Our daily lives are full of rubber products. Rubber soles of shoes, belts, hoses, tubes, tires, to name a few. There are various processing processes before they are distributed as rubber products.
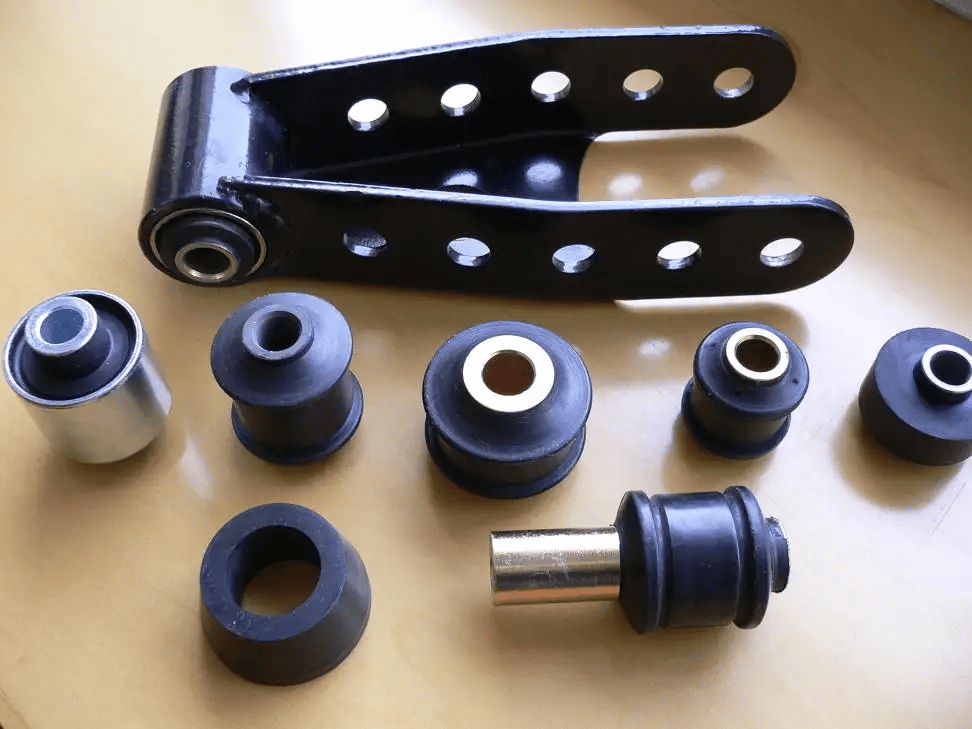
In this article, we will focus on how to process rubber and examples of defects that can occur during manufacturing. We have summarized the basic matters so that it is easy to understand even for those who do not have basic knowledge about rubber processing. If you want to acquire knowledge about rubber processing, please read to the end.
What Is Rubber Processing?
As the name suggests, rubber processing is the process of processing rubber material and molding it into the desired shape. Rubber materials come in various shapes such as plates, strings, and blocks. By modifying these materials, we will make them into the desired shape.
Rubber is soft and bounces easily, and has the property of stretching well when pressure and force are applied. Even if you stretch it with force, it will return to its original state if you release it, and it is a material characterized by elasticity.
On the other hand, the weakness of rubber is that the material is prone to deterioration and it is difficult to predict the time of deterioration. As a countermeasure, it is considered to apply an anti-aging agent to the processed product.
Rubber material can be cut with a blade like a cutter, but it is difficult to finish it cleanly because when cut with a blade, it is deformed by the applied force. Therefore, it is necessary to use a processing method that matches the shape of the rubber.
From the next chapter onwards, we will explain the rubber processing process and specific processing methods.
Main Processing Processes Of Rubber
Here, we will look at the main processing processes of rubber. The following processes are required to finish rubber products.
1. Design
We determine the types of chemicals and other materials to be mixed in the raw rubber, as well as usage fees, and summarize them in a compounding table.
2. Roll (completion of material)
We measure the compounding agent based on the compounding table. Some products use more than 10 types of compounding agents, so you need to be careful to make sure you don’t make mistakes. After weighing the chemicals, the materials are completed by refining them using a polymer or other machine.
