Processes
- Polymer Processing
- Injection Molding Insert Molding Blow Molding Over Molding Metal Injection Molding Thermoforming
- Metal Casting
- Die Casting Castings & Forgings Wax Casting Lost Wax Casting Grey Iron Castings Centrifugal Casting Investment Casting Permanent Mold Sand Casting Shell Mold Casting Aluminum Investment Casting Brass Investment Casting Steel Investment Castings Titanium Investment Casting
- Machining
- Milling Turning EDM machining CNC Engraving Hole-making Tap Size Chart Drill Size Chart 5 axis machining Micro Machining CNC Cutting Metal Processes Ceramic Manufacturing Swiss Precision Machining
Materials
What is EDM Machining? – Electrical Discharge Machining Process
EDM (Electrical Discharge Machining), also known as spark machining, wire erosion, wire burning, and spark eroding, is a metal fabrication process in which a series of rapidly recurring current discharges between two electrodes to remove excess material from the workpiece and get the desired shape. The electrodes are separated by a dielectric liquid and applied with a voltage, one of them is the tool or electrode, and another electrode is the workpiece. EDM machining is common in tool and mold making.
How Does EDM Machining Work?
The EDM process involves the electrical discharges from soft metal tools to disintegrate conductive materials such as steel. Both electrodes (tool and material) have to be submerged in a dielectric fluid, in the small gap between the electrodes, a discharge occurs that removes material through melting and vaporizing. When the tool electrode is lowered and getting closer to the workpiece, the spark gap increases until it approaches the breakdown volume. The discharge causes heating and melts a small amount of material. With the steady flow of the medium fluid, the excess material is removed. The workpiece and tool do not touch, and the fluid in which this discharge occurs is not conductive, the process relies on the ability of controlled electric sparks to erode the material. However, the amount of removed material of a single spark is small, the overall speed of EDM machining is not very fast.
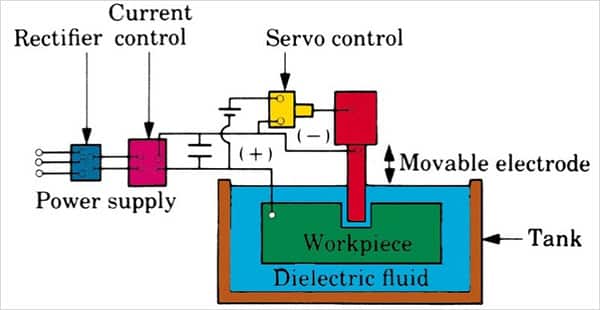
Types of Electrical Discharge Machining
- Wire EDM, also known as WEDM, in the wire EDM process, a thin single-strand wire works as the electrode, and the wire are continuously fed from the automatic feed with the spool during the process, the electrical discharge is created between the wire and workpiece, as the spark moves across the gap, the material is then removed from the part. Because the discharge will be eroded and compromised by wire and workpiece, the WEDM machine tool uses the spool filled with wire, which will move continuously, thus adding a new discharge path in the cutting. Wire EDM process can easily produce precision parts out of hard conductive materials.
- Sinker EDM, also called plunge EDM, ram EDM, and conventional EDM, produces components by eroding materials in the path of the EDM tool using electrical discharges or sparks that can produce heat anywhere, the electrode is used to create a conductive path and cut the material into the desired shape. There is no actual contact between the electrode and the workpiece because corrosion is a reaction to the generated current. This process takes place in a dielectric fluid that allows conduction. The liquid is always used to flush debris during the process to obtain a clean, burr-free edge. Plunge EDM is suitable for injection mold tooling, small hole drilling, washers, keyways, etc. Plunge EDM does not require a pre-drilled hole to feed the wire into. Common plunge EDM electrodes are graphite, copper tungsten, and brass, which makes it different from wire EDM, in addition, plunge EDM has 3D capacities.
