You not only should deliver your prototypes in a short delivery time, but also carry out third-party inspections every day so that you can deliver high-quality prototypes.
CNC Machining is performed based on the drawing, and it is judged by measurement whether it is completed according to the drawing. Since the drawing supports the “target value” and the “tolerance” that indicates the range of allowable deviation, the pass range is between the minimum allowable dimension (lower limit value) and the maximum allowable dimension (upper limit value). Therefore, Dimensional Inspection is one of the means to ensure quality after prototypes are completed.
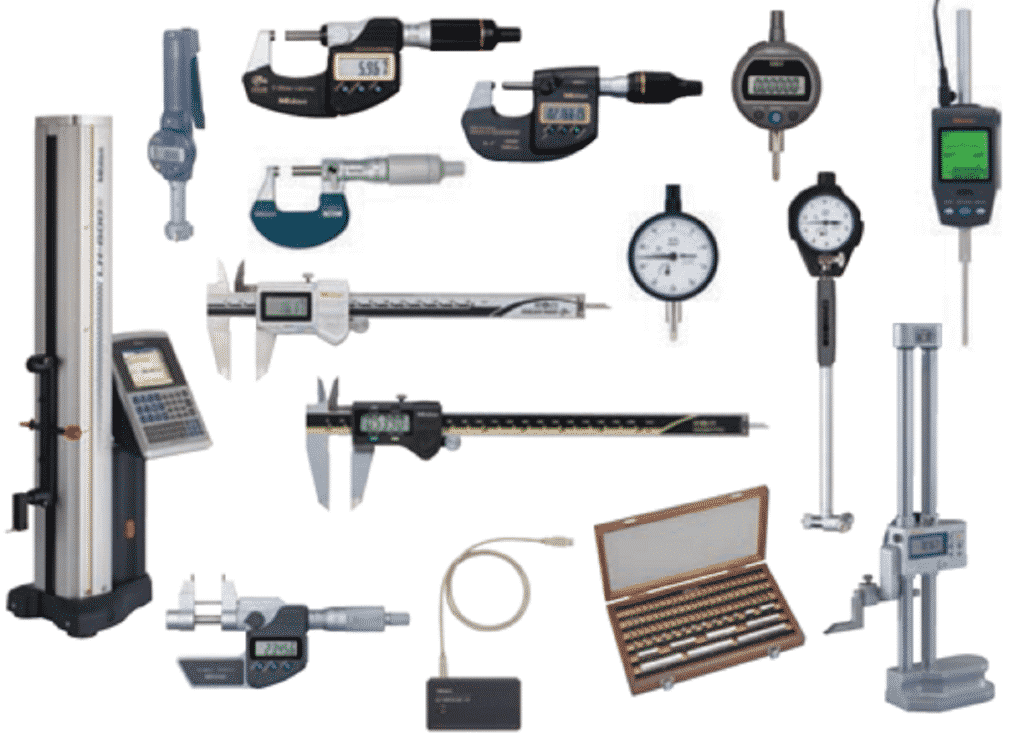
Value of Accurate Dimensional Inspection – Manufacturing Quality Guarantee
The true value is known only to God, as the measured value always contains an error. There are various causes of error, such as variations in the measuring instrument itself, the effects of temperature changes, memory reading misalignment, and foreign matter adhering to the measurement location. In order to reduce this error, we will provide education and training on how to handle measuring instruments and prepare a measurement environment. The error of the measuring instrument itself is corrected based on the measuring instrument whose error is as close to zero as possible. This is called “calibration”. By performing calibration on a regular basis, highly reliable measurement can be performed.
Types of Dimensional Measuring Instruments
Caliper Gauge
Calipers are the most frequently used measuring tools in machining plants. It consists of a main scale and a vernier scale, and the resolution (the smallest readable difference that can be discriminated by the measuring instrument) is 0.05 mm, but measurement errors are likely to occur, and the guarantee system is about ± 0.2. Outer diameter measurement, inner diameter measurement, depth measurement, and step measurement are possible.