3. Extrusion
Depending on the product, this process is performed to prepare the preparation material.
4. Inspection
When the material is finished, we inspect and test it to make sure it is as designed. We use multiple evaluation testing machines to conduct tests from various angles.
5. Molding
If there are no problems with the material, we move on to molding. It is poured into a mold to form a shape or cut into a predetermined size.
6. Secondary vulcanization
The cut and molded rubber material is heated by pressurized steam in a cylindrical pressure-resistant can (direct steam vulcanization) and indirectly heated (hot air vulcanization) in a 20-vulcanized can. Vulcanization is the process of mixing and heating sulfur in a rubber material to create a network of molecules.
7. Finishing touches
Depending on the product, we will finish by cutting off excess parts.
8. Inspection
We inspect the finished product visually or by machine to check for problems. The above is the general processing process (manufacturing process) of rubber products. The process may differ depending on the product.
In the next chapter and beyond, we will introduce the specific contents of the processing method.
Rubber Processing Methods
Molding process
Molding is processing to create shapes. There are various processing methods, but here we will introduce 5 types.
Compression molding
This is the most used method of rubber molding. Rubber material is poured into a mold and molded by applying heat and pressure. The advantage is that the cost of the mold is low and the equipment is easy to install and operate. On the other hand, there is a disadvantage that there are many burrs. It is used in the manufacture of hoses, tubes, packings, etc.
Extrusion
This is a method of making long products with the same cross-sectional shape by melting and fluidizing the material in an extruder and applying pressure to continuously advance it with a screw. It is suitable for the manufacture of pipes, hoses, tubes, etc.
Press-fit molding
This is a method of molding rubber material by placing it in a pot and heating and pressurizing. It has high dimensional accuracy and can be molded even with complex shapes. If the structure is complex, the mold will be more expensive and the amount of scrap will increase. This method is used for precision machinery parts and OA equipment parts.
Machining
It is a molding method that uses drilling machines, general-purpose coatings, NC plates, etc. There is no mold cost, and it is suitable for small production volumes. Due to the large number of handmade elements, it is not suitable for cases where strict precision is required, but it can be used for a wide range of products. This method is used in the manufacture of packings, gasket pipes, etc.
This is a method in which pressure is applied to a rubber material that has been heated and melted, and it is poured into a mold. Mold tightening, injection, vulcanization, etc. are performed step by step. Although it costs more than other methods, unmanned manufacturing is possible if the material can be supplied automatically. It is used in a wide range of products such as machine parts, mass-produced products, and OA equipment parts.
Cutting
Cutting is a method of cutting using machines such as lathes and milling machines, or by cutting by hand by craftsmen to finish the desired shape. By the way, when cutting by hand, a rokuro is used, but since it is difficult to maintain the angle of accuracy, a machine is almost always used. The advantage of cutting is that it does not use molds, so there is no initial cost or time required for mold manufacturing. It is also suitable for small-lot production.
Cutting is suitable for making products and prototypes with many standard changes. Some shapes cannot be handled by cutting, but complex shapes that are difficult to achieve by machining with molds can be achieved.
On the other hand, it is not suitable for mass production because it does not use molds. The production cost per piece tends to be expensive, so if you have a large number of pieces, it would be wise to choose another processing method. In addition, there are various types of cutting, so we will briefly introduce the specific methods.
Waterjet processing
This is a method of cutting by applying high water pressure to the rubber material. Since it can be cut from all angles, it is easy to handle complex shapes.
This is a method of rotating the blade attached to the milling machine and cutting while applying the material to the blade. It is used for thread making and cutting outer and inner diameters.
Rokuro processing
It is a method of rotating the fixed rubber material and cutting it with a whetstone. It is used to finish molded materials to some extent.
Drilling machine processing
This is a method of grinding rubber material by rotating a drill set on a drilling machine. Since the set material cannot be moved, it is mainly used for drilling.
Cutting
This is a method of pushing the rubber material set in the cutting machine with a blade. It is suitable for cutting in a straight line.
Adhesive processing
It is a method of connecting multiple materials such as rubber to each other or rubber and metal. It is bonded using adhesive, double-sided tape, or vulcanization bonding.
