Product quality is the foundation of brand building, and brand development further improves product quality. How to make customers trust your product? A complete quality management system is essential. This article will present five key points on how to improve the effectiveness of a quality management system.
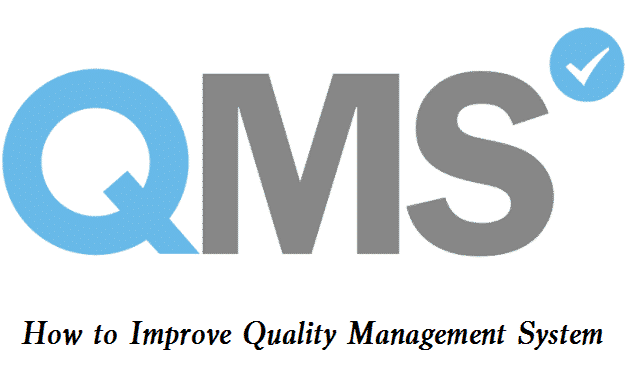
How to Improve the Effectiveness of Quality Management System
A quality management system refers to the management system that commands and controls the organization in terms of quality. It is a systematic quality management model established within the organization and necessary to achieve quality objectives. It is a strategic decision of the organization. Generally, it becomes the requirement of the internal quality management of the organization in a documented way, so how can we ensure the effectiveness of the quality management system?
1. Be sure to implement what is written in the document in practice. Because the purpose of preparing quality system documents is to standardize the work of employees, whether employees can consciously carry out work according to the requirements of procedure documents is one of the quantitative indicators to evaluate the effectiveness. Many certified enterprises will have the same feeling. It is easy to write documents but difficult to implement them. It is suggested that the quality record should be operated in the form of a table, which will achieve better-expected results..
2. Implement the traceability system inflow management. The quality of products and services is guaranteed through process work specifications. For any nonconforming products, the causes of nonconformities should be found out and effectively traced to the responsible person. Even if there is no punishment and only exposure, it can also play a good role in improving quality awareness. Focus on tracking the repeated nonconformities, and conduct factual education for employees in the form of quality cases and quality analysis meetings.
3. Focus on the quality cost to satisfy customers. Quality cost is one of the quantitative indicators to evaluate the level of quality management. The quality of a company without benefits can be imagined. Regarding customers as God, we should not only pay attention to the quality of products provided to customers but also have a good relationship with customers to make customers satisfied. In the process of enterprise operation, quality management should start from the actual situation of the enterprise, and can not blindly follow all the requirements put forward by customers. Some requirements beyond the enterprise’s ability to bear improvement should be resolved through communication.
4. Self-correction through rolling quality internal audit. Seriously carrying out quality internal audit is an important link of quality system management. We should be able to audit horizontally and vertically, cover the whole company and correct ourselves. There should be a mechanism to constantly find, solve and improve problems. Generally, an internal audit, based on the internal hierarchical relationship, usually does not audit the management. In fact, it is wrong. Because the management’s attitude towards quality will directly affect the employees’ attitude towards quality work.
5. The management should control the quality problems of the products and take a long-term view. When there is a contradiction between the quality control department and the production department, we should take quality as the first consideration and ensure the standard it should reach.