The measurement range is 150 mm and 300 mm, and there are even larger ones.
It is difficult to read the measured values directly with a vernier scale unless you are accustomed to it, and calipers with dials and digital calipers are widespread.
Micrometer
It is a measuring device used for precise length measurement using precision screw rotation. Measure by sandwiching the object to be measured between the unbuilt and the spindle. Use the ratchet stop to measure so that no force is applied to the object to be measured. It is difficult to read a vernier scale called a thimble, and recently there is also a digital micrometer.
The resolution is 0.01 mm, but be aware that it is affected by temperature and body temperature.
Depending on the application, there are point micrometer, three-point micrometer, depth micrometer, inside micrometer and so on.
Dial Gauge Indicator
It consists of a dial with a circular scale and a spindle, and is used by attaching it to a magnet stand. Instead of using a measuring instrument that directly reads the length of the object to be measured, for example, adjust the zero point with a 30 mm block gauge, sandwich the 30 mm object, and measure as a 30 ± dial gauge reading. At the assembly site, touch the side of the shaft with a magnet stand, rotate the shaft once, read the value of ±, and adjust it so that the value is minimized. This is called the core.
The resolution is available in 0.01mm and 0.0001mm.
Height Gauge
It is an indispensable measuring instrument for machining machine parts, measuring dies and jigs, and marking work. In addition, a standard surface plate is required for various settings and marking work. The scale part with the main scale, the base part of the scale, the Banya scale integrated with the Toscan (marking tool), or digitally enables accurate reading of measured values.
The minimum reading is 0.01 mm, 0.02 mm, or 0.05 mm depending on the size of the main body.
In addition, there are some that can measure parallelism, flatness, and straightness by attaching a lever type dial gauge (dial indicator) using a dial indicator holder or the like.
Projector
It is a kind of optical measuring instrument, and its measurement principle is similar to that of an optical microscope. By placing the object on a table and shining light from below, the shadow of the object is projected on the screen. Align the shadow on the screen with the reference line, etc., move the stage manually, measure the dimensions by the amount of movement, or superimpose it on the enlarged drawing and visually compare the difference with the edge (contour).
Some large projectors have screens larger than 1 m in diameter.
In this way, the projector must visually determine the edge from the shadow of the object physically projected on the screen. In addition, the physical movement amount and physical scale of the stage are visually confirmed and measured. Therefore, measurement requires skill and requires a lot of man-hours.
It is a measuring machine that can measure the solid to be measured three-dimensionally. It is roughly divided into contact type and non-contact type.
In the contact type, the object to be measured is measured with a stylus called a probe, and in the non-contact type, a scanning laser probe or optics is used to measure without contacting the object to be measured. The product is measured by points or lines, and the obtained numerical values are used to detect three-dimensional coordinate values. You can combine point cloud data to create surface elements and circle elements to create cylindrical elements.
You can also find the inner and outer diameters of a circle, and geometric tolerances such as flatness, parallelism, squareness, and position.
These detections are processed by the connected computer. However, due to its precision, the measurement conditions are strict, it is easily affected by temperature, and a constant temperature room is required. And the measured object also needs to reach the temperature of the constant temperature room.
Image Dimension Measuring Machine
The measurement principle of an image dimension measuring machine is completely different from that of a projector. First, the image sensor (camera) captures the object as an image.
Since the dimensions are calculated and measured using the pixels of the image for dimension measurement, the higher the resolution of the image that can be captured, the higher the accuracy of capturing the edges, and more accurate measurement becomes possible.
In addition, it is possible to detect the edge of the object by image processing, recognize the pattern, correct the position and orientation, and automatically control the stage. Therefore, in recent years, measurement using an image size measuring device has become the mainstream rather than a projector.
Limit Gauge
The limit gauge may not be a measuring instrument, but when mass-producing fitting parts, it is not efficient to measure the actual product by the above measurement method, so use the limit gauge. Use to inspect fit dimensions. There are hole gauges and shaft gauges.
Since a large amount of objects are handled, the limit gauge needs to have accurate accuracy and hardness as a jig.