Punching
Punching is a punching method using a mold with a blade. When punching, use a press or hand press. It is easy to understand the image of pushing the mold into the material like a cookie die-cutting and hollowing it out.
The advantages of punching processing are that it can be done without cost, there is no need for large-scale equipment, many identical shapes can be manufactured, and even small quantities can be handled.
However, there are disadvantages such as being able to create only flat shapes, using only materials that match the shape of the machine, and low dimensional accuracy. It is a relatively inexpensive processing method, but it is also important to remember that it costs a mold.
We will also briefly introduce the specific method of punching:
Biku die-cutting
This is a method of attaching a blade to a wooden mold and performing punching. Compared to molds, it can be handled at a lower cost and in a short period of time.
Die stamping
It is a method of processing using a mold and a press. It is suitable for mass production and is characterized by high processing accuracy. However, there is a disadvantage that the cost is relatively large, such as equipment costs.
Super cutter removal
It is a method of automatic cutting using a biku type. It has high dimensional accuracy and is suitable for mass production.
Punch removal
It is a method of punching using a punch. The punch itself can be purchased at home centers, etc., so it can be done at a relatively low cost. Since the blade deteriorates as it is used, it is not suitable for mass production.
Possible Defects In The Processing Of Rubber
Various defects can occur in the rubber processing process. Possible defects differ depending on the machining method, but for example, in the cutting process, dimensional deviations and burrs on the cutting surface occur.
- In addition, if foreign matter is mixed into the rubber material regardless of the processing method, the quality of the finished product will be lowered. If packing is contaminated with foreign matter, the sealing function will deteriorate and cause water leakage.
- If a break occurs in the processing process, not only will the appearance of the product be lost, but it will not be able to function as a proper product.
- In addition, although it is an unfamiliar word, “bad luck” may occur. It is a state in which the positions of the joints of the molds do not match at the top and bottom.
- If the mold is misaligned at the top and bottom, even if it is molded, the top and bottom will be misaligned, which will lead to the occurrence of defective products as well as dimensional misalignment and foreign matter contamination. Since we often outsource haha to manufacturers, we may not be able to handle it ourselves. It is necessary to check the mold inspection carefully to see if there are any gaps.
- There are other types of defects in the rubber processing process. It will be easier to deal with what kind of defects are likely to occur in each process if you summarize the countermeasures when they occur.
Inspection Methods For Rubber Products
In the previous chapter, we introduced defects that can occur in the rubber processing process, but it is important to prevent the outflow of defective products by inspecting them.
- If the dimensions are defective, we will check the model dimensions, and if they are NG, we will correct or remanufacture. Even if the mold is finished accurately, dimensional defects will occur. It is also important to check the amount of heat charged in the mold used for compression. In addition, it is necessary to pay attention to the dimensions because the dimensions change depending on the type of molding machine, heat temperature, time and pressure.
- Defective cuts are detected by visual inspection. However, defects cannot often be detected by visual inspection alone, and the product is checked by pulling or bending it during the quality inspection.
- If there are too many defective cuts, it will be necessary to change the mold. If a finishing error causes cuts, it may be necessary to improve the skills of the operator.
- In addition, visual inspection is generally performed for the inspection of foreign matter in rubber materials. Efficient inspections require the development of skilled inspectors. You may also use a magnifier or optical microscope.
- It is almost impossible to completely prevent foreign matter contamination even if countermeasures are taken. In a normal environment, various foreign matter is suspended in the air, and even if a clean room is established, it will be difficult to reduce foreign matter contamination to zero.
- While it is necessary to make efforts to eliminate foreign matter, it is also important to improve the quality and efficiency of inspection so that we can respond quickly when foreign matter is found.
Summary
Various processing methods are used in the process of manufacturing rubber products. However, each has its advantages and disadvantages, and it is difficult to completely prevent the occurrence of defective products.
Visual inspections are indispensable to prevent the outflow of defective products, but it is becoming difficult for inspectors to conduct accurate inspections due to labor shortages and difficulty in inspections. Therefore, visual inspection using AI has been attracting attention in recent years. Please take a look at the document that summarizes how to automate visual inspection.