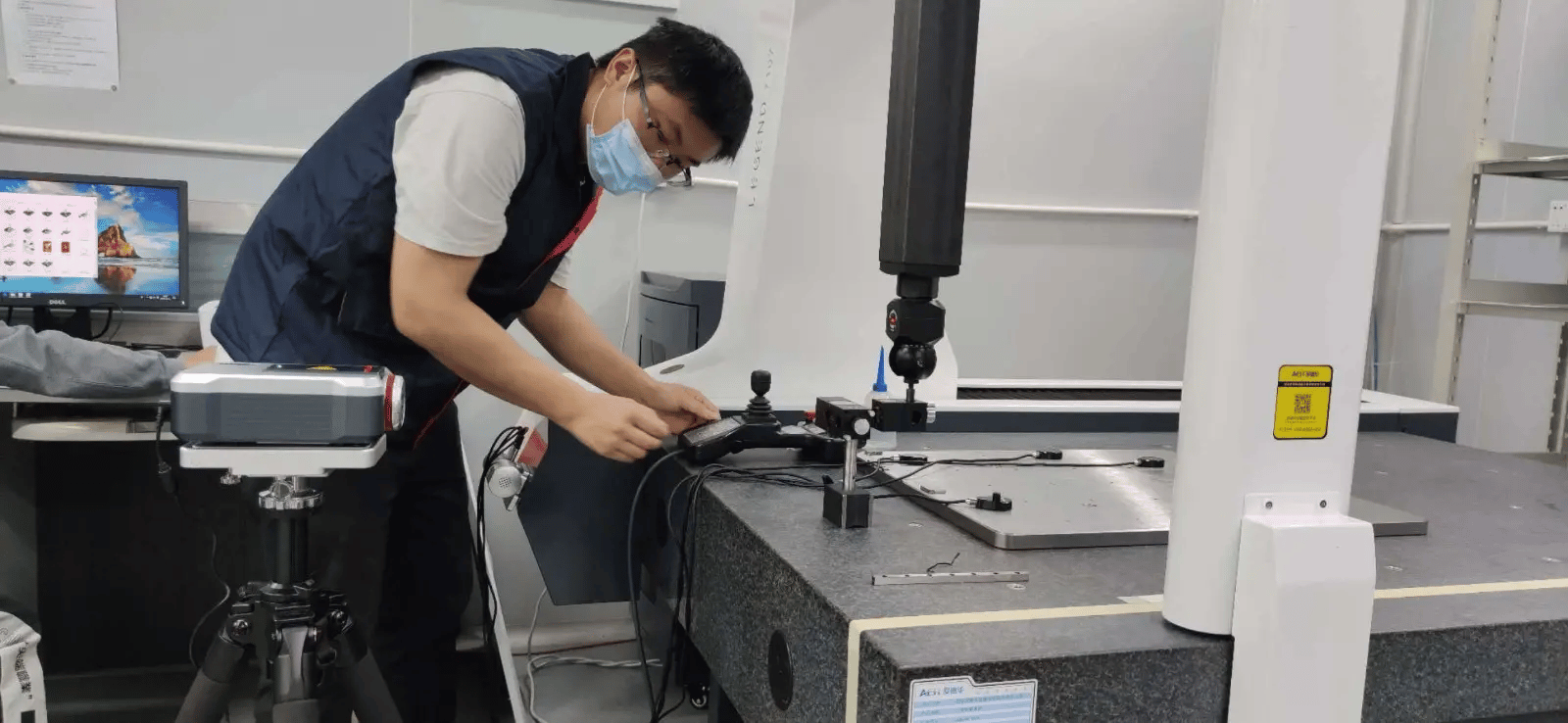
Measuring instruments require regular calibration work. So why do we have to do proofreading? For example, even if your company has obtained ISO9001 (an international standard for quality management systems by the International Organization for Standardization), calibration of measuring instruments is still necessary.
If you do not calibrate your measuring equipment on a regular basis, it can be a major mistake that can damage your company’s credibility. We will explain the meaning of performing the calibration work, the implementation method, and the documents required to prove that the calibration has been performed.
What is Instrument Calibration?
Instrument calibration is a series of operations to determine the relationship between the value indicated by an instrument or measuring system, or the value represented by a measuring instrument or reference material, and the value realized by the standard. It is also defined as “calibration does not include adjusting the instrument to correct errors.”
To put it simply, it can be said that it is a task to compare the reference instrument to calibrate the instrument and the value read from the instrument and check whether there is any deviation.
Why Does The Measuring Instrument Need To Be Calibrated?
