Processes
- Polymer Processing
- Injection Molding Insert Molding Blow Molding Over Molding Metal Injection Molding Thermoforming
- Metal Casting
- Die Casting Castings & Forgings Wax Casting Lost Wax Casting Grey Iron Castings Centrifugal Casting Investment Casting Permanent Mold Sand Casting Shell Mold Casting Aluminum Investment Casting Brass Investment Casting Steel Investment Castings Titanium Investment Casting
- Machining
- Milling Turning EDM machining CNC Engraving Hole-making Tap Size Chart Drill Size Chart 5 axis machining Micro Machining CNC Cutting Metal Processes Ceramic Manufacturing Swiss Precision Machining
Materials
Milling Definition – What is Milling?
Milling is the most common machining process, which can produce various complex shapes such as slots and grooves through material removal by rotary cutters. In the process of milling or CNC milling, the workpiece is secured to the fixture that is attached to a platform inside the machine tool, high-speed milling cutter is used to cut out the required shape and features. By feeding the workpiece to the rotating cutter, the material is cut away from the blank in the form of small chips.
Milling operations can be done with a variety of machine tools, the original and most typical type is milling machines, with the advent of CNC (Computer Numerical Control) in the 1960s, milling machines evolved into machining centers. CNC milling machines are composed of automatic tools changers, tools magazines, coolant systems, CNC control, and enclosures. There is a wide variety of milling cutter types and materials that serve a specific purpose. Milling cutters can be solid carbide, high-speed steel, or adjustable inserts.
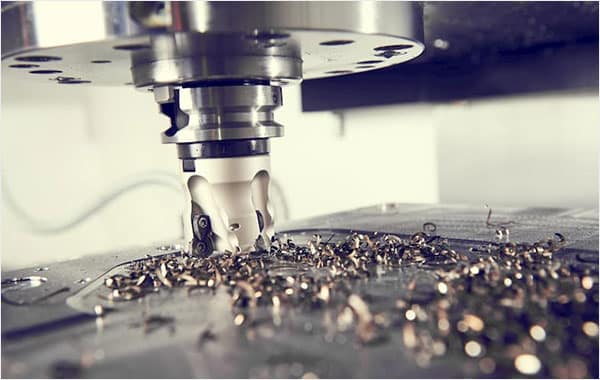
Milling Applications – What is Milling Used for?
Milling is a versatile metal removal process capable of generating varying geometries. Milling is a technique that typically used to manufacture milling parts that are axially symmetric and have many features, like slots, pockets, grooves, etc. The milling process can also manufacture industrial components used in limited quantities completely, such as prototypes. Different tooling production is also a popular use of milling. The CNC machining factory also uses milling as secondary processing, adding or refining features to parts manufactured by different processes.
Milling Equipment – What is a Milling Machine & Main Parts of Milling Machine
A milling machine is a machine tool that rotates a cutting tool with a number of cutting edges symmetrically arranged about its axis, the workpiece is held in a vise clamped to a table that can move in three perpendicular directions. Milling machines can be designed to various sizes and specifications, here are some basic parts of a milling machine. These components of the milling machine can be oriented either vertically or horizontally, creating two very distinct forms of milling machine: horizontal milling machine and vertical milling machine.
- Base: sits on the ground and supports all of the other parts of the machine.
- Column: attached to the base vertically and connects other components.
- Table: the part to be milled is mounted onto the worktable, which often has a T-shaped slot. The fixture used to hold the piece is secured into the T-slot. The table offers horizontal motion of the part along the X-axis by sliding along the saddle beneath it.
- Saddle: supports the table and allows its longitudinal motion. The saddle can provide horizontal motion of the part along the Y-axis by sliding transversely along another platform called the knee.
- Knee: supports the saddle and table. The knee can move vertically along the column, to make the workpiece move vertically.