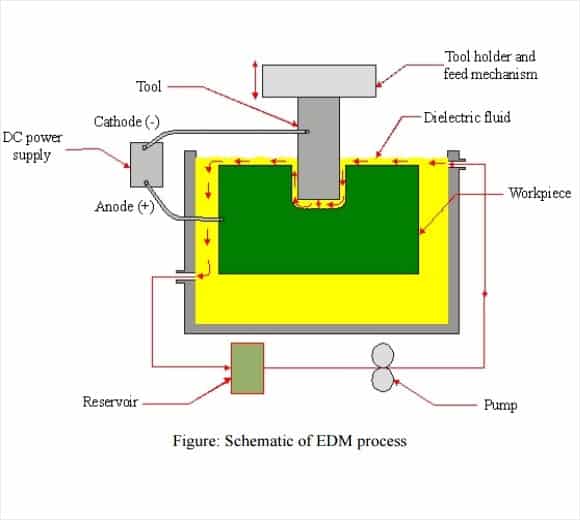
- Hole Drilling EDM, this process is used for drilling, and capable of drilling very small deep holes, during hole drilling EDM, the electrodes are tubular and the dielectric fluid is fed through electrodes themselves. Regardless of the type of metal, high-precision holes can be drilled.
Advantages of EDM Machining
- It can produce complex shapes, which is difficult for conventional machining methods.
- It can be used on any material as long as it is conductive, including tungsten carbide and titanium.
- Fragile outlines are easier to produce due to the lack of mechanical force put into the workpiece.
- Tolerance of ±0.005 and a good surface finish can be achieved economically.
- No distortion or vibration of tool or workpiece, as there no physical contact between the tool and piece.
- It allows sharp internal corners, deep ribs, narrow slots, and deep processing.
- It can be applied on hardened material, which can avoid any deformation from heat treatment
Disadvantages EDM Machining
- High power consumption
- Excessive tool wear during machining
- Only applicable for metallic or conductive material
- Material removal rate or MMR is very low
- Not suited for high-volume production
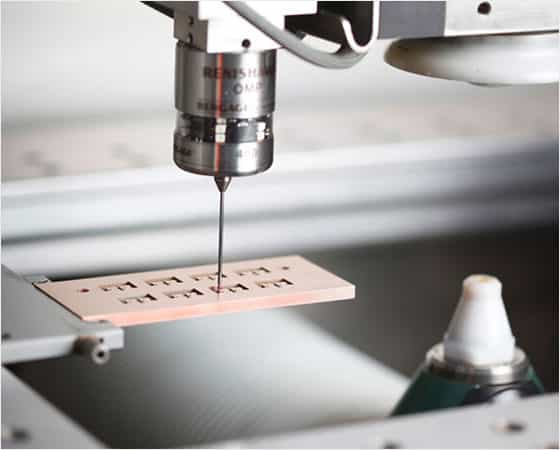
Applications of EDM Process
EDM is a non-traditional process, which can be combined with CNC technology and commonly used for low volume production such as prototypes. Electrical discharge machining has become the solution of various processes like turning, drilling, and milling. Automotive and aerospace are typical uses of EDM machined parts.
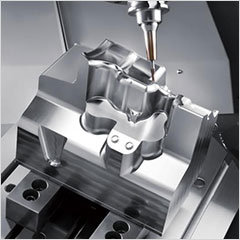
Die and mold making
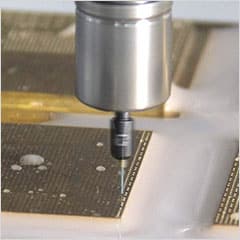
Drilling of micro holes
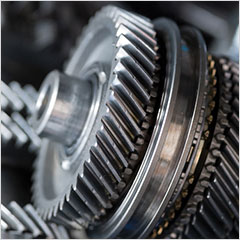
Manufacturing of gears
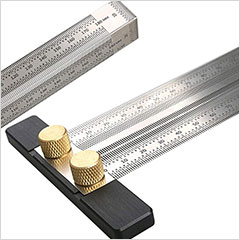
Fine holes or slots
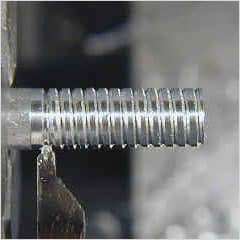
Thread cutting
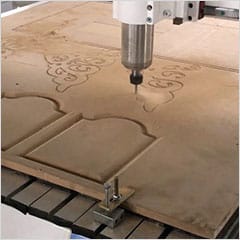
Engraving operations
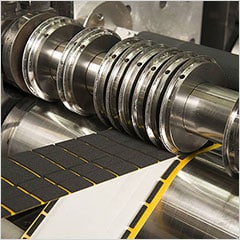
Rotary form cutting