In any machine, if it is used for a long time, various parts will deteriorate and break. In order to check for abnormalities. In the case of automobiles, the law stipulates that the vehicle must be inspected periodically. Machine tools are also usually inspected in-house on a daily basis or periodically inspected by manufacturers. The same is true for measuring instruments. If it is used for a long time, various places may deteriorate and it may not show the correct value. Even if it operates without obvious failure, if the adjustment is out of order or the measuring part is worn by contact, accurate readings may not be obtained.
Therefore, what is necessary is “calibration” of the measuring instrument. Calibration is the process of confirming whether the actual machine being used is measuring correctly. We compare the value of the actual machine and the value of the standard machine and grasp the difference (deviation). If calibration determines that adjustments are necessary, repairs and maintenance will be performed. If you use measuring equipment that cannot be measured correctly, you will not be able to maintain the quality of your product. Even if it passes the in-house inspection, if it is deemed defective in the inspection of the delivery destination, it will greatly damage the credibility of the company. By maintaining the accuracy of the measured values through regular calibration work, the quality of your products is indirectly guaranteed. Calibrating measuring instruments is an important task that should not be neglected in the manufacturing industry.
When To Calibrate Your Measuring Instruments?
There are no clear rules about when and at what intervals the calibration work is performed. The ISO 9001 section “Management of Monitoring and Measuring Instruments” states that the procedure should be done at a defined interval or before use, and in accordance with traceable metrology standards in accordance with international or national metrology standards, but the intervals between calibration operations are not specified. At each site, decisions will be made according to each situation.
Measuring equipment manufacturers usually set recommended calibration intervals, such as annually. Based on that, it is often the case that past calibration results are checked and calibration intervals are set. It is okay to compare the previous calibration data with the current calibration data and extend the next calibration interval if the accuracy is within the permissible range. If the accuracy is not acceptable, maintenance should be performed immediately and the calibration interval should be shortened. If the product is used for products with high measurement frequency and strict accuracy standards, the frequency of calibration may be increased to ensure safety and quality. It is important to set a period during which it can be judged that there is no problem in the quality control of the company’s products, considering the frequency of use of the measuring equipment, the usage environment, work manpower, personnel, cost, etc.
What are the Certificates Issued by Measuring Instrument Calibration ?
Calibration of measuring instruments is not just a matter of being performed, it is important to show evidence that the calibration results are valid. If the effectiveness of the calibration results cannot be proven, quality assurance cannot be carried out no matter how much calibration is performed. The requirements for an externally effective calibration include the following:
- Regular calibration is performed by qualified proofreaders
- Traceability of standard machines used for calibration has been established
- The calibration procedure is clear in the procedure manual
- There is a record to prove the calibration
Proofreading certificates are used to prove that calibration work that meets the above requirements has been performed. Proofreading certificates include calibration certificates and traceability system diagrams.
What is Measuring Instrument Calibration Certificate?
This is a document that describes the calibration results of the measuring equipment. The date of calibration, the name of the manufacturer that performed the calibration, inspection test items, inspection results, etc. are described. Normally, if you request calibration together with maintenance of the measuring equipment, it will be attached when you return it.
What is the Traceability System Chart of Calibration?
In order to clear the calibration required by ISO 9001, it is necessary to be traceable that the standard machine to be compared at the time of calibration conforms to international or national metrology standards. The traceability system diagram is a document that describes the calibration route of the equipment used for calibration. Going back to the top reveals what criteria were used for calibration. It is written so that you can see that if you trace it to the top, you will arrive at the International Metrology Standard or the National Metrology Standard.
These documents prove that the calibration has been performed to meet the standards required by ISO9001. Calibration is also necessary to prove the quality and accuracy of your products. Since customers may require the submission of calibration certificates and traceability system diagrams, it is essential to carry out proper calibration of measurement equipment.
ISO for Measuring Instrument Calibration
Testing laboratories and calibration bodies that calibrate instruments must meet the general requirements of ISO for their ability to perform specific tests or calibrations.
General requirements for the capabilities of laboratories and calibration laboratories
- General requirements – Fairness and confidentiality
- Structural requirements
- Resource requirements – General, personnel, facilities and environmental conditions, equipment, metrology traceability, externally provided products and services
- Process requirements – Confirmation of contract contents, method selection verification and validity confirmation, sampling, handling of items, technical records, uncertainty evaluation of measurement, guarantee of validity of results, report of results, complaints, nonconformity work, data management
- Management system requirements – Options, Management System Documents (Option A), Management System Document Management (Option A), Record Management (Option A), Risk and Opportunity Initiatives (Option A), Improvements (Option A), Corrective Actions (Option A), Internal audit (option A), management review (option A)