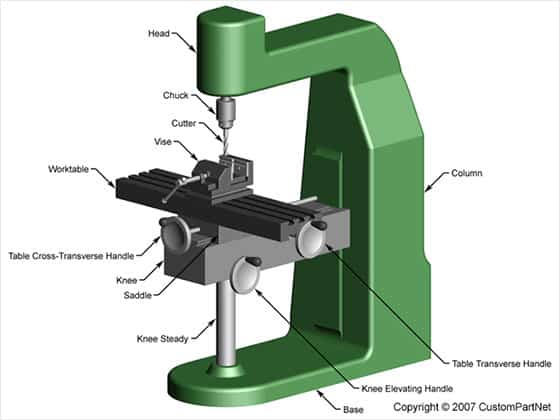
Milling Tooling – Types of Milling Cutting Tools
CNC milling operation requires a sharp cutting tool that will be rotated by the spindle. A milling cutter is usually a cylindrical tool with teeth around the outside. The gaps between the teeth are called flutes, which allow material debris to move from the workpiece. The teeth can be straight along the side of the tool but are more commonly arranged in the helix. The helix angle reduces the load on the teeth by distributing the force. There are many kinds of cutting tools that can be used in milling operations. Their diameters, lengths, cutting shapes, and materials are very different, and they also vary according to their directions, whether they are used horizontally or vertically. Therefore, a variety of characteristics can be formed with milling services. Common milling cutter types:
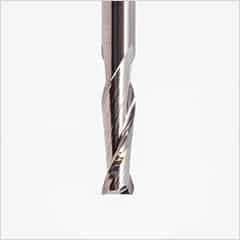
Flat end mill
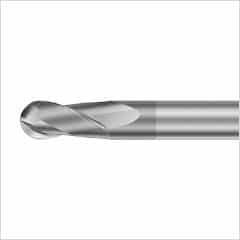
Ball end mill
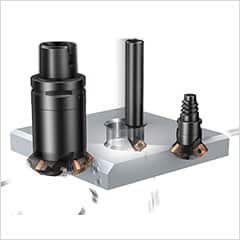
Chamfer mill
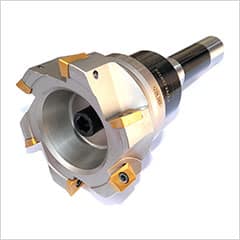
Face mill
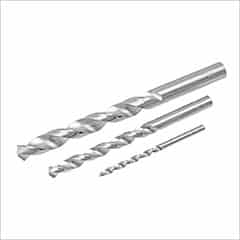
Twist drill
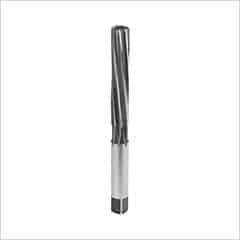
Reamer
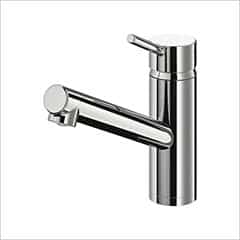
Tap
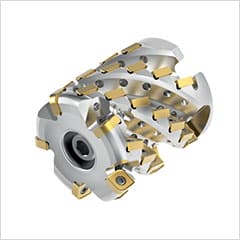
Helical mill
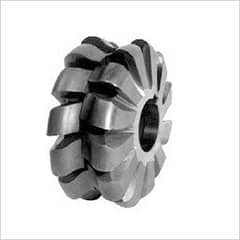
Form relieved mill
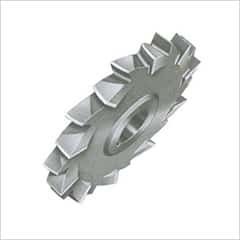
Staggered tooth mill
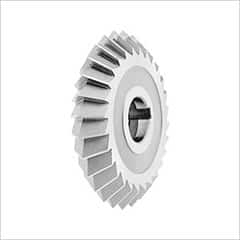
Double angle mill
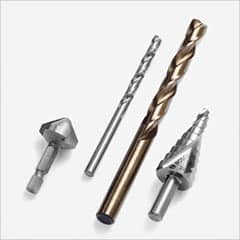
High-speed steel (HSS)
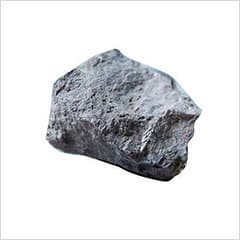
Carbide
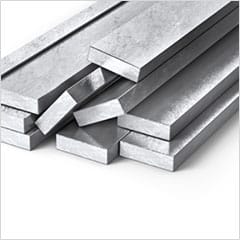
Carbon steel
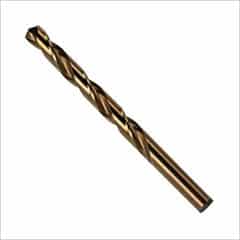
Cobalt high-speed steel
Milling Capabilities | ||
---|---|---|
Typical | Feasible | |
Shapes | Solid: Cubic Solid: Complex |
Flat Thin-walled: Cylindrical Thin-walled: Cubic Thin-walled: Complex Solid: Cylindrical |
Materials | Alloy Steel Carbon Steel Cast Iron Stainless Steel Aluminum Copper Zinc |
Ceramics Composites Lead Nickel Tin Titanium Elastomer Thermoplastics Thermosets |
Max wall thickness | 0.04 – 40 in. | 0.04 – 72 in. |
Advantages | All materials compatible Very good tolerances Short lead times |
|
Disadvantages | Limited shape complexity Part may require several operations and machinery |
|
Applications | Machine components, engine components |